Complex façade, very little space: Lean Construction!
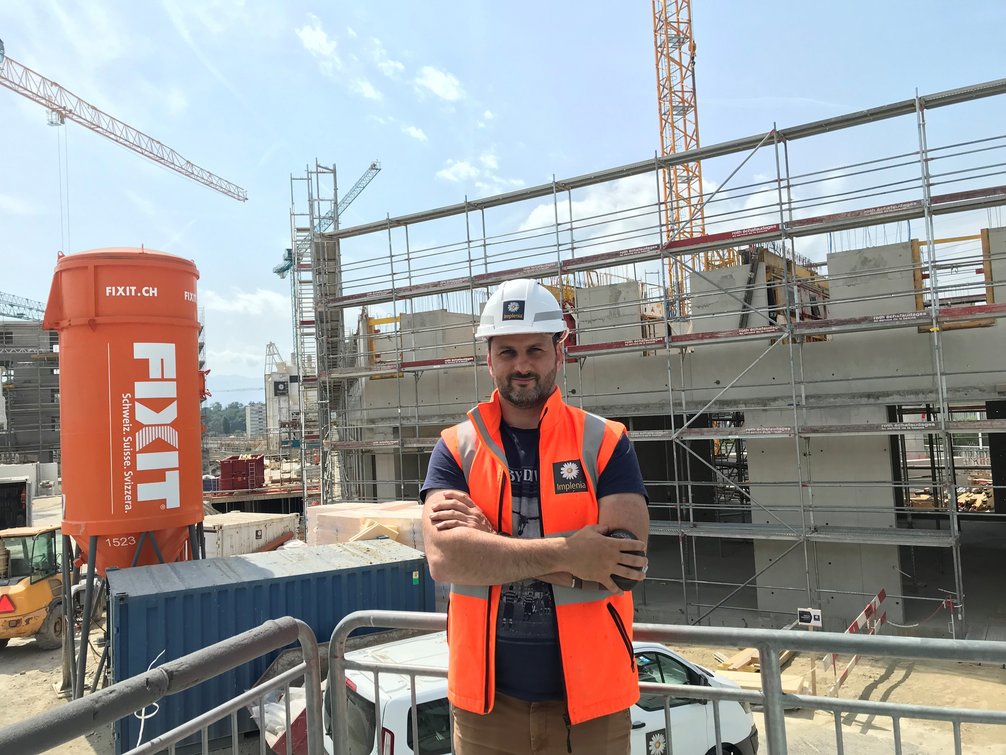
How did Lean Construction influence the schedule in this demanding project?
Lean Construction offers a clear, universal view of the construction managements requirements for the companies involved in the construction, enabling planning, organisation and optimisation. Specifically, the optimised planning allowed us to finish the project on time, despite starting with a delay of five months. And we also succeeded in sticking to the execution deadlines, despite unknowns and having to make numerous changes on site.
“The optimised planning allowed us to finish the project on time, despite starting with a delay of five months.”
Sébastien Depecker, site manager responsible for facade and envelope
What were the most important things you learned?
Organisation and communication are the key to success. I believed in the concept and its effectiveness from day one. But even with Lean Construction, the construction site does not manage itself. It takes dynamism and energy from the people involved to get the results.
Do you ever catch yourself not sticking to the defined processes?
When unforeseen events occur, I keep an eye on both the lean guidance and the targets that must be met. That allows me to make better decisions, because I can see the potential effects on each sub-contractor involved and can even discuss the material and content of the steering room with them and find the best solution for everyone. Only at the end of the project we lack involvement, when the order volume is smaller and we give instructions in the conventional way. Some companies are actually less efficient at that point.
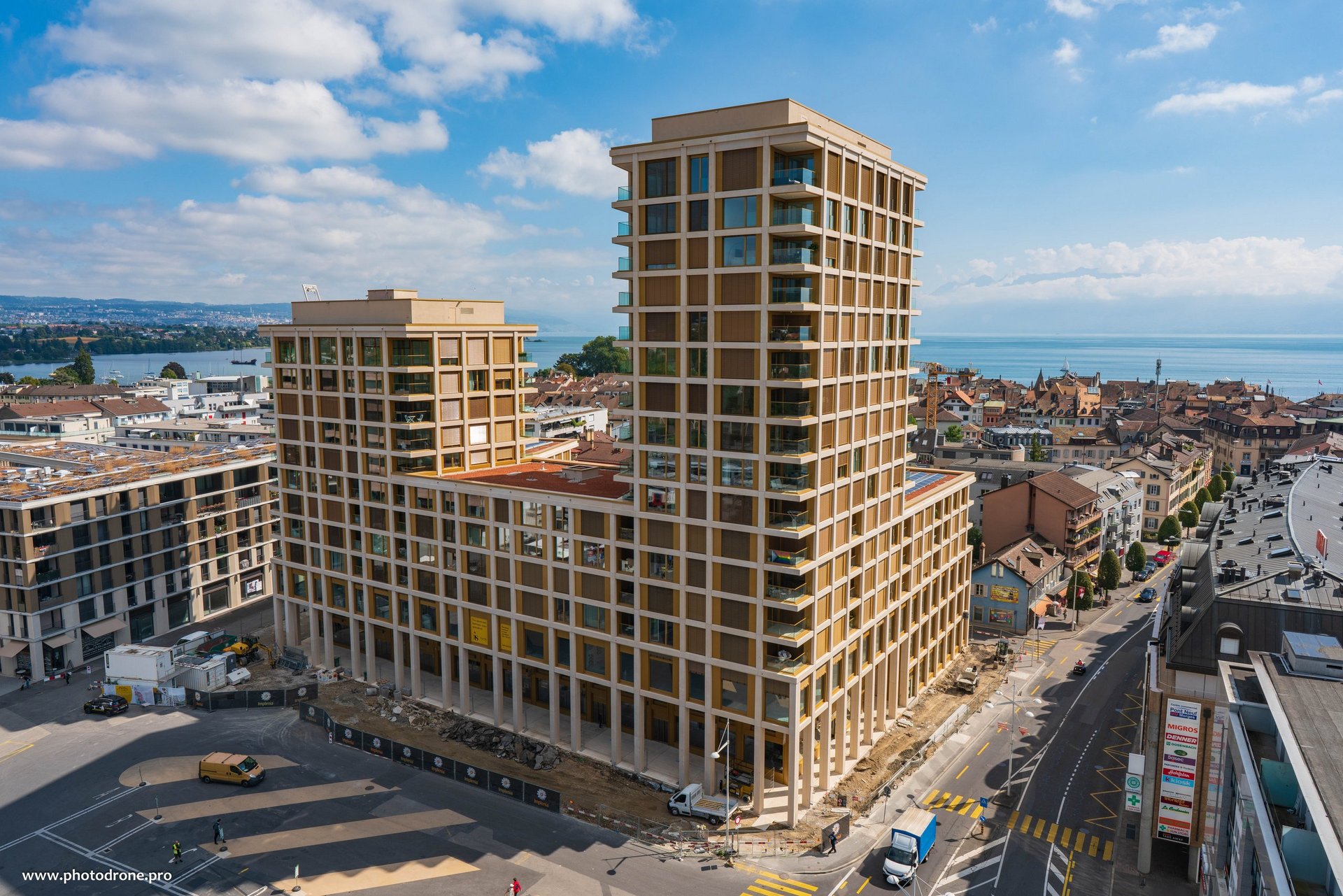
How is the collaboration with the team when Lean is introduced?
Lean Construction allows us to see the needs of every party involved and to spot potential conflicts, such as in execution or deliveries. For the project to be a success, it is important that everyone works at the same speed and understands that the project management has defined certain priorities that have to be adhered to .
Is there resistance and how do you overcome it?
Yes. Resistance comes not only from subcontractors, but sometimes from within the company, too. It helps to be able to show people how Lean allows us to spot problems early and solve them more efficiently. And anyway, Lean is not up for discussion. The method is gradually being introduced in all projects, making it the ‘new normal’ for organising a construction site.
Applied Lean methods
- Detail analysis of the façade processes
- 3-week planning and weekly assessment of PPC percentage plan completed (Last Planner System)
- Dynamic construction site setup plan to manage inventory
- Creation of an additional daily huddle (15mins) for steering the critical path for the 163 loggias
Has the Lean way of thinking influenced your private life? If so, how?
I am naturally a very structured person. For me, Lean is an opportunity to keep an eye on all my tasks, targets and actions, thus freeing myself from that mental load. I admit that I did try to introduce lean planning for a month at home to manage the family’s schedule, but I can’t fine my wife for being late.
“Lean = Winner: Lean Construction gives us a clear vision for a shared goal.”
Sébastien Depecker
If you had one sentence with which to appeal for Lean, what would it be?
Lean = Winner: Lean Construction gives us a clear vision for a shared goal and allows us to plan, organise and optimise. Together, for a team result.
The Îlot Sud project in Morges
Implenia was constructing the “Îlot Sud” project, a modern property with mixed use close to Morges Sud station. Its role as sole contractor comprises construction of 162 rented homes, more than 5,000 square meters of retail and leisure space, a 277-space underground car park, and a bike station with 250 spaces. Implenia developed the project in an architecture competition together with Fehlmann Architectes/Magizan Architecture Urbanisme AG. The new complex, which Implenia is creating for the real estate fund UBS (CH) Property Fund – Swiss Mixed “Sima”, is in line with the principles of sustainable construction with regard to resource consumption, harmful emissions and mobility. Construction work on the CHF 100 million project began with demolition of the existing properties in October 2017. The first tenants moved into their homes in this up-and-coming area of Morges in 2021.
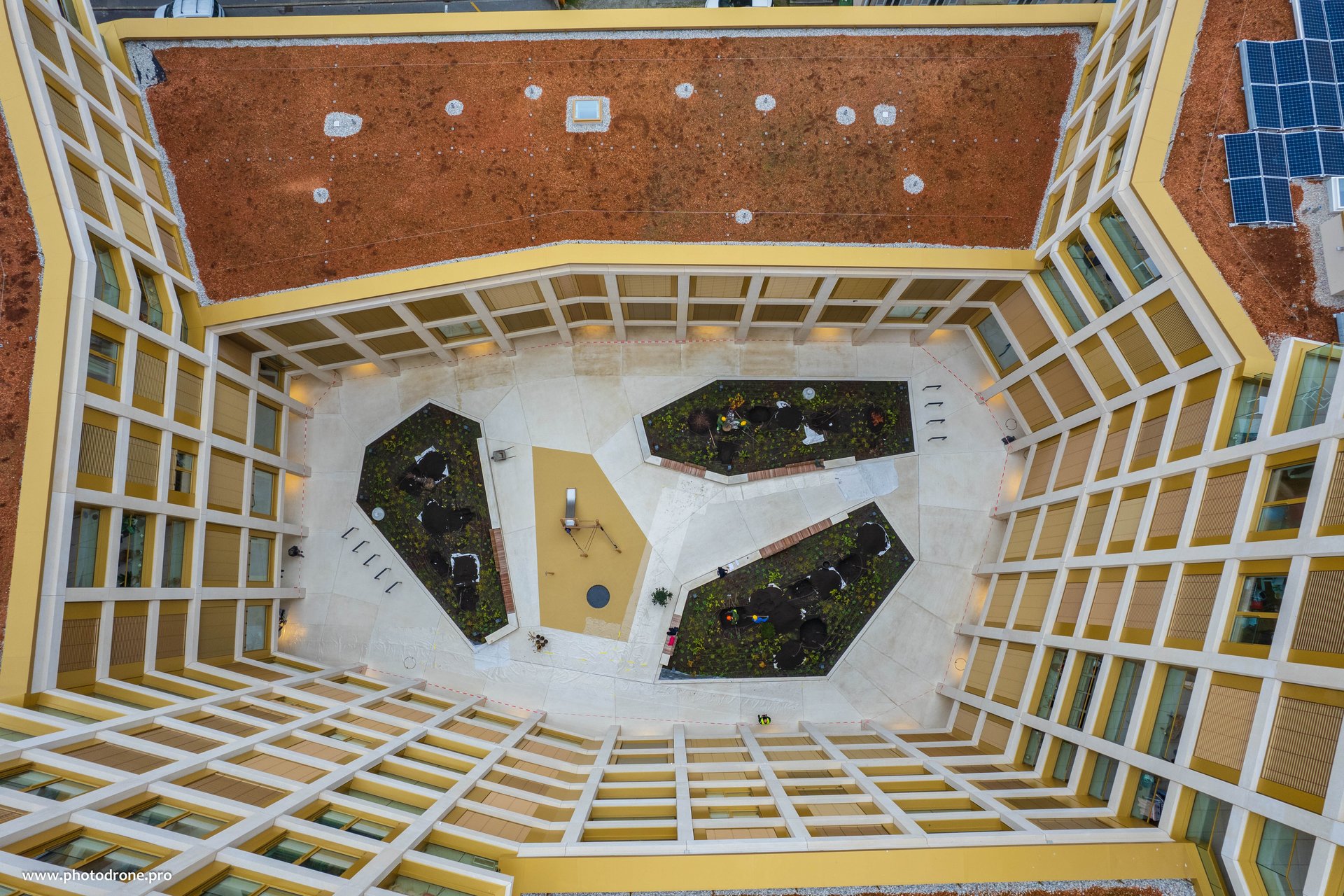