Zone de convergence en montagne
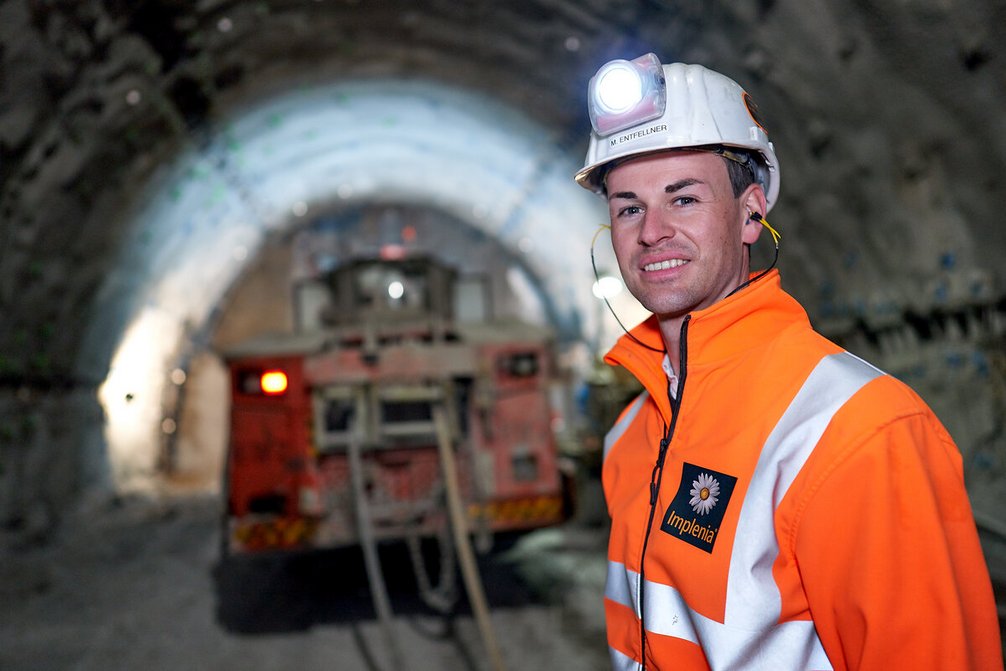
Il y a montagne et montagne. Et il n’y a pas que les alpinistes qui le savent, mais aussi les tunneliers. Certaines montagnes, comme le Semmering en Autriche, sont exigeantes d’un point de vue géologique. A l’avancement, la roche déformable se met en mouvement et soumet les structures du tunnel à une forte pression. Il s’agit de prendre des précautions en construisant le tunnel. «Plutôt que de fabriquer des coques de béton projeté fermées et rigides, nous les rendons élastiques en y incorporant des éléments de compression», explique Manuel Entfellner. «Nous absorbons ainsi la pression de la montagne et nous assurons la stabilité du tunnel malgré la pression du massif.
Le Salzbourgeois de 29 ans s’y connaît en la matière. Pour boucler ses études de géotechnique et de construction de tunnel, il s’est précisément intéressé dans son mémoire à l’utilisation de ces éléments de compression. «Une pression énorme pèse sur ces éléments. Il est capital, lors du choix du matériau, de comprendre les exigences précises en matière de propriétés de dilatation et de tension», explique-t-il. «Traditionnellement, le choix se porte sur l’acier.»
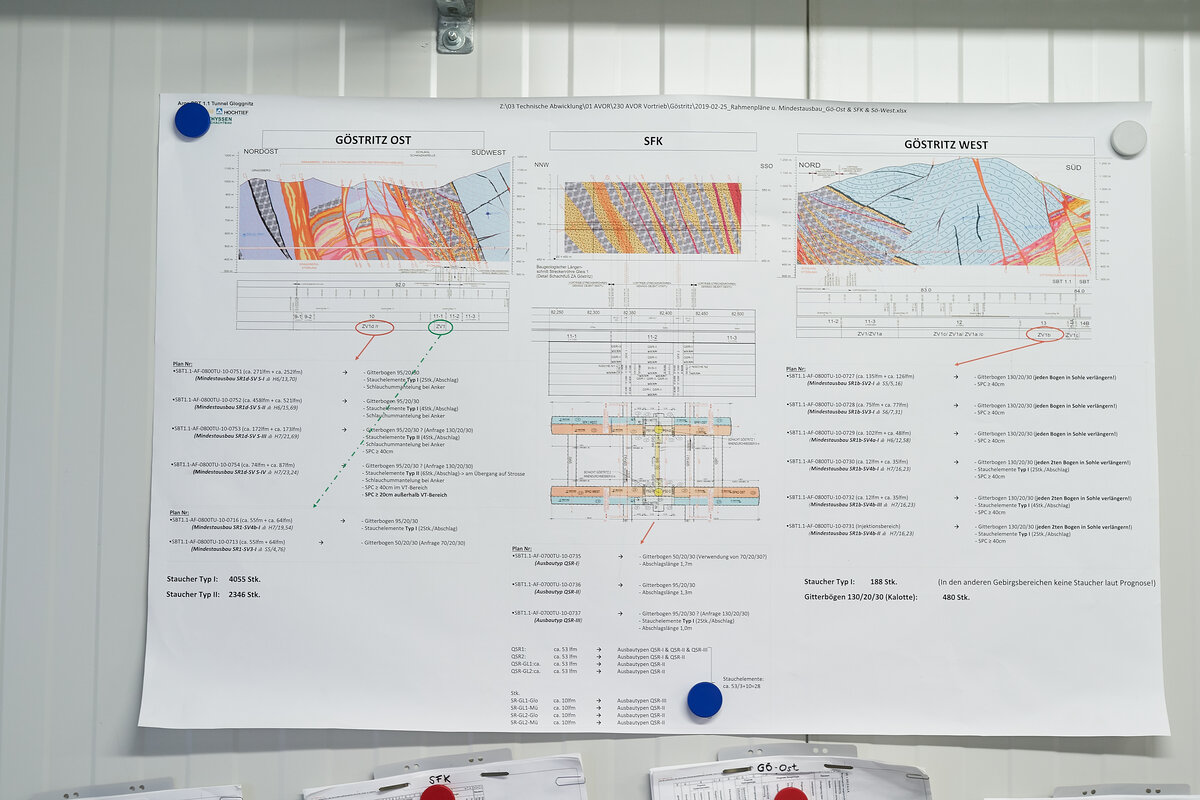
Lors de ses tournées quotidiennes sur le chantier du tunnel, Manuel a observé l’incorporation de nombreux éléments de compression. À chaque dynamitage, ce sont jusqu’à six éléments qui sont montés. Chacun pèse près de 80 kg et est positionné par deux hommes dans un espace très confiné à quatre ou cinq mètres de hauteur, souvent par-dessus la tête, ce qui nécessite beaucoup de force. «C’est un travail extrêmement difficile, complexe, pénible, une catastrophe d’un point de vue ergonomique et dans tous les cas un risque en matière de sécurité», explique le contremaître Markus Viertler.
«Il y a des choses dans le travail pour lesquelles on se dit: ça ne peut pas être ça la solution!»
Manuel Entfellner, chef de chantier
« Il y a des choses dans le travail pour lesquelles on se dit: ça ne peut pas être ça la solution!» dit Manuel. «La situation était la suivante : je m’y connaissais assez bien en éléments de compression et j’en voulais de meilleurs que ceux qui sont disponibles en ce moment sur le marché.»
L’ingénieur civil avait déjà une solution en tête. «Je savais grâce à mes études que le PSE/polystyrène – utilisé notamment en guise d’isolation périphérique sous les fondations – pouvait remplacer l’acier dans de nombreuses applications », explique-t-il. « C’est ce que j’ai voulu essayer.» Un petit laboratoire existe sur le chantier du Semmering. Il y a commandé des matériaux et s’est mis à tester de nouvelles solutions – le plus souvent durant son temps libre.
Les premières tentatives avec du polystyrène en vente dans le commerce ont échoué au niveau de la fermeté, qui devait être multipliée par 20. Cela fut possible grâce à une collaboration avec un fabricant d’isolants autrichien et de nombreux essais dans son laboratoire. L’étape suivante fut un vaste programme d’essais.
« Nous avons testé d’innombrables variantes d’éléments de compression et défini ce qui était le mieux pour l’utilisation dans le tunnel de base du Semmering», selon Manuel Entfellner. «Nous avons finalement pu construire un prototype et le présenter au client, les Chemins de fer fédéraux autrichiens (ÖBB). »
Avec ses 19 kg, le nouvel élément de compression affiche sur la balance tout juste un quart du poids de l’élément en acier conventionnel – tout en offrant une performance maximale. «Lors de la présentation, toutes les personnes présentes ont pu directement comparer les deux versions. Même les sceptiques ont été rapidement convaincus.»
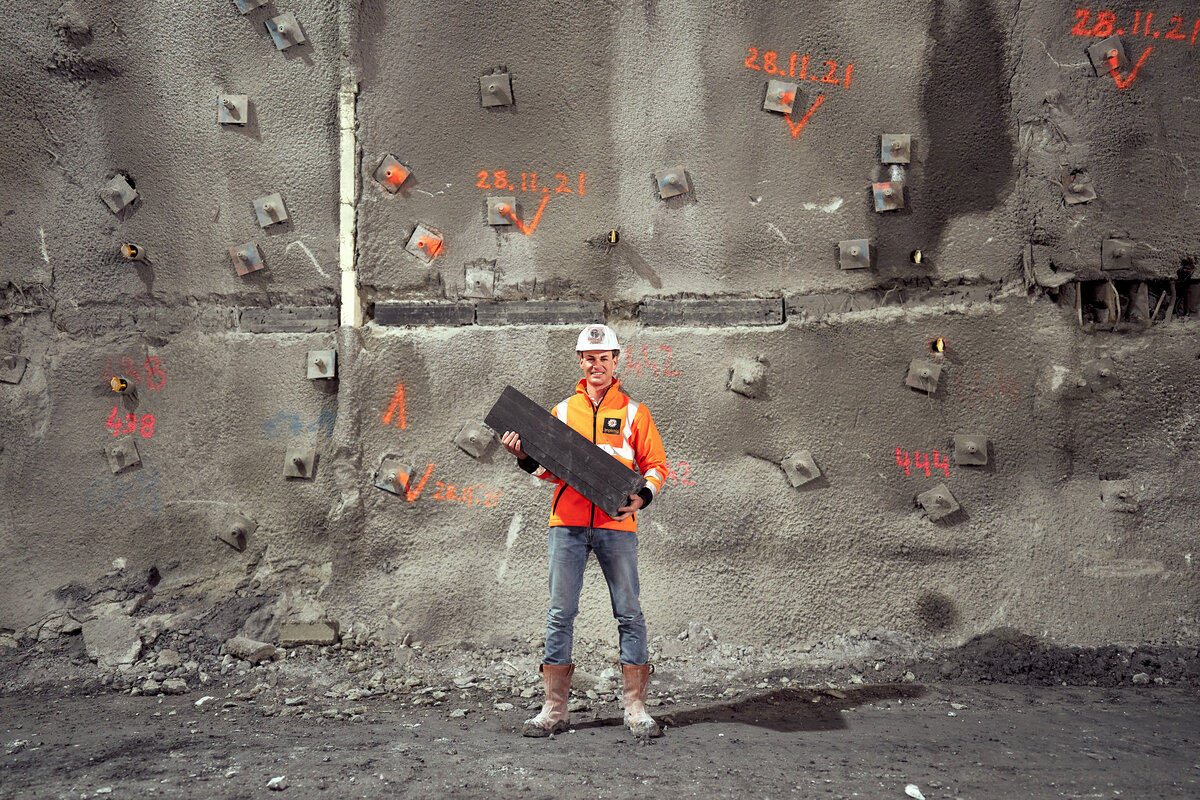
D’autres tests dans le tunnel ont également été convaincants. Sur un tronçon test de 10 m, le nouvel élément s’en est sorti avec brio. Mais plus encore, les éléments de compression conventionnels en acier se sont avérés insuffisants sur un tronçon techniquement exigeant. Les nouveaux éléments y ont été utilisés en concertation avec ÖBB – 650 d’entre eux ont été installés et sont depuis pleinement satisfaisants.
Pour qu’ils figurent définitivement sur la liste officielle de matériaux pour le projet, les éléments doivent, en parallèle au laboratoire, être soumis à des contraintes de sorte qu’une durée de vie de 150 ans puisse être garantie. «Nous utilisons les résultats des tests dans une prochaine étape pour établir des extrapolations sur 150 ans», selon Manuel Entfellner. Après quoi, le produit est prêt pour le marché.
«De nombreux collègues étaient sceptiques dans un premier temps», dit Manuel pour décrire la réaction de son milieu professionnel à son esprit novateur. «Heureusement deux personnes ont totalement soutenu cette idée dès le début et m’ont apporté leur aide: notre géotechnicien Helmut Wannenmacher et Rudolf Knopf, directeur d’Implenia Autriche.»
«En améliorant les procédés ou les matériaux, nous en profitons directement, car le travail devient plus facile pour nous.»
Helmut Wannemacher, géotechnicien
Helmut Wannenmacher, également expert en géotechnique, est en quelque sorte un habitué quand il s’agit d’innovation. «Nous voyons encore et toujours des solutions insatisfaisantes dans notre travail dans la construction de tunnel», explique le natif du Tyrol. «En parvenant à améliorer les procédés ou les matériaux, nous en profitons directement, car le travail devient plus facile pour nous. La plupart du temps, les nouvelles solutions sont également plus économiques. Je trouve cela motivant de pouvoir sans cesse expérimenter de nouvelles choses dans le cadre de mon travail.»
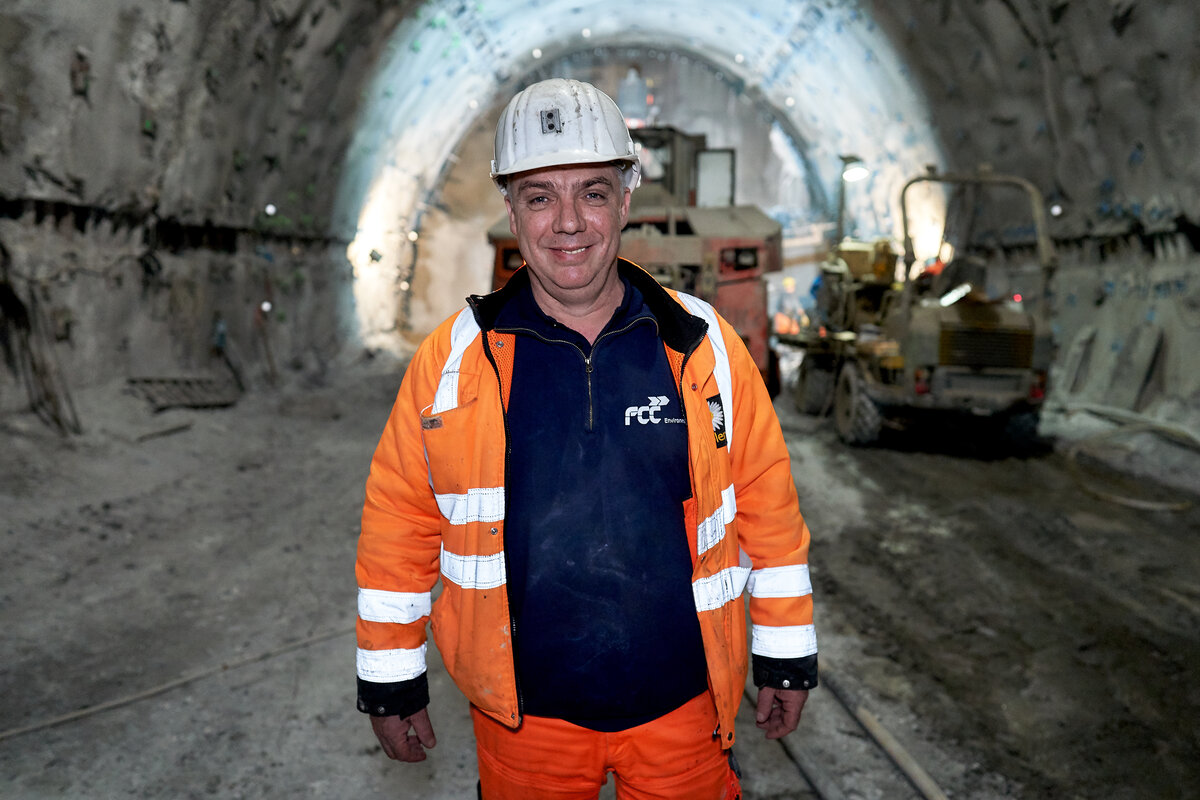
Rudolf Knopf aime son équipe engagée et soutient activement les initiatives visant à obtenir de meilleurs produits plus économiques. «Pour les éléments de compression, nous avions un marché protégé avec des prix exorbitants et une qualité insatisfaisante. La solution dans ce domaine est vraiment la bienvenue chez nous. Quand des personnes arrivent avec de bonnes idées, je les soutiens. «Impossible!» ça n’existe pas chez nous.»
Rudolf Knopf a également encouragé Manuel à présenter sa proposition sur Kickbox, le programme d’innovation interne à Implenia. Depuis, l’équipe de l’Innovation Hub d’Implenia le soutient dans le dépôt du brevet du produit en préparant son déploiement sur le marché. La solution suscite également de l’intérêt chez d’autres entreprises.
«Avec la tendance à placer de plus en plus sous terre les routes et les lignes ferroviaires, la construction de tunnel continue à gagner en importance en tant que discipline.»
Rudolf Knopf, directeur d’Implenia Autriche
Manuel Entfellner, tunnelier et intrapreneur de 29 ans, verra sans doute prochainement comment son innovation sera utilisée non seulement pour son propre projet, mais enrichira aussi la construction de tunnel bien au-delà des frontières autrichiennes. Et c’est très bien ainsi. «Avec la tendance à placer de plus en plus sous terre les routes et les lignes ferroviaires, la construction de tunnel continue à gagner en importance en tant que discipline», Rudolf Knopf en est convaincu. «Les esprits innovants comme Manuel Entfellner font en sorte qu’Implenia ne fournisse pas seulement un travail solide, mais contribue également de façon déterminante à la manière dont les constructions seront faites demain.»
The project: Tunnel de base de Semmering, Los 1.1 –Gloggnitz tunnel
Le tunnel de base du Semmering (SBT) représente actuellement l’un des plus grands projets d’infrastructure au cœur de l’Europe. D’une longueur totale de 27,3 kilomètres, le tunnel constitué de deux tubes à voie unique sera percé entre Gloggnitz et Mürzzuschlag et reliera la Basse-Autriche et la Styrie. Il fait partie intégrante de la nouvelle ligne ferroviaire sud-autrichienne, qui constitue l’axe central de la liaison transeuropéenne entre les mers Baltique et Adriatique. Implenia, en tant que membre du consortium qu’il constitue avec HOCHTIEF et Thyssen a été mandaté par la Société fédérale des Chemins de Fer autrichiens (ÖBB) pour la construction du lot initial de l’ouvrage 1.1 d’une longueur de 7.4 km environ.
Client: Chemin de fer fédéral autrichien ÖBB Infrastruktur AG
Valeur de nos services: EUR 457 mio
Début de construction: Janvier 2015
Mandat Implenia: Mandataire, expertise technique, participation 40 %