"We don't have a 90 degree angle here".
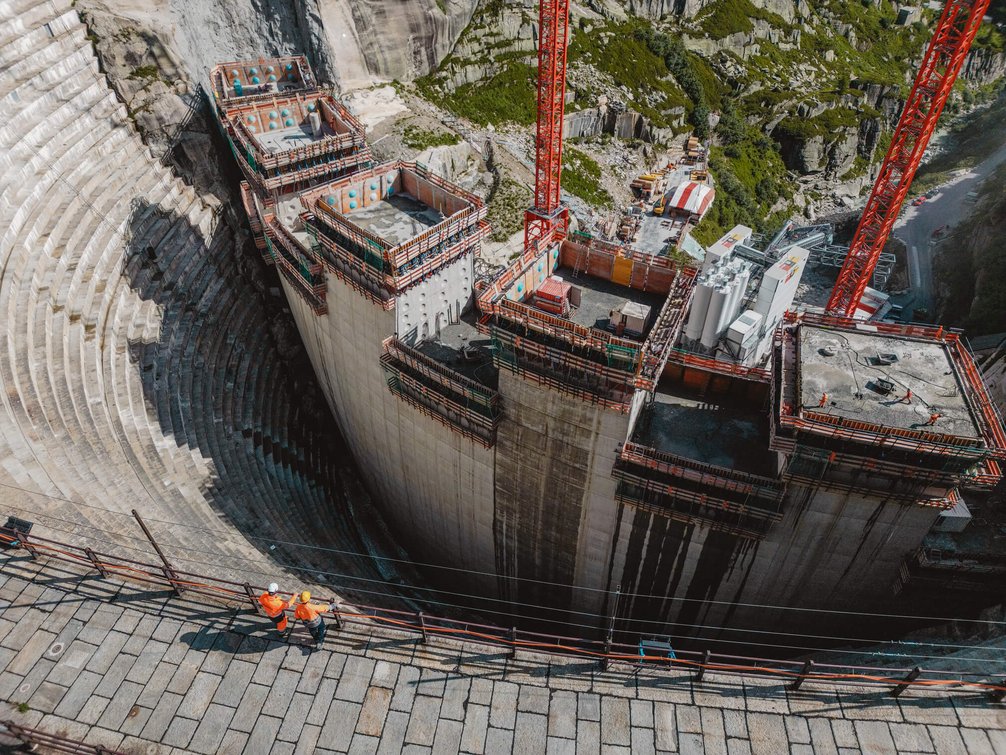
The view of the high mountain landscape is breathtaking: at 1,900 meters above sea level, the road winds in serpentines up to the Grimsel Pass, which connects the Bernese Oberland with the Upper Valais. The top of the pass is 2,163 meters above sea level and on the European watershed between the Mediterranean and the North Sea.
"When the weather is nice, it's perfect here," laughs construction foreman Daniel Seliner. He is already spending his third year on this construction site of the century and has experienced every kind of weather. On this hot late summer day, the water of the lake glistens, rocks and structure present themselves in the brightest light. But things can be different. "In 2021, when we started building, it rained a lot. That was difficult: if it's wet for weeks, the motivation also goes down."
Building at a "pilgrim's pace"
Around 100 people work in the Grimsel consortium team from the beginning of April to the end of October in several shifts, seven days a week. The construction site in the high mountains sinks under a thick blanket of snow in winter and is therefore only accessible for around six months of the year - time that needs to be put to good use. Formwork starts at 6 a.m. and concrete is poured from 4 p.m. onwards. The goal is to concrete a three-meter-high block every day, thus raising the dam in a "pilgrim's step" process.
"We first build the so-called forerunner blocks nine to twelve meters ahead and then pull the follower blocks after them - this looks as if battlements are growing upwards. This procedure saves time: we form the forerunner blocks once on all sides, and the followers only get parament formwork on the water and air sides. This way, we can work on different levels and don't get in each other's way," says Daniel, explaining the process.
Once one of the blocks has been concreted and the concrete is hard, the team releases the formwork and uses the crane to position it three meters further up. Precision is required during the fitting process. "We don't have a 90-degree angle here at the double-curved dam; everything is rounded. That's why every block is measured with the theodolite," says Daniel Seliner.
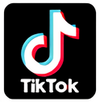
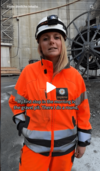
LET OUR TEAM SHOW YOU AROUND THE CONSTRUCTION SITE!
Construction of the Spitallamm replacement dam
Kraftwerke Oberhasli AG will replace the existing dam with a new one from 2019 to 2025. The old wall is in need of renovation, but it will be retained and flooded at a later date. With the replacement of the Spitallamm wall, the KWO ensures that the water from Lake Grimsel can be used for electricity production without restriction in the long term.
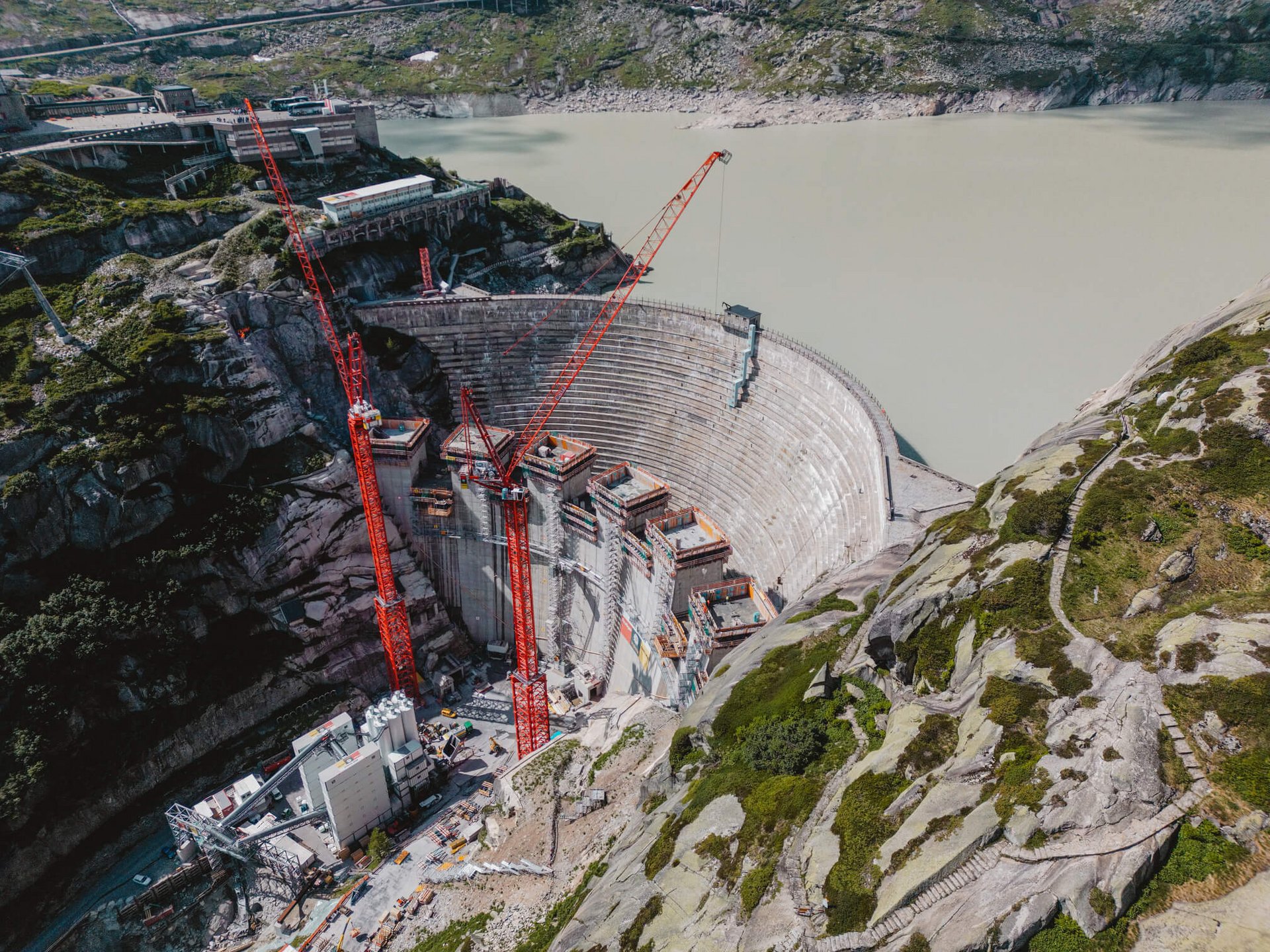
Concrete production at the foot of the wall
The concrete used, with a low cement content and fly ash, is produced in the mixing plant directly at the foot of the dam. Since 2022, construction foreman Julia Geist has been supervising concrete production as well as the work in the company's own gravel plant at 1,650 meters above sea level, about three kilometers down the road.
"In contrast to otherwise standard concrete, here the client specifies the composition of the concrete precisely," Julia explains. "That really only exists for dam walls. We use aggregates up to 125 mm in diameter. This is a very exceptional concrete!"
The material for concrete production comes from the immediate surroundings, as Julia points out, "We extract the rock and aggregates ourselves. At first, we recycled the rock excavated from the dam for this purpose. In the meantime, we use old-legal dumps from the 1980s that were made for tunnel excavations for the Grimsel system."
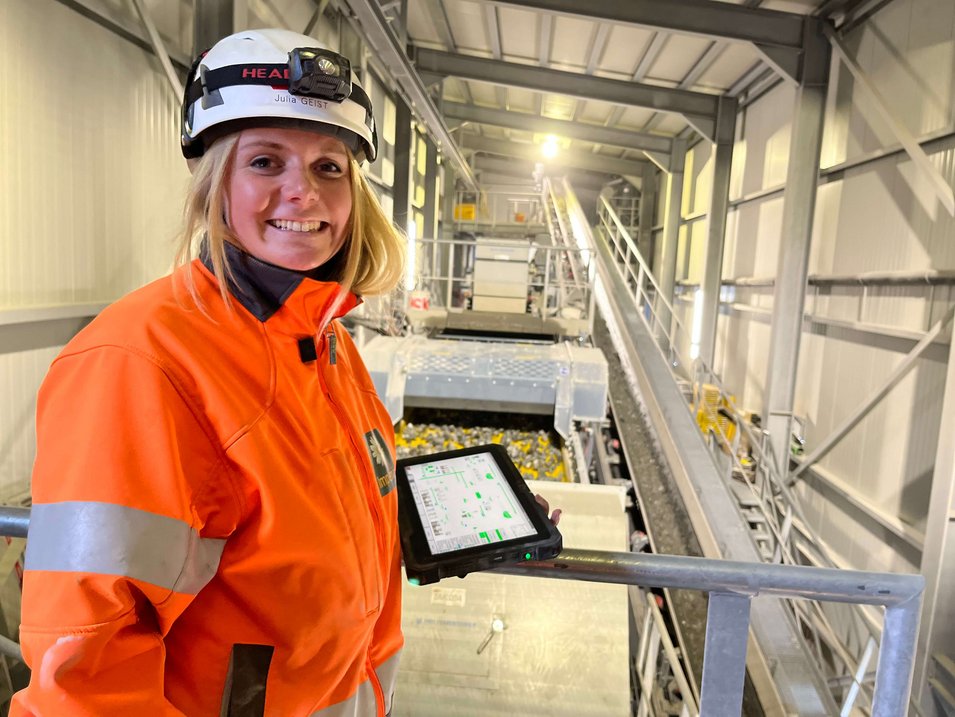
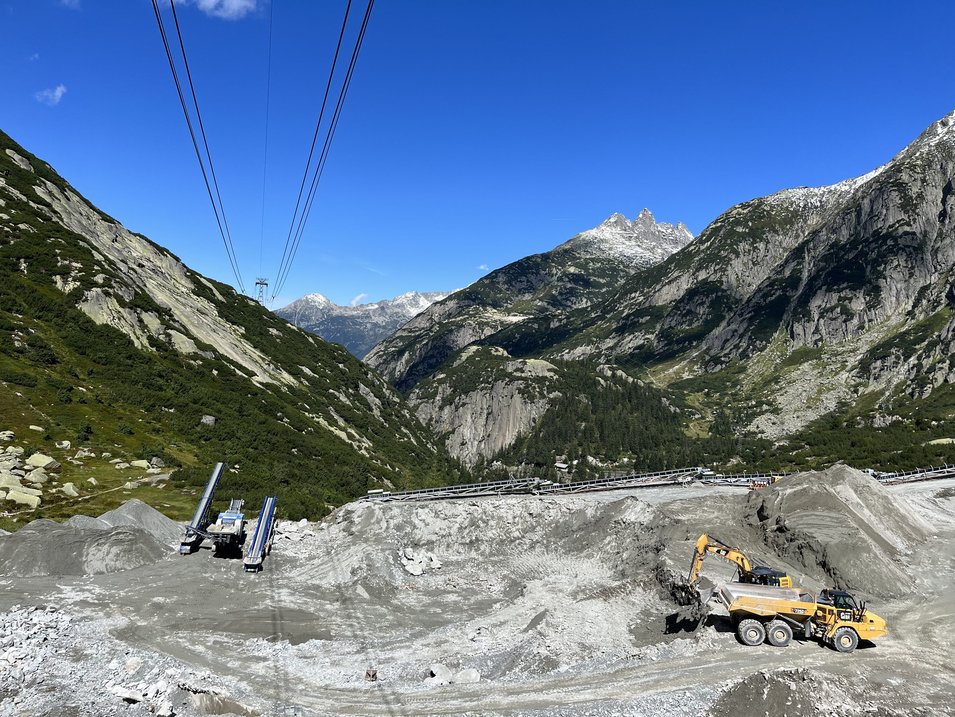
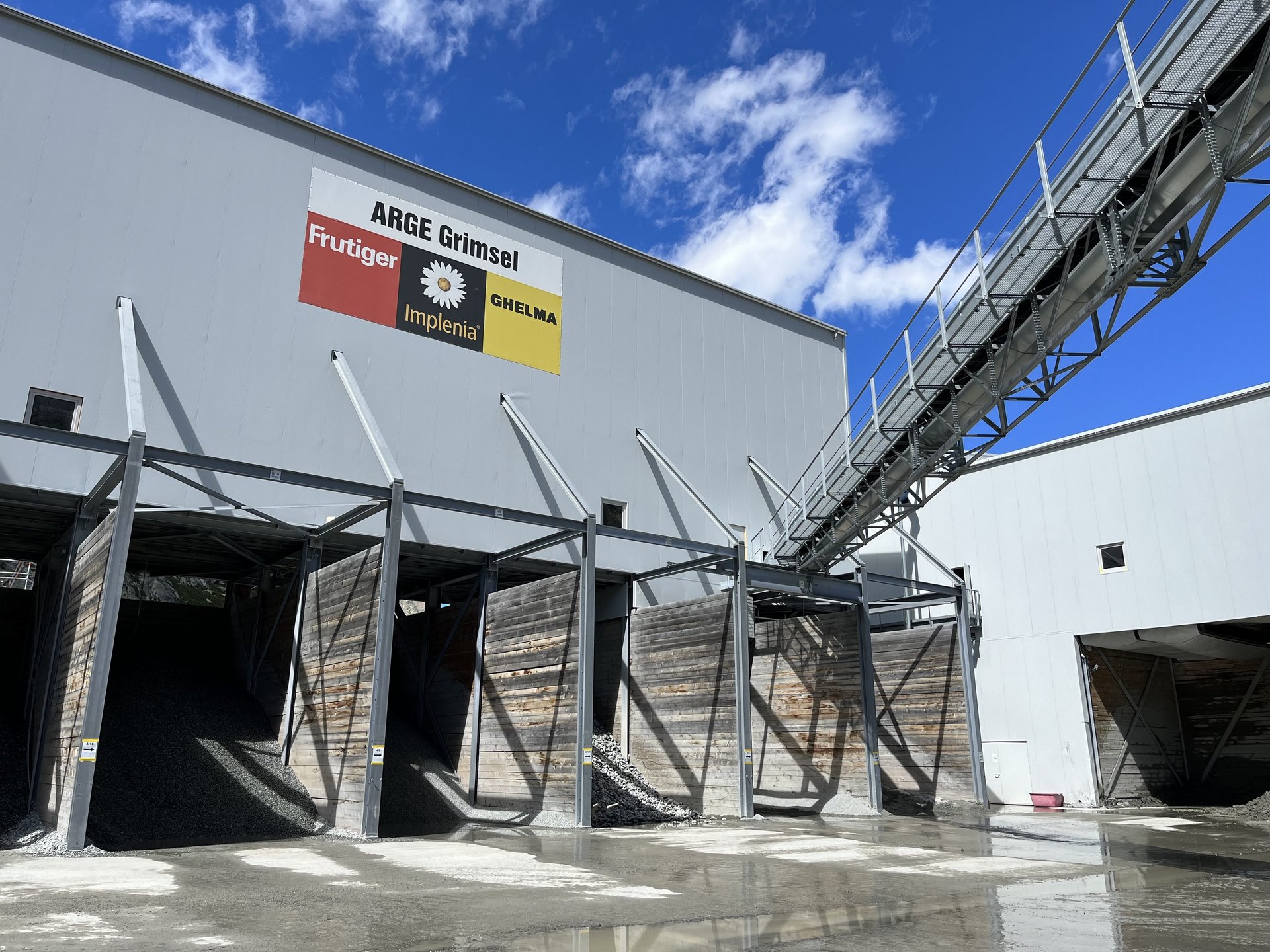
Short distances are good for the environment
Before the rock can be used for concrete production, a number of work steps are necessary that must be coordinated in terms of quality and timing. "We first remove plastic and wood from the landfill, among other things. Then the pre-crushed raw material is further crushed, washed and screened in the gravel plant, preparing it for the various rock components for concrete. Afterwards, we drive it about 3 km by truck up to the concrete plant and fill it into the appropriate silos there."
Short distances save time and are good for the environment. And where there is no other way, the team relies on transport that is as environmentally friendly as possible, as Julia explains: "Cement and fly ash are the only things we have to bring up from the valley. Some of this material is brought up by electric trucks."
The concrete itself is mixed right at the foot of the dam - strictly according to specifications to meet the high quality requirements. "We operate our own construction site laboratory, and that's where the material is continuously tested and the process documented," Julia emphasizes.
40 km of water pipes in the concrete
To ensure that the new dam wall does not develop any cracks, however, it is not only the right concrete mix and proper placement that are relevant; the concrete must also cure evenly. For this purpose, it is already cooled during installation - with water that is fed through a total of around 40 km of water pipes through the new dam.
The cold water comes from the reservoir and is returned to the Grimsel system after use, as Daniel Seliner explains: "The water in the lake contains a lot of sediment. After we use it, we clean it - and then feed it back cleaner than we took it out. We check and document the water quality every day. We feel the need to take good care of the environment."
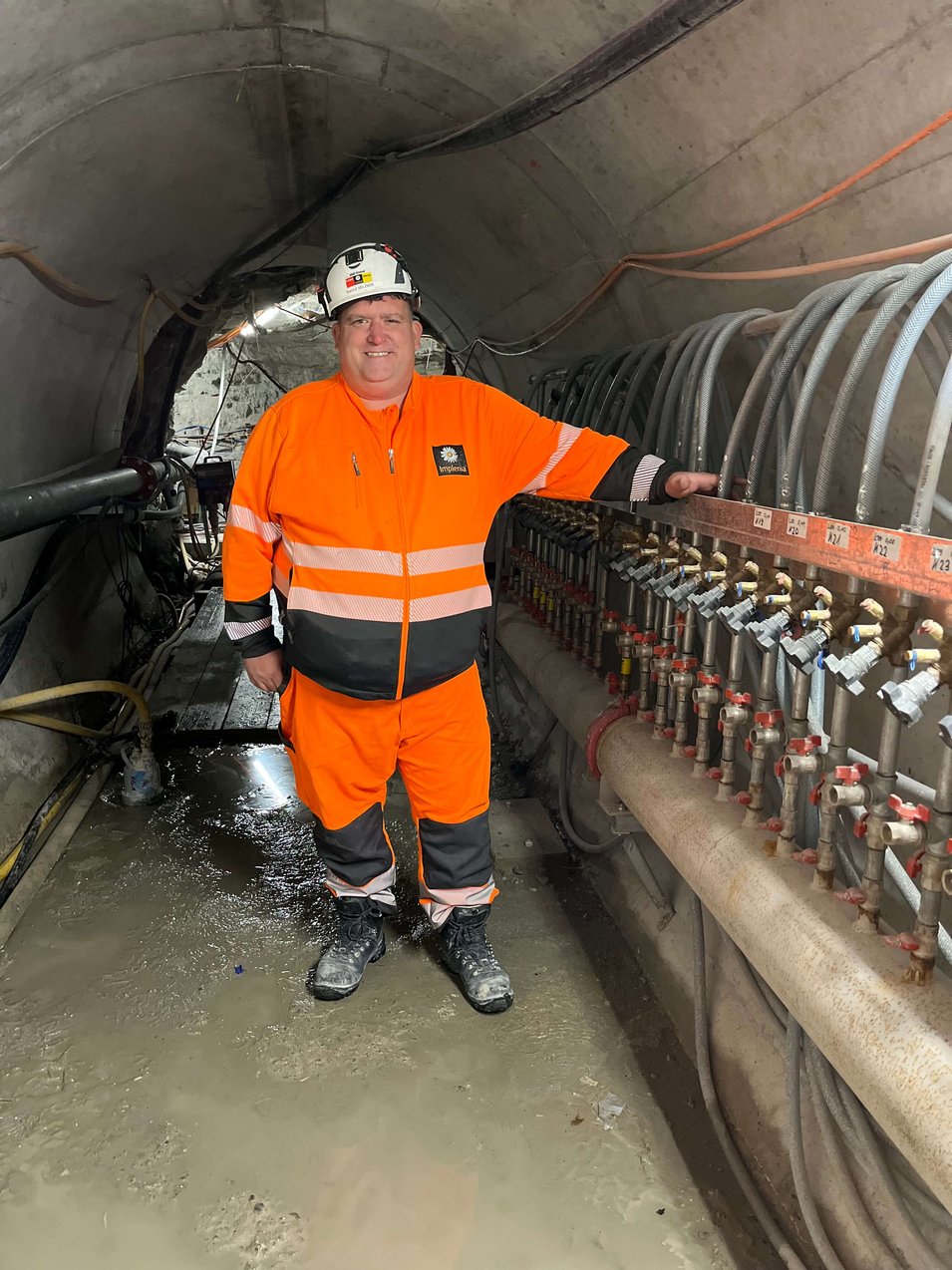
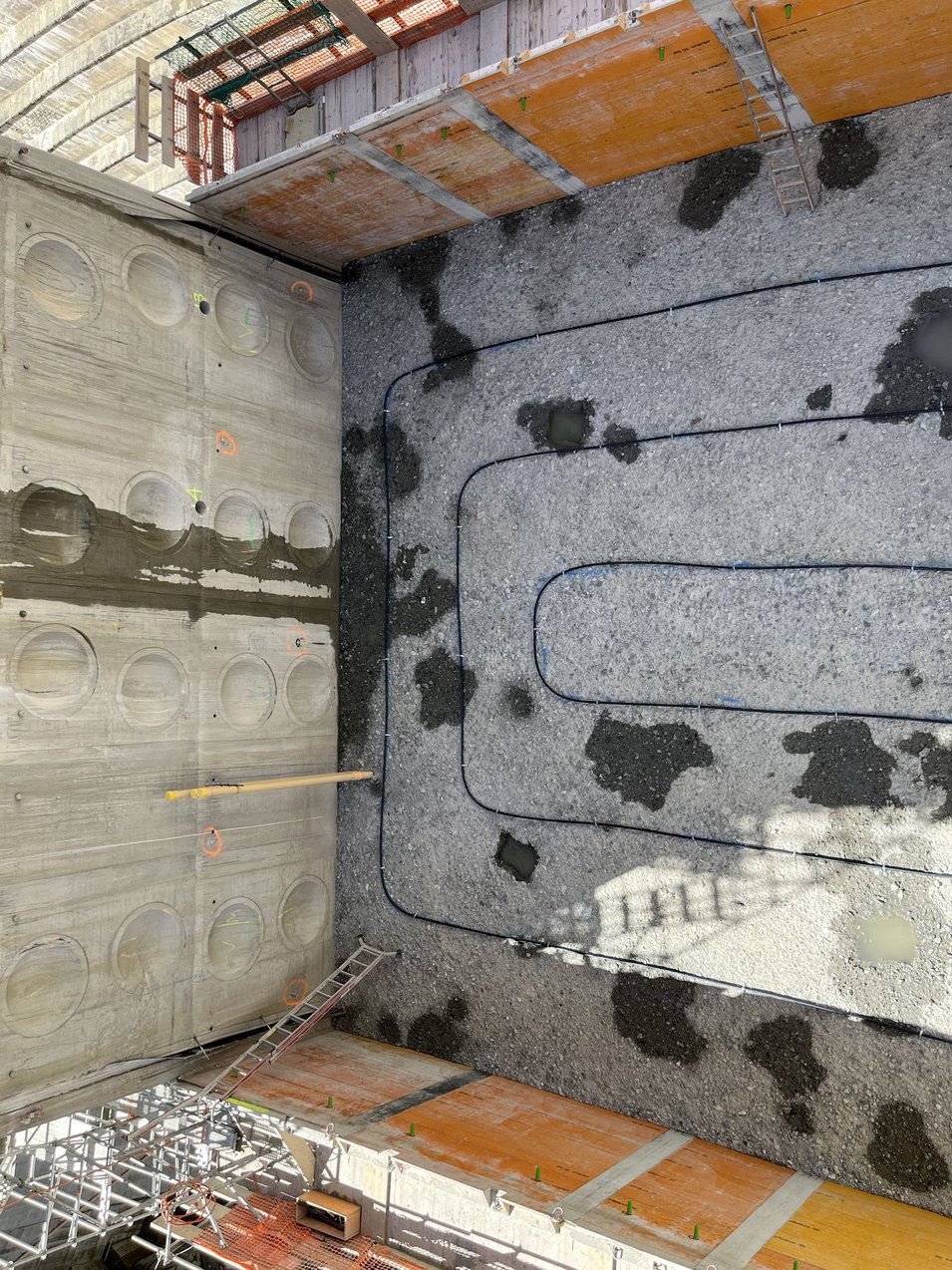
Against the clock in 3-meter steps
Once the planned block has been formed, the cooling and injection lines laid and joint tapes, recesses and formwork for the inspection walkways etc. installed, the work begins: the concrete is conveyed by a large forklift truck to the concrete bucket on the crane and lifted up onto the new wall being built, where the team is already waiting for it with the spreading excavator and the vibro-excavator. By 3 a.m. every day, around 500 m3 of concrete are placed in a prepared block. In this way, the wall grows a little further in height every day.
Towards the end of the intensive construction season, Daniel Seliner looks at the day's work with satisfaction: "This is the third concreting season here on the site, and it's really going extremely well. The teams got together quickly at the beginning of the season, and people are enjoying working on such a project of the century. We are fully motivated and even ahead of schedule. With that, I'm confident that we'll be able to hand over the dam to the client in the fall of 2025."
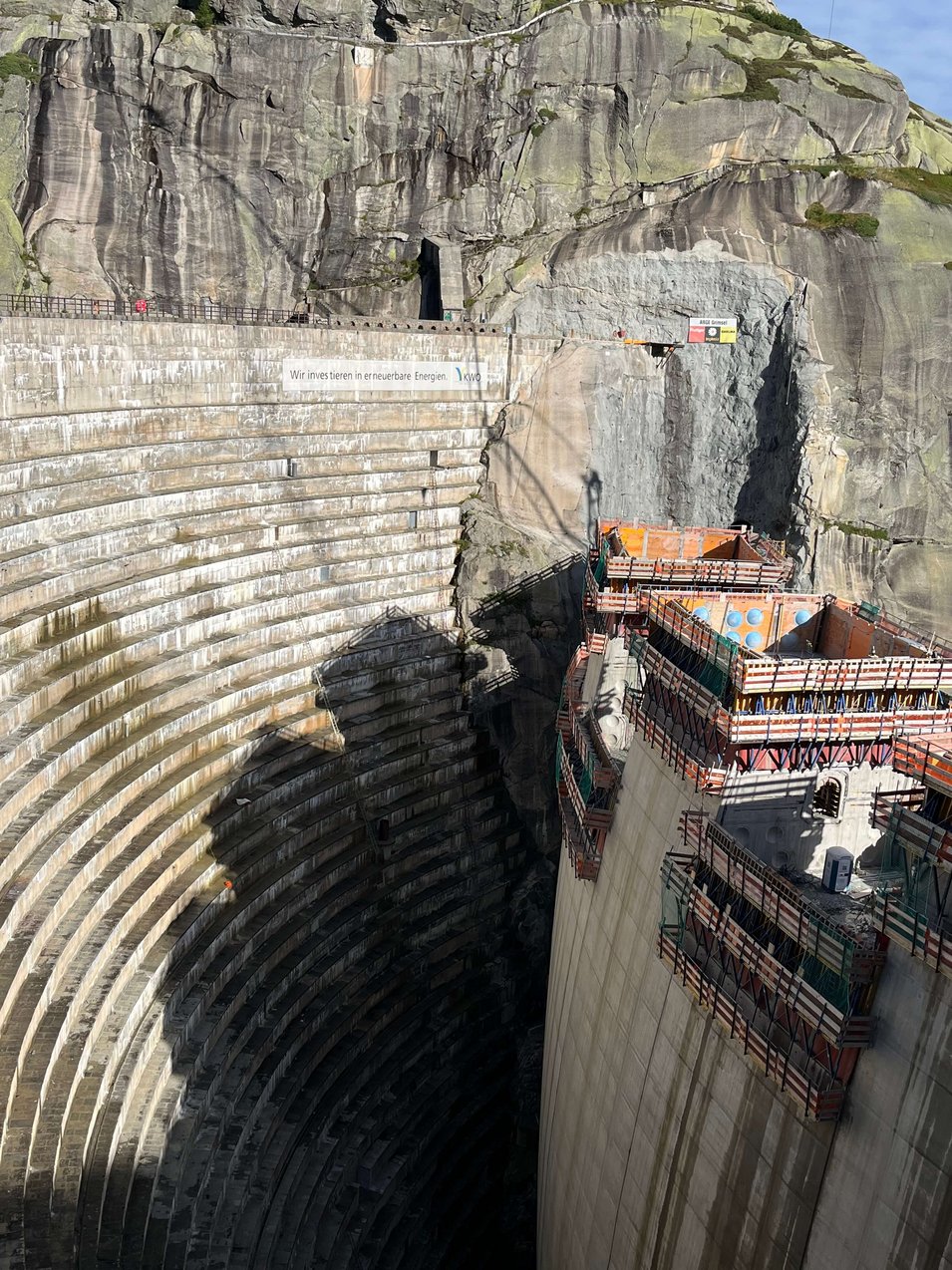
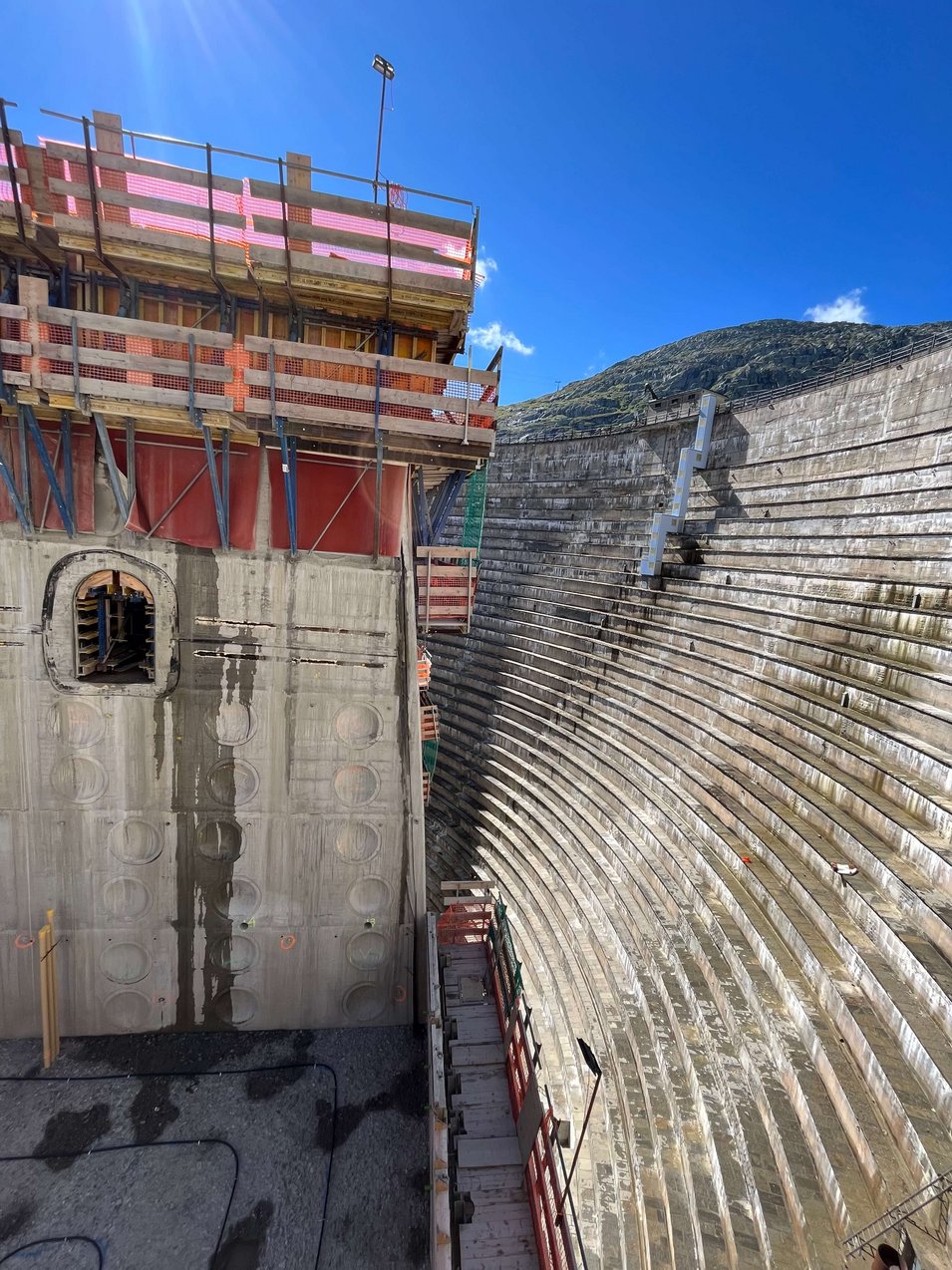
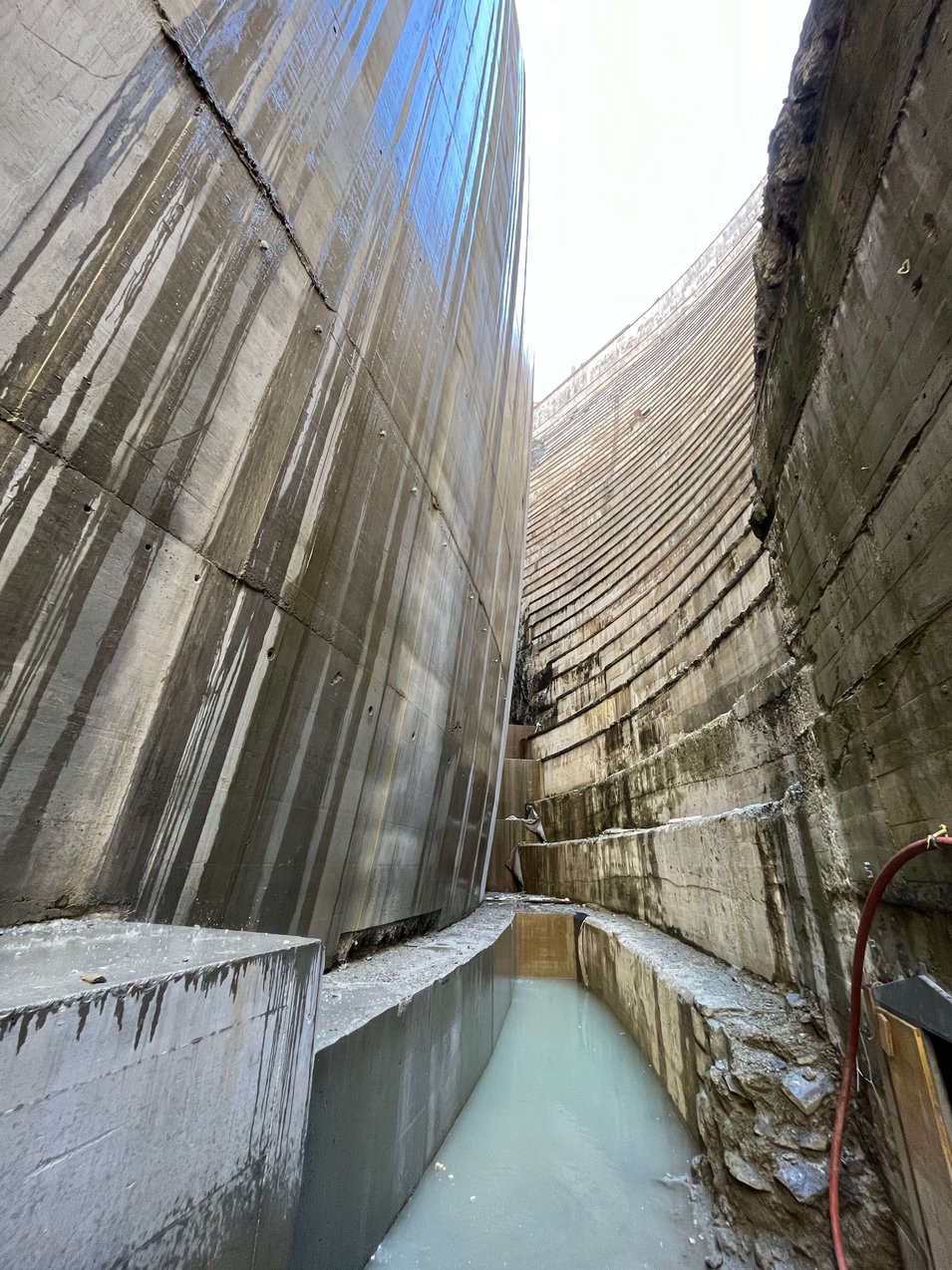
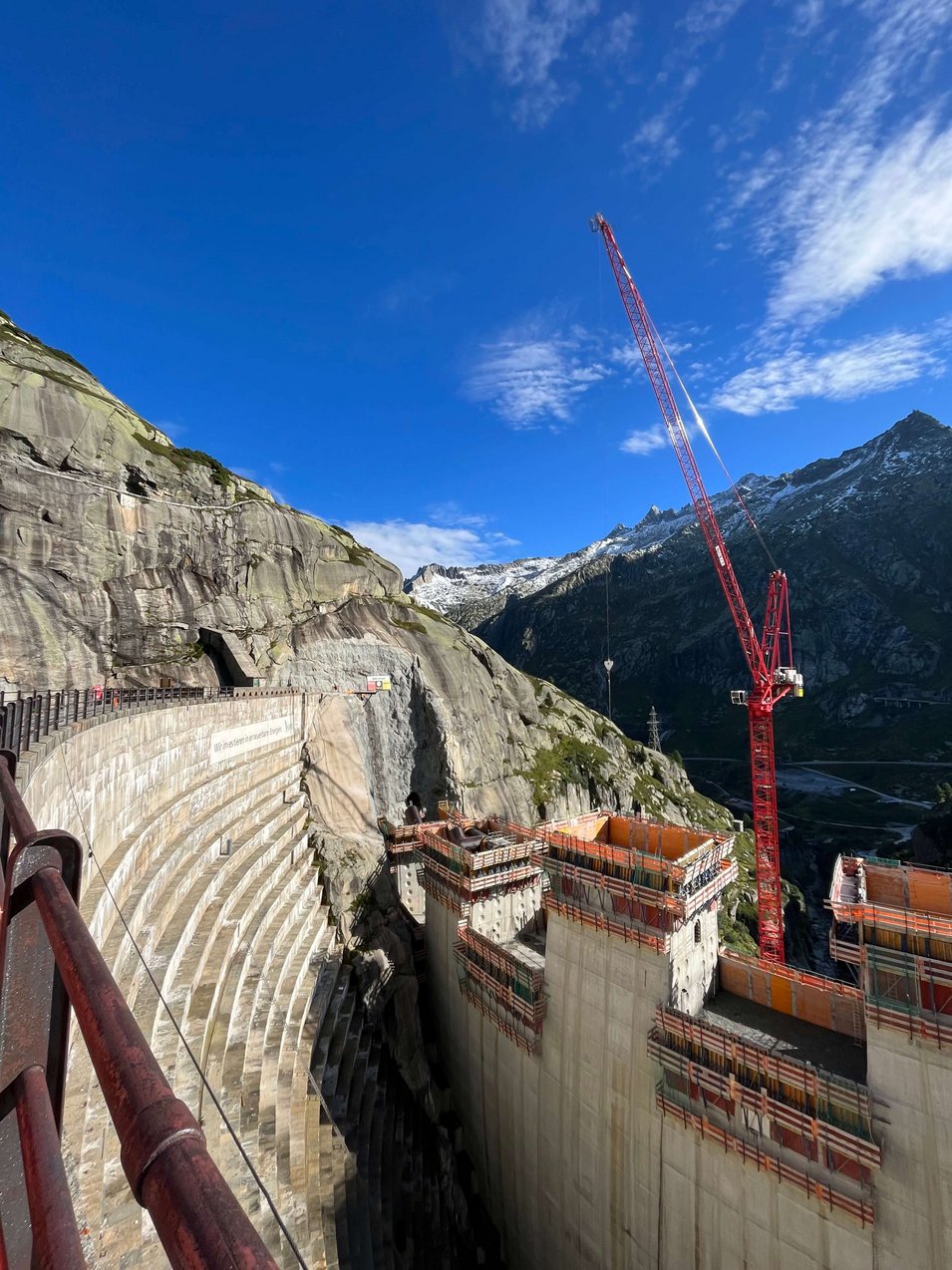
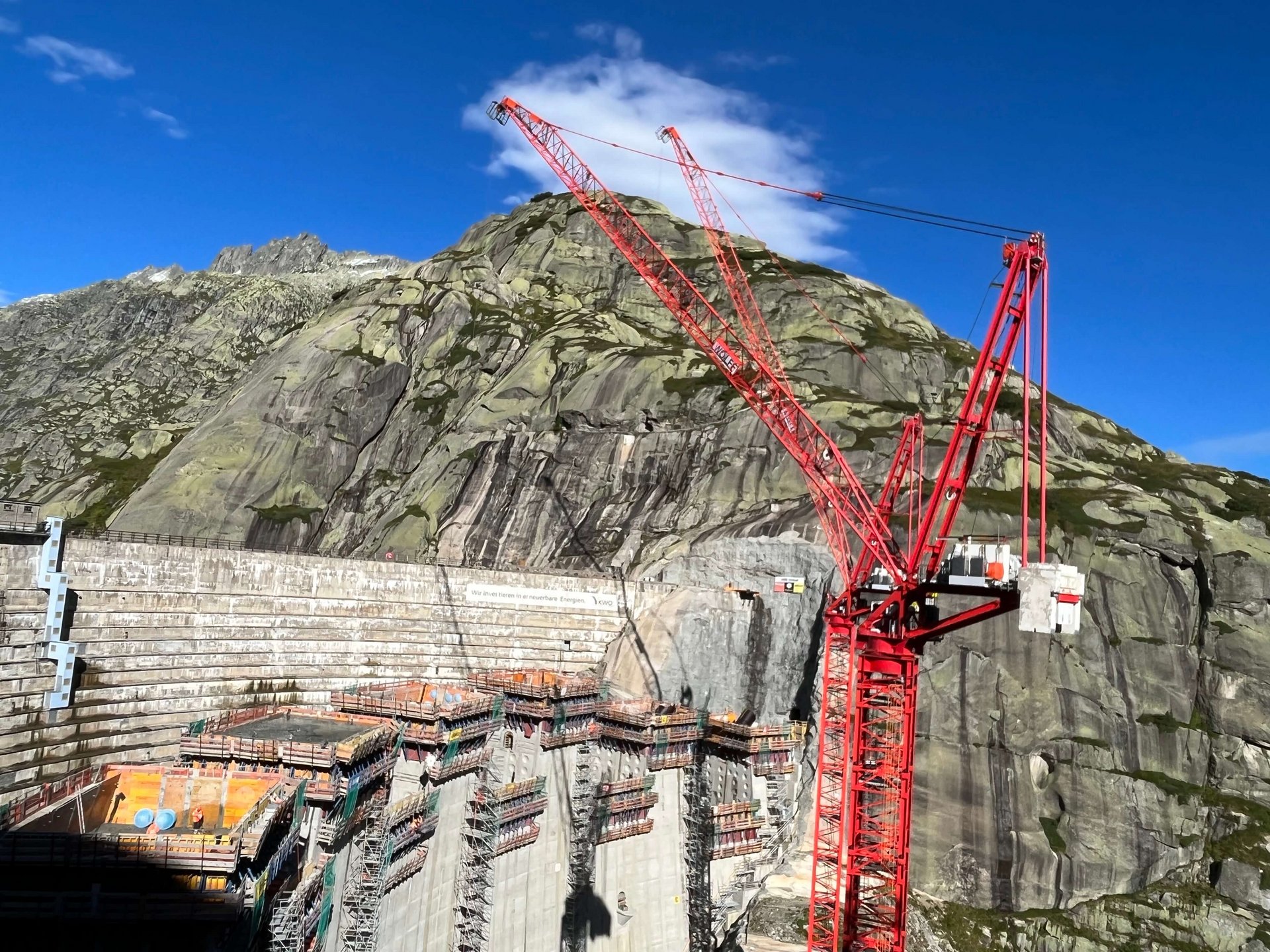
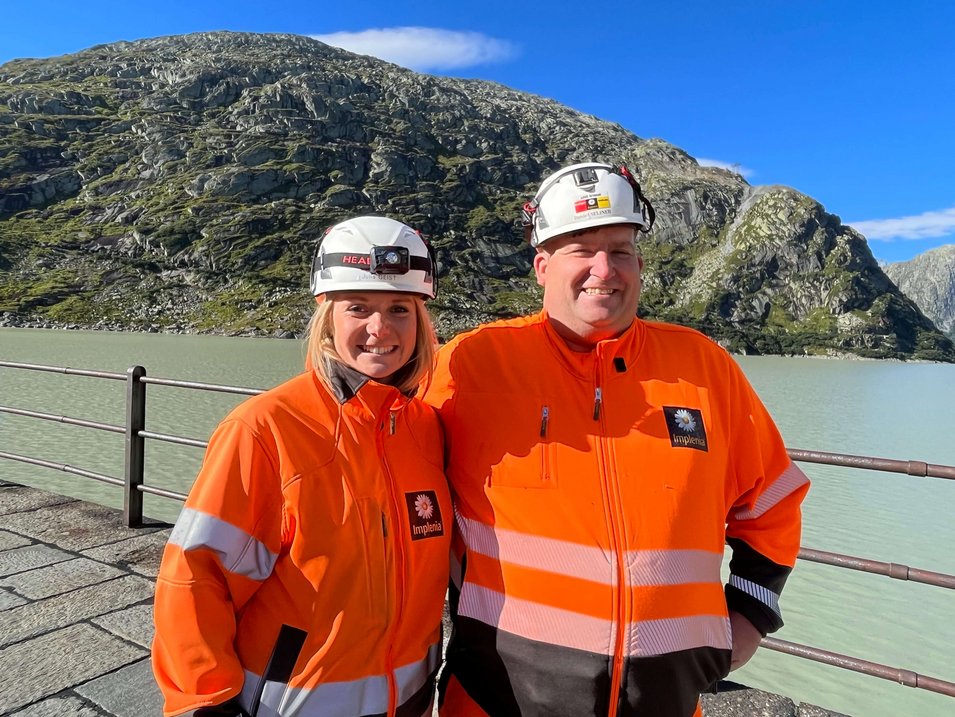
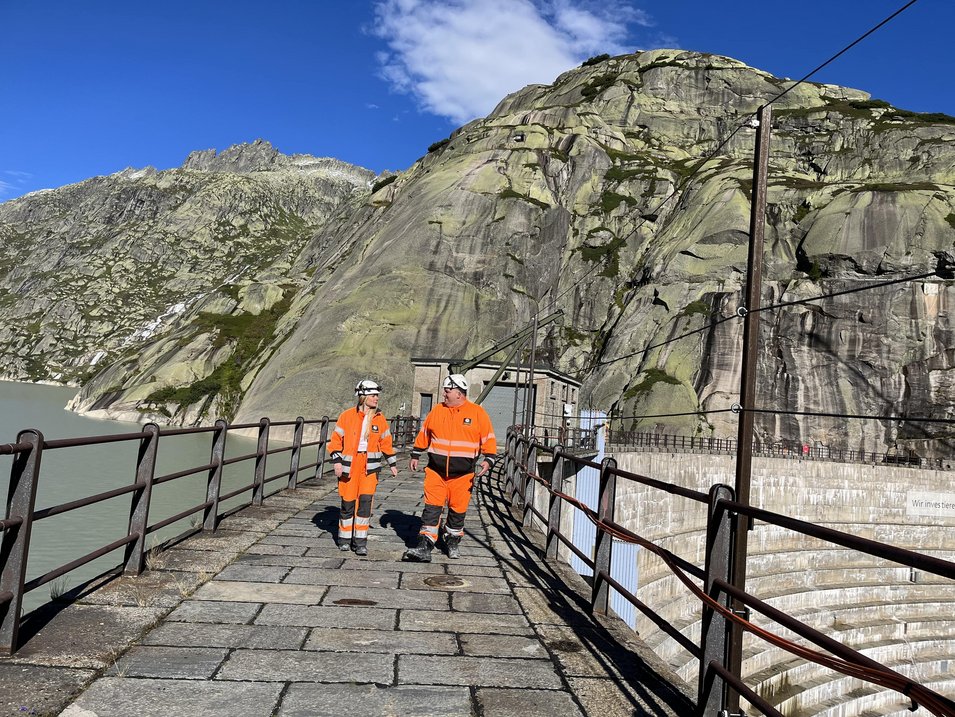
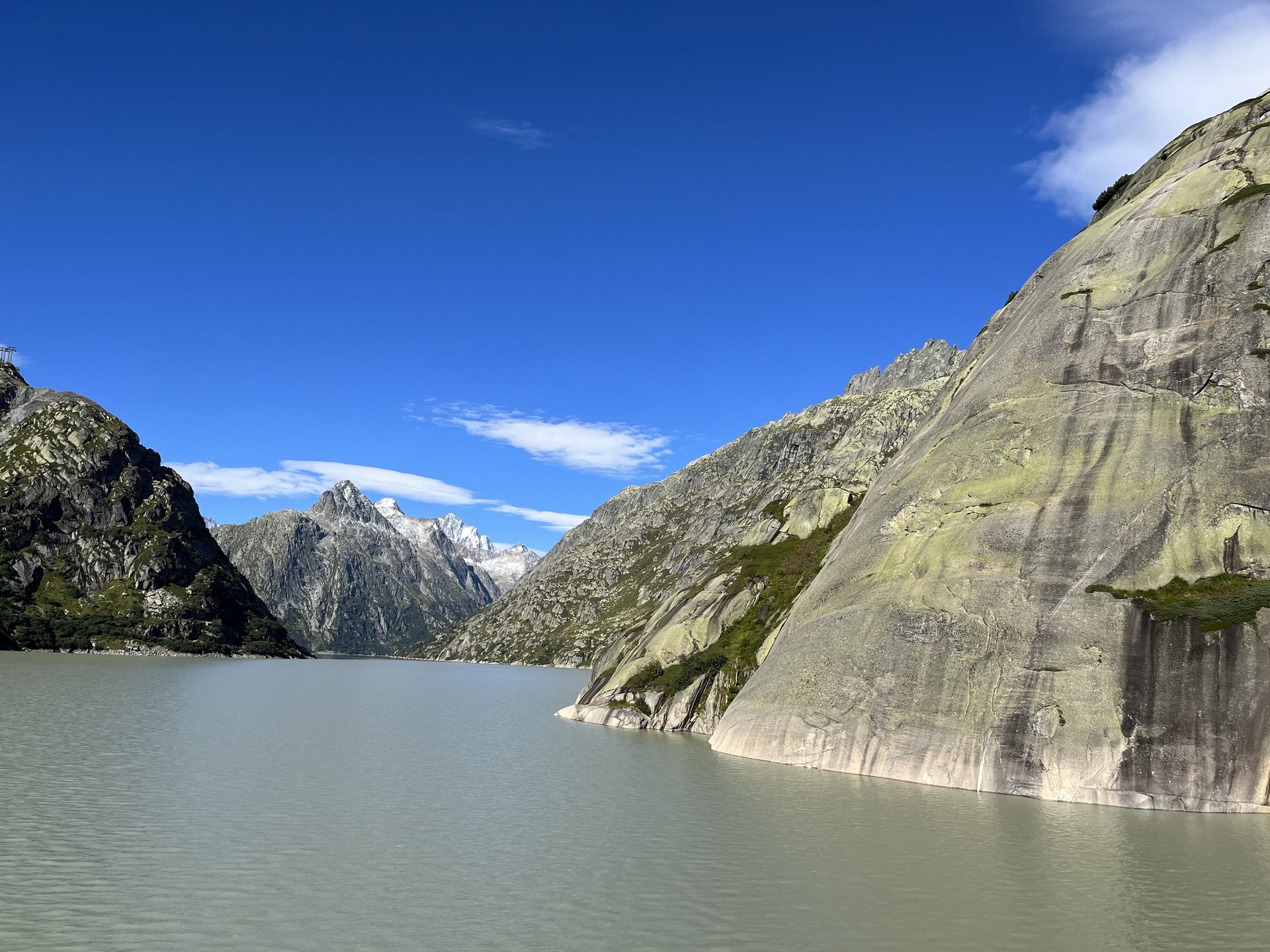
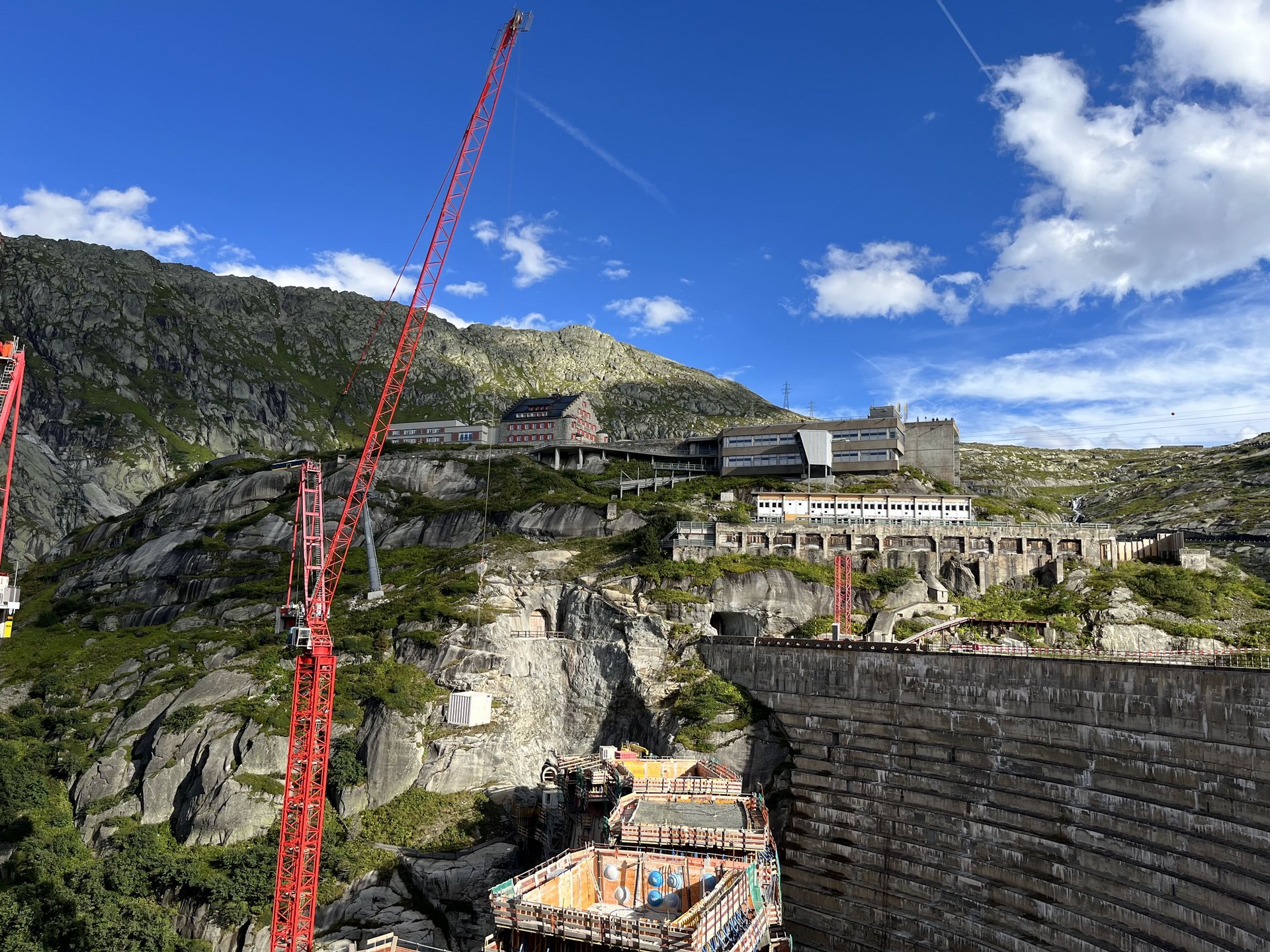
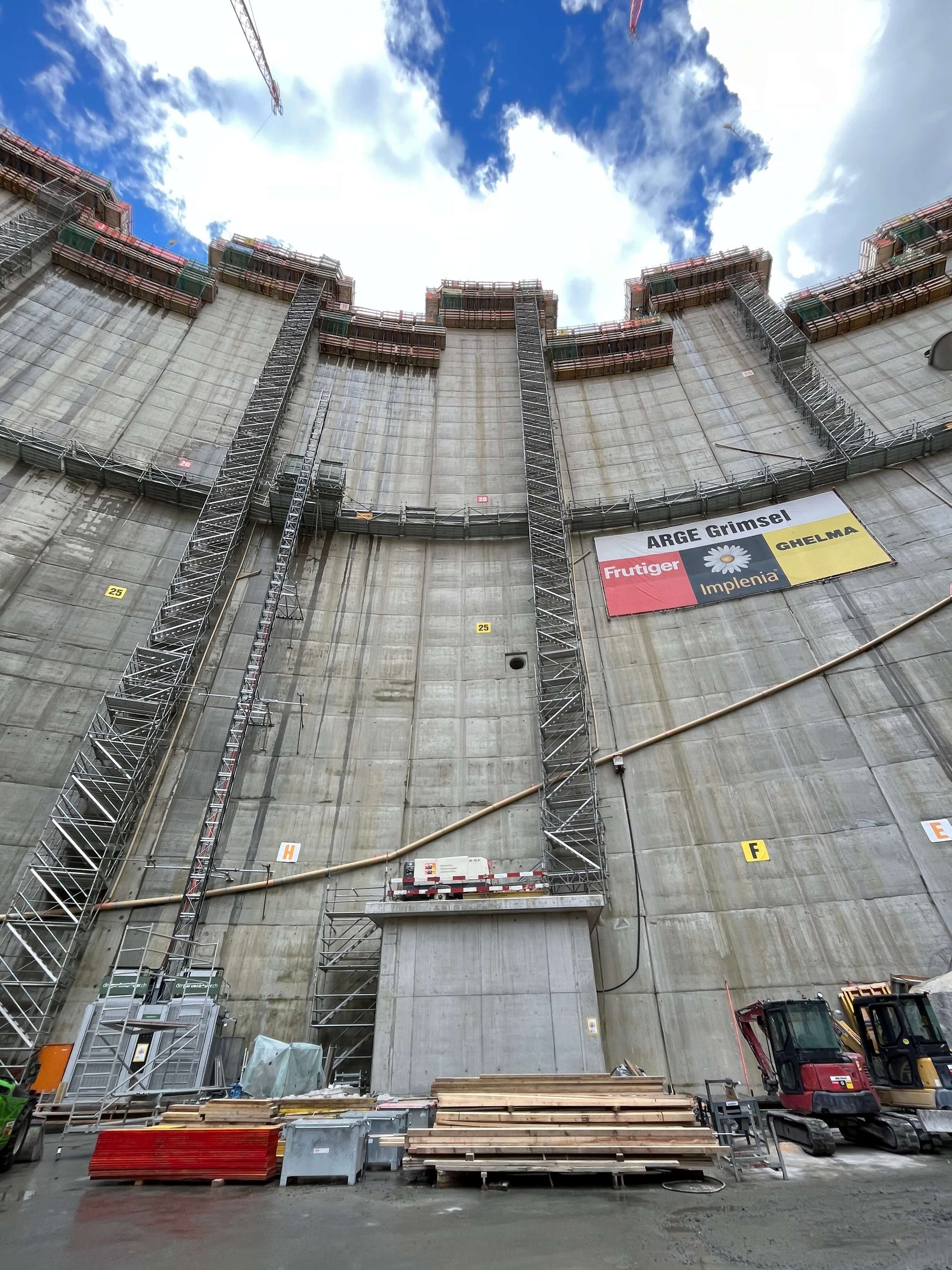
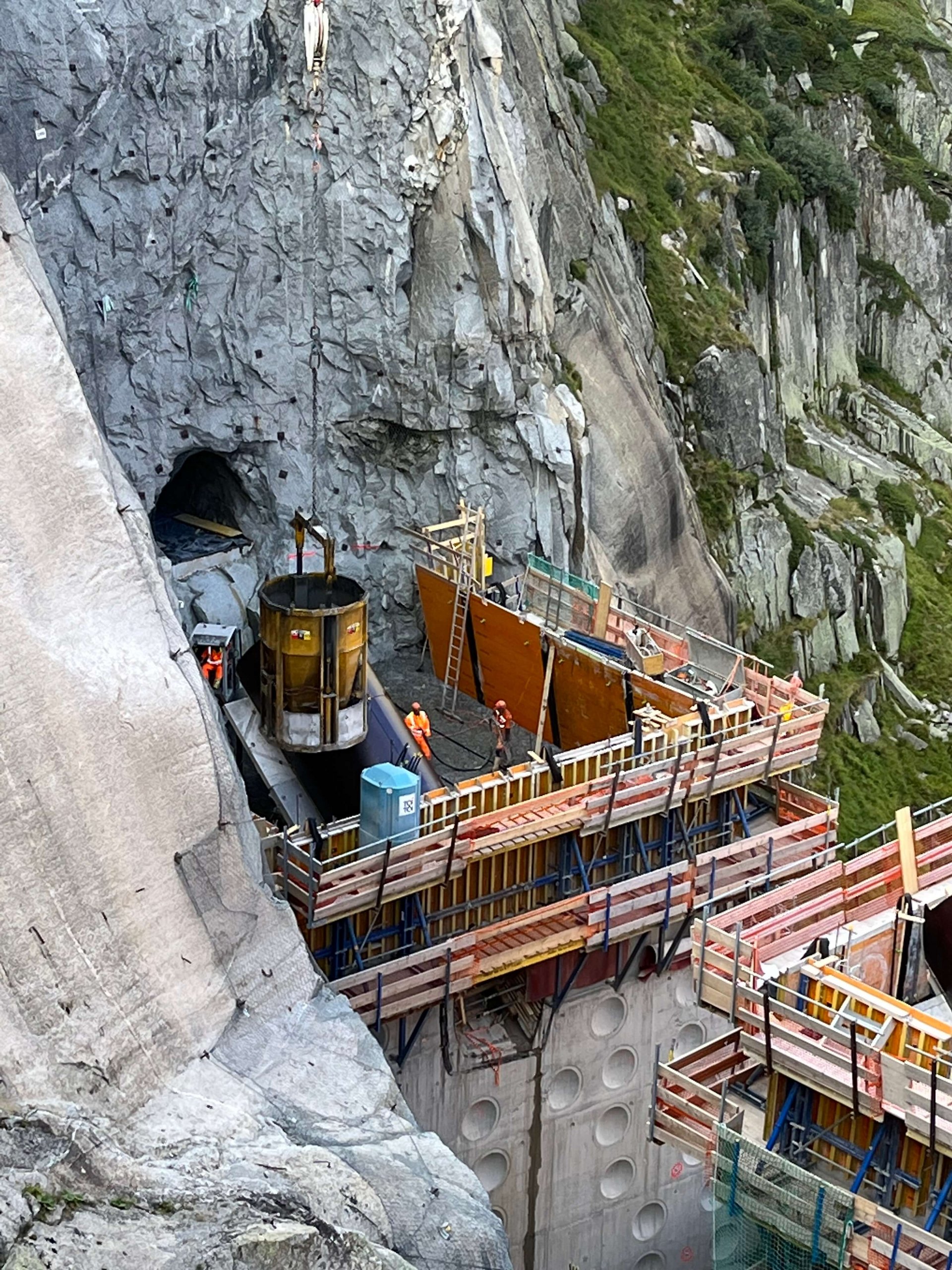