With combined (anchor) forces
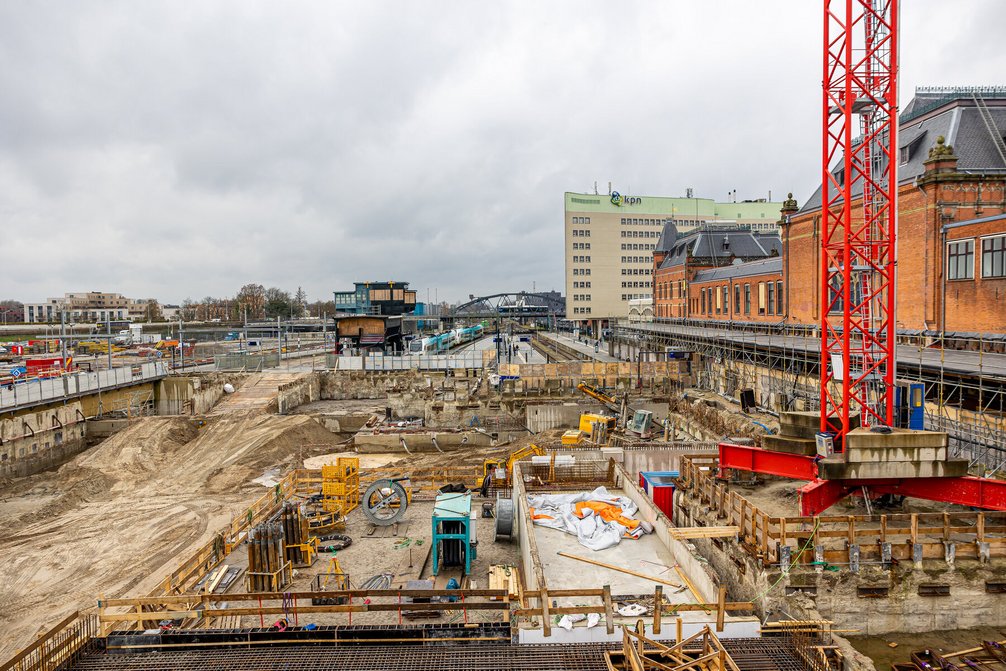
Groningen station is currently being redesigned so that travelers at the most important rail and bus hub in the northern Netherlands can reach their destination even faster and more conveniently. But it will still be a while before that happens. For now, the civil engineering work is underway, in which the anchors from BBV Systems are playing a key role. "After we were able to prove what our Multibond anchors are capable of in phase 1 of the Groningen station construction project, we were also called in for phase 2 - with a particularly challenging task," emphasizes Thomas Riss, Site Manager Geotechnics at BBV Systems.
Anchors in new dimensions
The Multibond anchors for the second construction phase are longer, larger and heavier than all anchors supplied by BBV Systems to date. They are also designed for a service life of 50 to 100 years, electrically insulated and equipped with measuring sensors for permanent monitoring of the anchor forces. "All in all, these are anchors that have never been seen before in Germany and probably also in the Netherlands and throughout Europe."
New paths in production
In order to realize them, BBV Systems took paths that were new even for the highly innovative company. It quickly became clear that the usual manufacturing steps and production processes would not work for the construction of these anchors. "We had to rethink and redesign everything. This presented me and my colleagues in production with challenges that were not commonplace."
Production line adapted
Production lines were extended and relocated and established and proven processes were adapted. One example: Due to the high inherent weight of the anchor and the sensitivity of the protective tube, it was not possible to use a heavy-duty winch to pull up the corrosion-protection collecting sleeve as usual, so BBV Systems quickly developed new auxiliary constructions. Another example is the construction of a 50 m long low-friction trough, which was designed to minimize deformation of the cladding tube when rolling up the up to 47 m long and up to 1,200 kg heavy Multibond anchors onto drums.
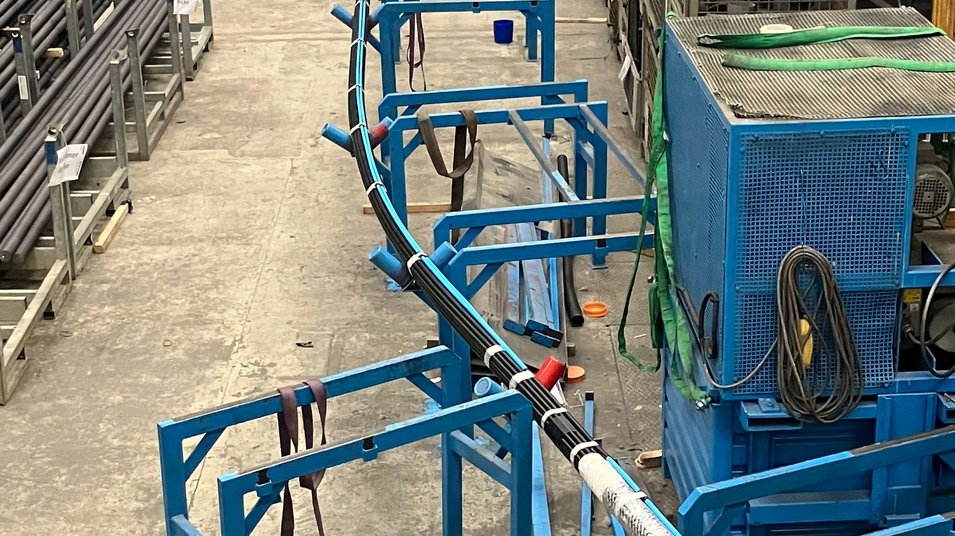
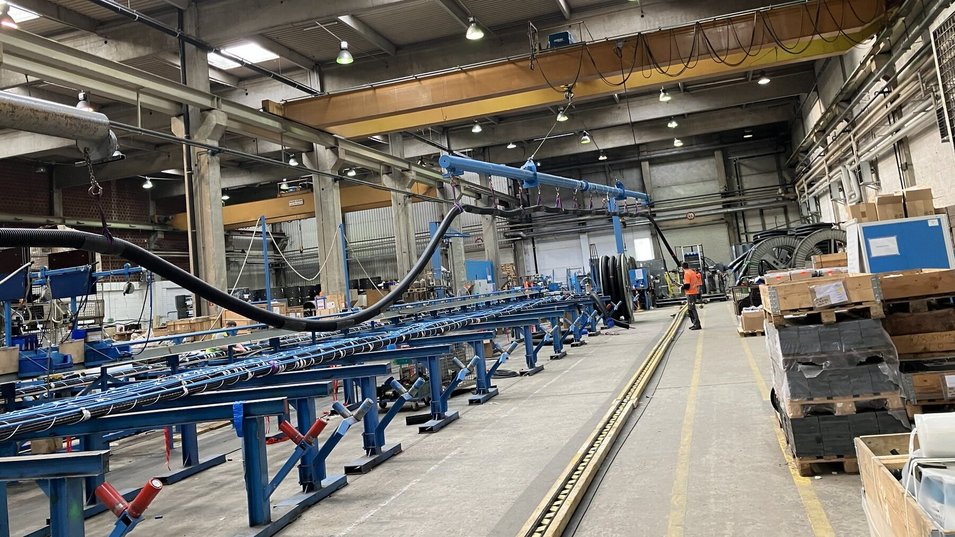
Achieving top performance together
For Thomas Riss, Groningen Phase 2 is a success story - both for BBV Systems and for the patented Multibond anchor, as well as for his team. "In order to develop the solution, an open exchange between production and project management was necessary. Everyone was able to contribute their ideas, experience and expertise - regardless of any hierarchy."
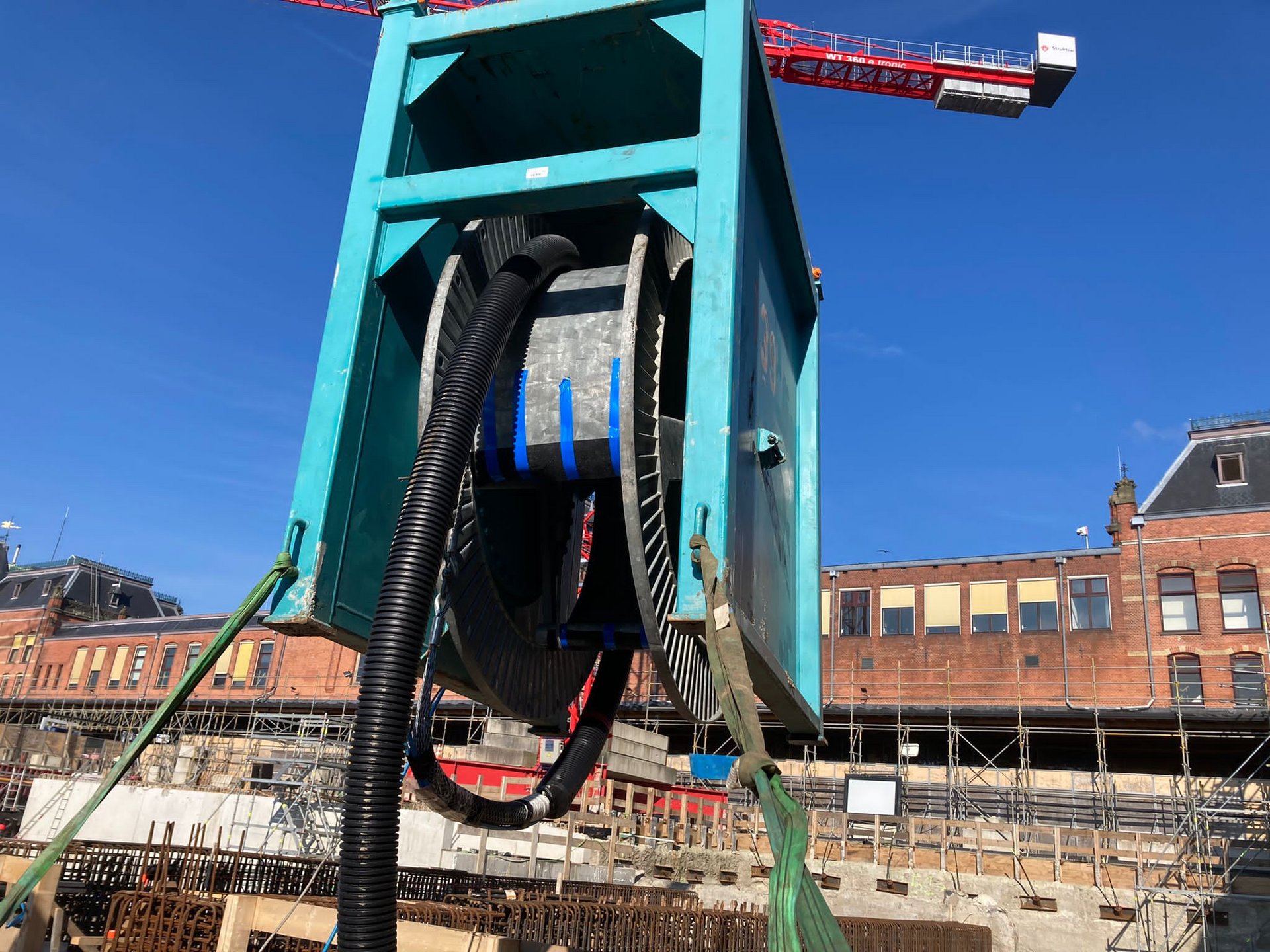
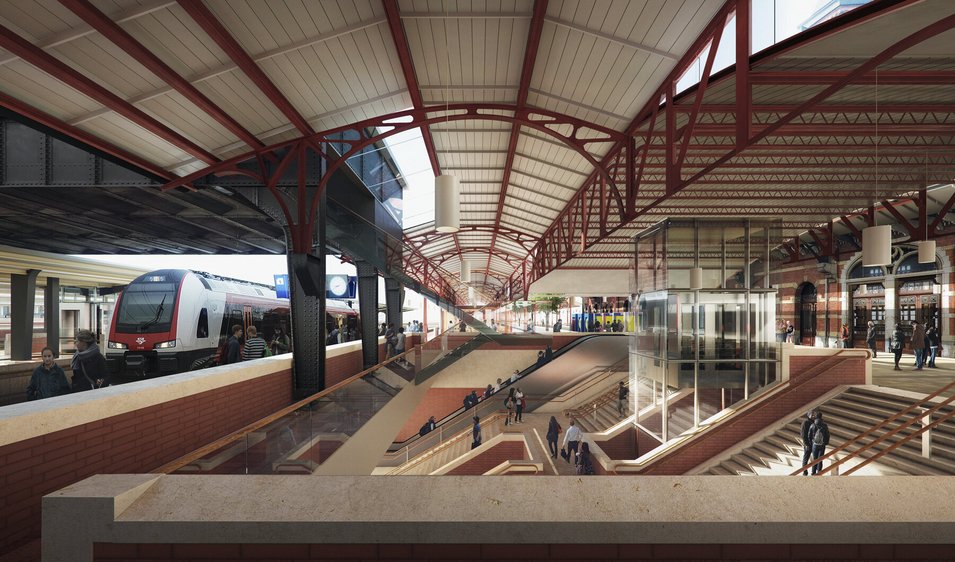
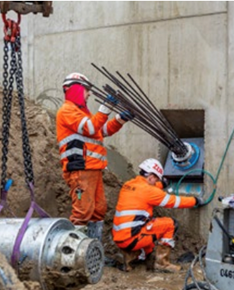
On a good foundation
The team was unanimous: if there is one step forward, then it is together. However, it was not only within the company, but also between BBV Systems, the client Züblin Spezialtiefbau GmbH and all the companies involved: "It's great to see how large and complex projects can succeed in this way." The customer's feedback that each of the supplied anchors was able to apply and maintain the required characteristic values in the form of forces speaks for itself. Thanks to the anchors from BBV Systems, it has a solid foundation.
How did the collaboration with BBV Systems for Groningen Phase 2 go from your point of view?
The collaboration could not have gone better. Thanks to the open and solution-oriented communication on both sides, we were able to master all the special features in production and in manufacturing on the construction site compared to conventionally dimensioned grouted anchors.
What was special about this collaboration?
The cross-company team spirit and the determination of everyone involved to realize these very special anchors in the best possible way.
How satisfied are you with the result?
The client received the anchors he had planned and we can be very proud of the performance of everyone involved.
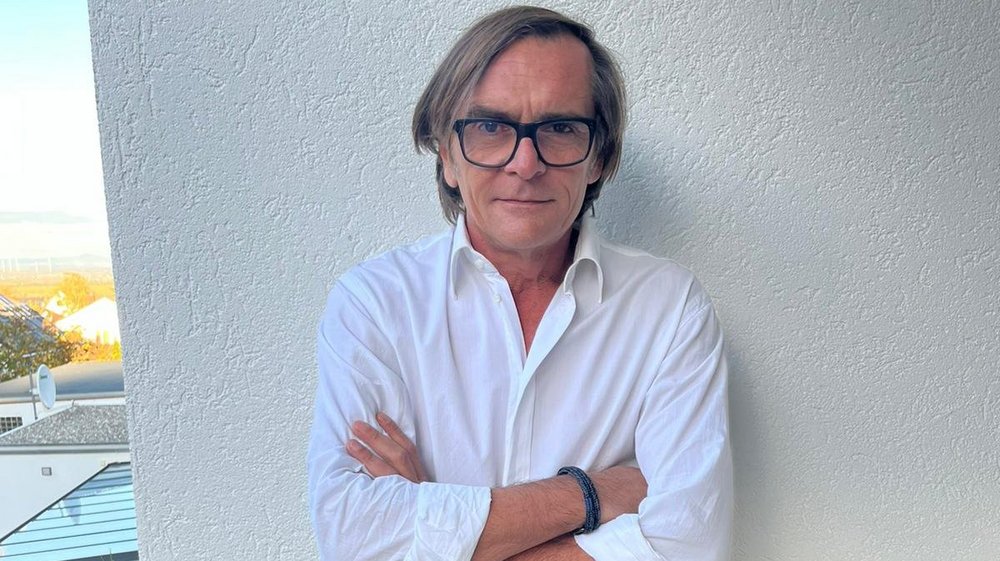
"An effective tool for soils with low bearing capacity"
Interview with Thomas Riss, Head of Geotechnical Engineering at BBV Systems
For the laymen among us: Why do you need anchors?
Just imagine: We are standing opposite each other and you have the task of preventing me from falling over if I let myself fall backwards. You grab me by my jacket and use the strength in your arms to hold me down. Our anchors work exactly according to this principle of pretensioning force - except that instead of a person, they prevent a building pit wall from falling over and we are dealing with completely different dimensions. You could attach a 220-ton jumbo jet to the anchors we used at Groningen station and the anchor would not be pulled out of the ground.
What is the main reason for using Multibond anchors at Groningen station? Our Multibond anchors have been designed for soils with low load-bearing capacity such as those found at Groningen Station. Compared to classic grouted anchors, our graduated anchors are capable of doubling or even tripling the anchor load-bearing capacity under comparable conditions. We therefore provide our customers with a particularly effective tool.
What does this mean for sustainability in construction?
The final depth at which the base of the excavation is poured can be achieved more quickly and more energy-efficiently thanks to Multibond anchors. This is achieved by saving on anchors, drilling meters and intermediate excavation levels, which conserves resources. In the Simon-Gatzweiler-Platz construction project in Düsseldorf, for example, CO₂ emissions were halved by switching to Multibond. The anchors at Groningen station are equipped with sensors.
What are they used for?
The sensors are used to permanently monitor the anchor forces. This monitoring is particularly useful for anchors that are intended to remain fully load-bearing in the ground for 50 to 100 years, as is the case here.