Project in focus: New construction of the Elbe bridge at Wittenberge
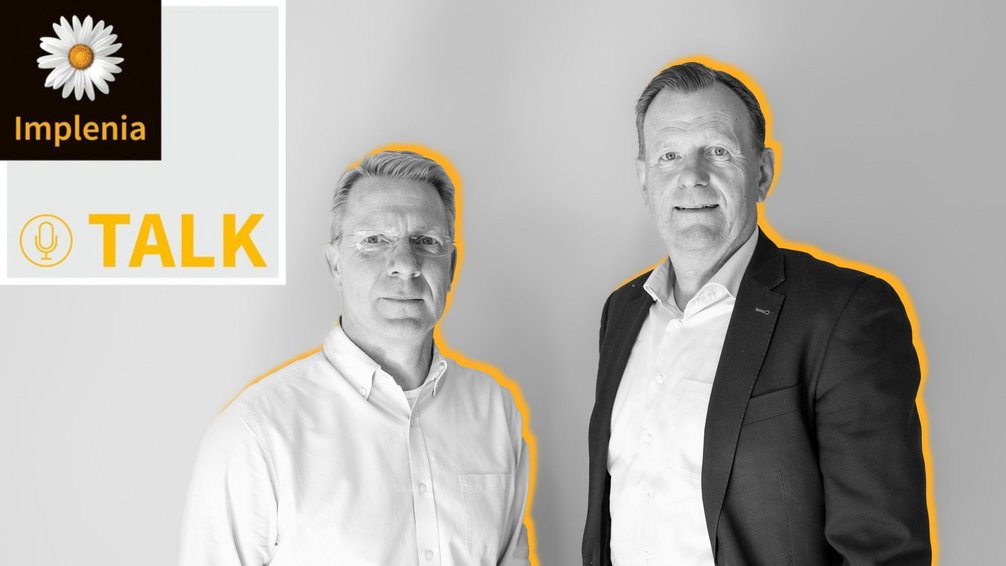
Video
The new Elbe bridge project near Wittenberge explained by our experts
PODCAST
The Implenia Talk for listening only: Click here for the podcast
Abstract of the podcast
In this video podcast, Jan Göttsche, Technical Managing Director of Implenia Civil & Specialised Civil Engineering Germany, and Senior Site Manager Lutz Geisler explain the challenges of construction in detail (the figures at the end of each section refer to the corresponding point in the video)
- Since March 2022, Implenia has been working on this project, which, upon completion in 2026, will connect the federal states of Brandenburg and Saxony-Anhalt across the Elbe. The construction is being carried out on behalf of DEGES, a German company responsible for highway planning and construction, and has a total volume of over 145 million euros. (0:30 Min.).
- Lutz Geisler elaborates on the challenges of the construction in detail. The bridge consists of two main parts: a foreland bridge and a river bridge. These will be connected during the construction process. The foreland bridge is being built in the floodplain area, while the river bridge runs directly over the Elbe. Geisler provides a detailed description of the technical implementation, planning, and construction methods used (1:40 Min.).
- The work in the water presents a particular challenge. Since there are no fixed paths for transporting the bridge components, floating elements are used to move foundation piles, foundation elements, and sheet piles. For this, a large pontoon is used to hold the equipment, as well as split barges and transport barges for material delivery and the removal of drilling debris. Lutz Geisler explains the various steps of the access routes by ship and the challenges Implenia faced in this process (2:20 Min).
- The project also faced difficulties due to flood-related issues and fluctuations in the Elbe's water level. It was necessary to precisely time the different periods, and sometimes work had to be halted (4:20 Min).
- Another focus is on environmental regulations, as parts of the construction are taking place in a Natura 2000 area. Geisler explains the necessary measures Implenia had to implement to comply with these regulations (6:40 Min.).
- Another highlight of the interview is the complex geometry and static planning of the bridge, especially the single-axis support of the steel bridge on the river piers. Geisler describes the sliding technique used and the associated logistical challenges (8:00 Min.).
- Geisler repeatedly emphasizes the enormous importance of teamwork and praises the excellent collaboration with colleagues and partners. In his view, their know-how and expertise have significantly contributed to the project's success, whether in foundation engineering (11:45 Min.) or in the prestressing techniques of BBV Systems (13:45 Min.). The interview provides a detailed insight into the technical and logistical aspects of bridge construction and explains how Implenia overcame the challenges encountered.
Transkript
Jan Göttsche: Welcome to Implenia Talk. Today’s topic is a large and complex infrastructure project: the construction of the new Elbbrücke Wittenberge as part of the A14.
Since March 2022, Implenia has been building the new highway bridge over the Elbe, which will connect the federal states of Brandenburg and Saxony-Anhalt. The structure is set to be handed over to the client, DEGES, in early 2026 and opened to traffic. DEGES, the German Highway Planning and Construction Company, plans and constructs various transportation infrastructure projects on behalf of the federal government.
The Elbe bridge is one of many large transportation infrastructure projects that Implenia is currently building for DEGES. This involves the complex construction of an infrastructure project in collaboration with our steel construction partners DSD and Stahlbau Niesky. The total value amounts to over 145 million euros. The bridge is part of the new construction of the A14 highway from Magdeburg to Schwerin, closing a gap in the German highway network.
But I would also like to welcome our senior construction manager, Lutz Geisler, who oversees the project daily. Lutz, can you tell us more about this project?
Lutz Geisler: Hello, Jan! Yes, gladly. My daughter even asked me about this project. While flying north, she suddenly sent me a photo. And as you can see clearly here, you can see our route in the lower left of the picture (image 1). You can even roughly see where the new bridge will run.
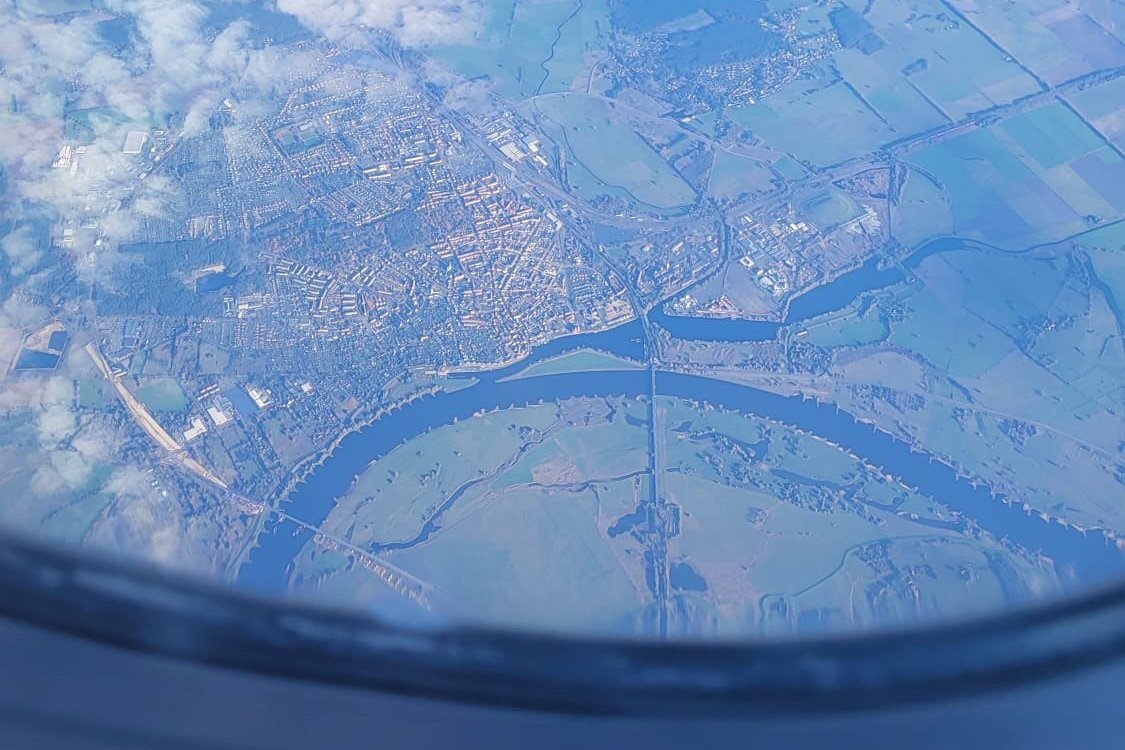
So, a project of this size, which can be seen from an airplane, is something I have not experienced in my career so far. It's something quite special. You can already see very clearly that we need two parts to create the entire bridge: one part in the floodplain area, the so-called foreland bridge (image 2) – which is about 700 meters long – and the second part, the river bridge (image 3), a steel bridge that runs directly over the Elbe. Both parts will then be connected to form a total bridge of over 1,100 meters. That's quite impressive.
Jan Göttsche: True. I also find it amusing that your daughter is watching you from above.
Lutz Geisler: I found that very amusing too! (laughs)
Jan Göttsche: I already mentioned how big and complex this project is. We are also building in the water and have to bridge the Elbe. What exactly makes this complex, and how are these measures implemented?
Lutz Geisler: Building in the water is always a challenge. There are no fixed paths or construction roads. Everything has to be brought in floating by ship: piles, foundation elements, sheet piles, and also what may need to be extracted. Even the drilling material for the pile foundation must be transported via the waterway. This makes it special because you cannot rely on mobile technology but always depend on floating elements (image 4).
Overall, we have two river piers in the Elbe. These are deeply founded, over 20 meters. It's an enormous challenge to bring together technology, personnel, and materials to execute all services precisely.
I have some pictures here. You can see what technology is being used. We have a large pontoon on which the equipment is mounted. Additionally, we use service units like split barges and transport barges for supplying materials such as reinforcement cages or for removing drilling material. We also need a pushing unit, a so-called pusher tug, for all steps – this is how the floating units are built (image 5).
The advantage of our technology is the use of leg pontoons. This allows us to always support ourselves on the ground of the Elbe and at least find a firm hold there to work safely. From our service point 3 km away, we can then transport the material logistically. If necessary, there is a small port in Wittenberge through which logistics can be carried out alternatively. The water issue plays a very special role in the Elbe.
Jan Göttsche: Let's delve a bit deeper into the water issue. When we recall the images of past floods we've experienced in Germany, it also affects the Elbe. The Elbe fluctuates greatly from season to season, and our construction site has already been affected by floods.
Show me those pictures again, I find them very impressive. I believe this picture is from January 2024. Not much work could be done then. What did you have to do to get back to work quickly?
Lutz Geisler: Indeed. During the flood phase at the beginning of the year, work in the foreland bridge area came to a complete halt (image 6). The Elbe has the peculiarity that we have no weirs in this part to possibly hold back water. Here, nature pushes through with full force. This concerns flood situations in summer, but also the low-water period, which also gave us pause for thought. That can be worrying.
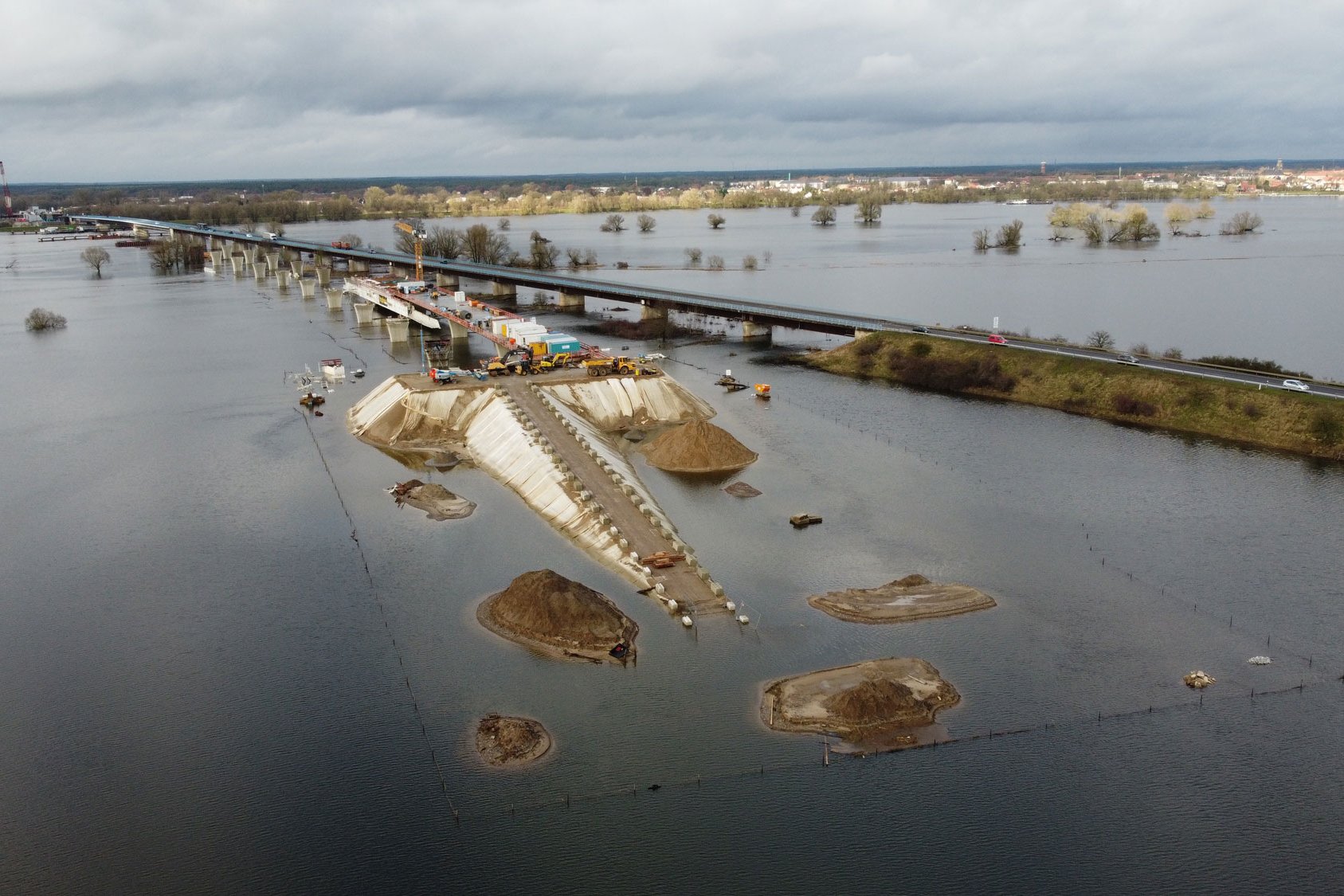
In the flood situation, we ultimately had to stop work. However, we found that we had no damage to the building substance and the completed parts of the construction site and were able to gradually resume our work as the water receded. We did this as quickly as possible.
We are currently working with our client on concepts on how to compensate for these situations as much as possible. I can elaborate on that later.
Jan Göttsche: When I look at this picture, you almost get the feeling we are working in the middle of the ocean on a large ship. On closer inspection, you can see our crane above the Implenia sign. Isn't the crane also in the water?
Lutz Geisler: The crane is not in the water. It stands on a console on the launching gantry (image 7). This is a large white steel structure that we can see below the bridge surface. The steel is deliberately mounted there to compensate for the risks of flooding that can occur here. This way, we don't have to repeatedly disassemble and reassemble the equipment, which would cause countless damages. This is an advantage to quickly get back to work – as soon as the water allows and has receded.
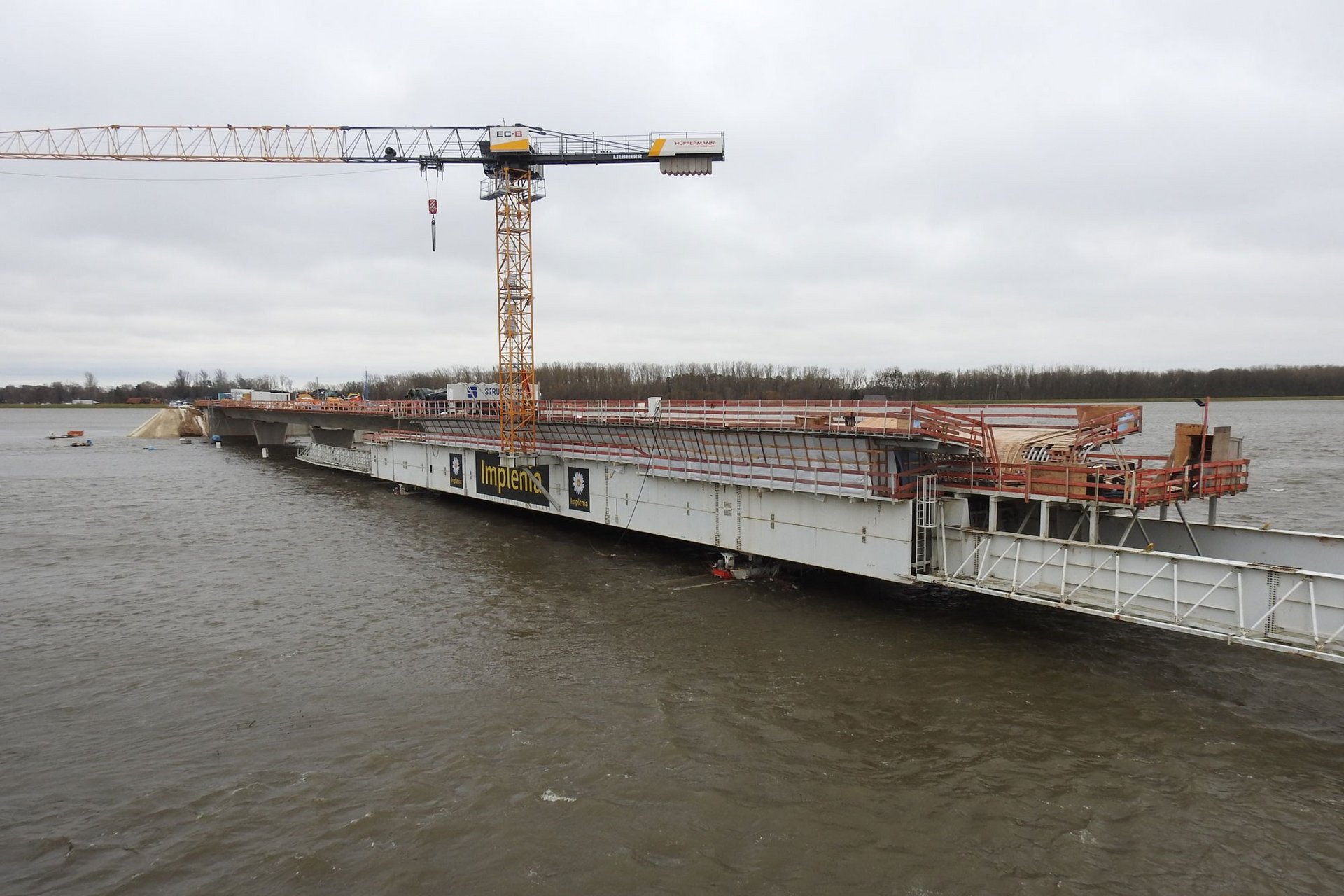
Jan Göttsche: Great! If I remember correctly from our bidding phase, parts of our construction work are in a Natura 2000 area, which really doesn't make the work any easier. How was this situation resolved?
Lutz Geisler: During the planning approval process, our client DEGES already initiated conceptual considerations to define the areas that could be used in this Natura 2000 area. Because we needed areas for construction roads, assembly areas, and storage areas, and there were very clear guidelines on what we could use and what we couldn't.
You can see it very well in these pictures: Everything green remains nature (image 8). These are the so-called taboo zones for us, which are defined exactly as such. Here you can see the construction road and the working areas around the piers where we can carry out our work. You can also see the launching gantry, which is exactly in the axes of the bridge piers. This was designed to leave the areas between the piers untouched, thus fulfilling the conservation requirements and guidelines (image 9).
Jan Göttsche: Our bridge construction includes not only a prestressed concrete solution for the foreland but also the bridge over the Elbe, a steel superstructure with a very demanding geometric design.
We have already looked at this several times: the single-axis support of the steel bridge on the river piers. Lutz, how is the planning for this bridge over the Elbe carried out?
Lutz Geisler: Absolutely, the geometry is very demanding. We have initially arranged a load-bearing element in the middle of the bridge, a so-called wave in the longitudinal direction. This is the main girder. Hollow boxes are attached to the right and left, only connected at the sides. This makes the assembly and especially the launching of the steel superstructure very complex because we can only use a central support (image 10).
You have to imagine it like a seesaw. We have to centrally support the steel superstructure and push it forward over the Elbe from pier to pier into its final position. This is a unique feature. You can see it well here: you can see where they formed the Kraken on the sides, in the lower area at the main axis where the sliding bearings and sliding supports are arranged. We can then push the entire complex over the Elbe on these (image 11).
The steel components were previously manufactured in steelworks in Plauen and Niesky. These arrive pre-assembled and are then put together on the so-called pre-assembly area. Large elements are then added. We need a total of about 80 to 90 meters to implement individual sliding states and push this rhythmically forward. We always have to maintain balance and nothing must tilt sideways or jam to achieve a stable and secure support.
You have to imagine that the bridge is pushed forward in four parts, step by step. First, we push the nose forward to create space. This allows us to weld and assemble further steel lengths on the pre-assembly area. Once we have enough overall length to reach the first pier, the first big step follows to the first river pier.
What distinguishes this from other processes is that we use steel cables and with strand jacks, we pull the superstructure towards the Elbe, moving it forward in intervals (image 12). These are large tonnages being moved, sometimes 3,500 to 4,000 tons.
Also noteworthy is the lighter nose. There we find a reduced cross-section to save on tonnage and to accurately guide the forward nose onto the individual piers. Imagine, as we push forward, the steel superstructure protrudes, bending downward, so it really dips down (image 13). This is a very challenging task to reach the first pier. The steel superstructure dips about 2.5 meters deep, so it deforms and must then be lifted over a special construction at the first river pier.
You can see it in this picture: the first lower part in the blue-marked steel structure is the so-called lifting press. With this, we lift the forward nose to then run onto the centrally arranged sliding support again. With this method, we ultimately enable stable support on the river pier and can then continue to push forward. This only occurs in the third and fourth sliding steps (image 14).
Then we can cross the Elbe and reach our final position. It takes a lot of patience and important milestones during the individual pushes that we need to achieve. That's the exciting part of this steel construction task.
Jan Göttsche: I am absolutely fascinated by your detailed explanation! I think our colleagues who listen to our podcast will particularly ask themselves one question: How do you actually manage it? How can we overcome these major challenges on the construction site?
Lutz Geisler: This can only be done as a team and through a partnership-based collaboration with the client, DEGES. But especially within the team, the cooperation must be right. Above all, know-how and commitment make good teams.
My greatest praise therefore goes to our colleagues for the great cooperation and the work done so far. We can really pat ourselves on the back for that. Let me elaborate: Our colleagues from the specialist foundation engineering were responsible for the foundation components (image 15). They manufactured all the piles – on land and in water. They used their knowledge for the floating technology, the equipment, and the service provision very profitably.
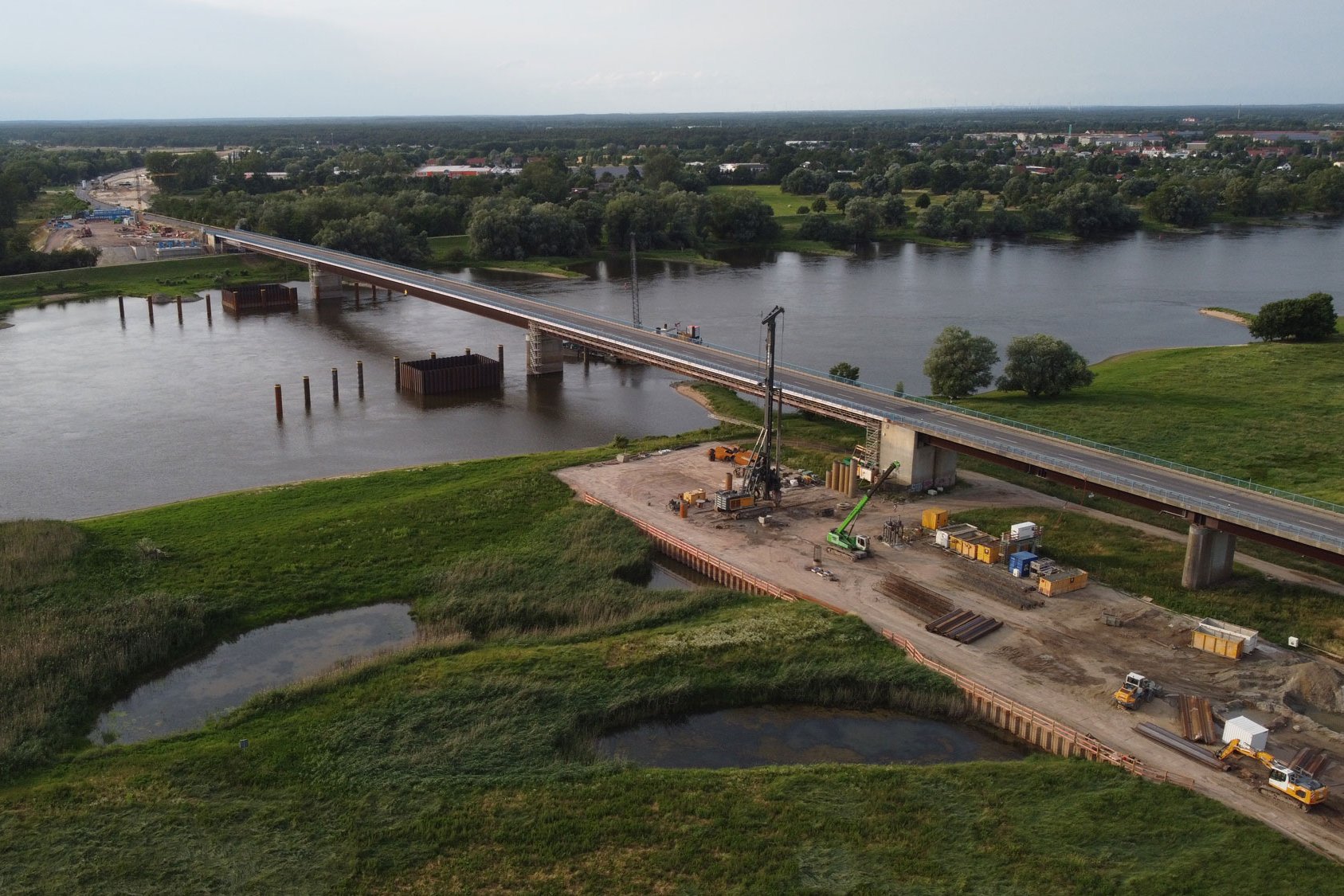
Their approach always revolved around the question: "How can we manufacture the piles as precisely as possible? How can we meet the requirements we calculated when we started the project?" Here, it became clear that an exchange of ideas led us to our goal. In this picture, you can see impressively that the sheet pile works were used as an additional component (image 16). This also had to be done floating, and this with many excavations on land that we had to move for each individual pier. Each pier contains seven long piles of 30 meters each (image 17 and 18). Moreover, the sheet piles with their special geometry also proved to be a challenge.
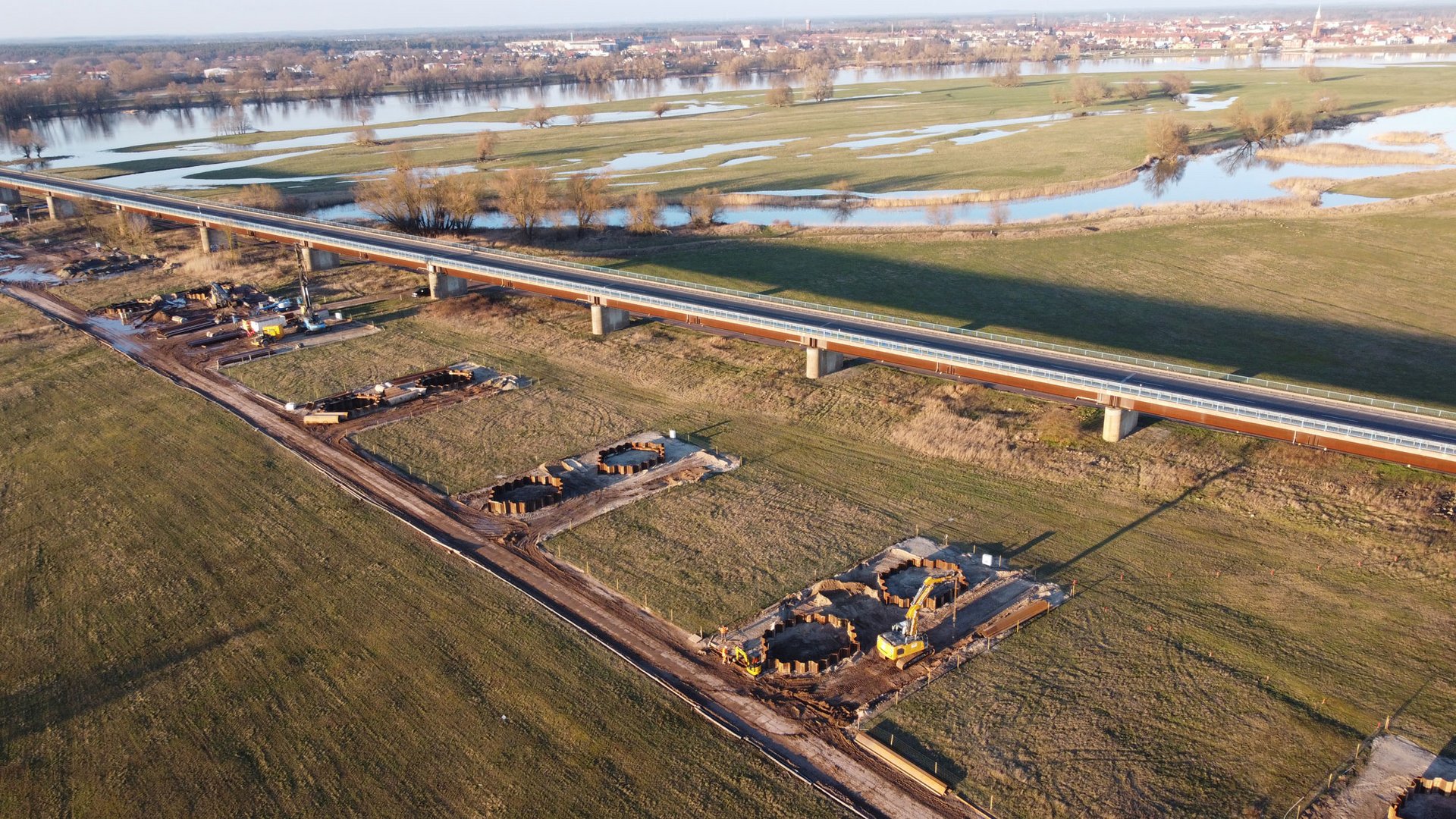
Let's take a look at the pier excavation in the water (image 19). Imagine you're floating with a pontoon with heavy drilling equipment in the Elbe. You can't see through the water or see the starting point. Nevertheless, it shows how precisely the location of the piles and the axes were maintained. This great work in specialist foundation engineering laid a good foundation for the further measures. Then the concrete was supplied, and the pier was built. These are the foundations for all bridges that are deeply founded. It's very impressive.

Jan Göttsche: The bridge on land is a prestressed concrete bridge. Collaboration with our BBV was a perfect fit. That's what we did. Can you tell us more about this prestressing technique and the cooperation with BBV?
Lutz Geisler: Sure. In this picture, we see the superstructures in the foreland area. These are concrete superstructures that are longitudinally prestressed. In addition to the concrete and reinforcement steel, prestressing steel elements are installed. Here, you can see the tubes and sheaths (image 20). Both the arrangement and the height are crucial. The tendons give the superstructure its key properties. Regarding the stress distribution and deflection, this is an important component that was integrated here.
The colleagues at BBV manufacture, deliver, and install these prestressed concrete elements. The strands, as they are called, are tensioned and grouted after concreting when the concrete has reached its strength. In this picture, we see the completed superstructure. It takes about 50 hours for the concrete to reach the strength we need. Regardless of weekdays, Saturdays, or Sundays – the colleagues helped us and tensioned the strands and prestressed the concrete to achieve the ideal condition.
Jan Göttsche: So they come to the construction site every two weeks just for us, tension the strands, and install them?
Lutz Geisler: Exactly. For each superstructure, the colleagues help and support us. Here we have a picture of a completed cross-section, looking into a concreted and prestressed section. You can see the roles very well, which will then be installed in the next superstructure, and the blue caps are partly end pieces, that is, end prestressed or tendons that are extended and coupled to be continued in the next superstructure (image 21).
This internal collaboration with our partners can really only be praised.
"Especially in such complex projects as this one, it is crucial that everyone pulls together and masters the challenge as a team."
Jan Göttsche
Jan Götsche: I also think this collaboration is further facilitated by the newly introduced organizational structure. We have merged the engineering and specialist foundation engineering units into ICS Germany.
Especially in such complex projects as this one, it is crucial that everyone pulls together – as you just explained. This way, we can tackle this challenge together as a team. The initial experiences are very positive and confirm that we have set ourselves up correctly.
We have now reached the end of our conversation. I am Jan Göttsche and I thank my guest, Lutz Geisler (image 22). The Elbe bridge is expected to be completed in early 2026 and will then close the gap in the German highway network.
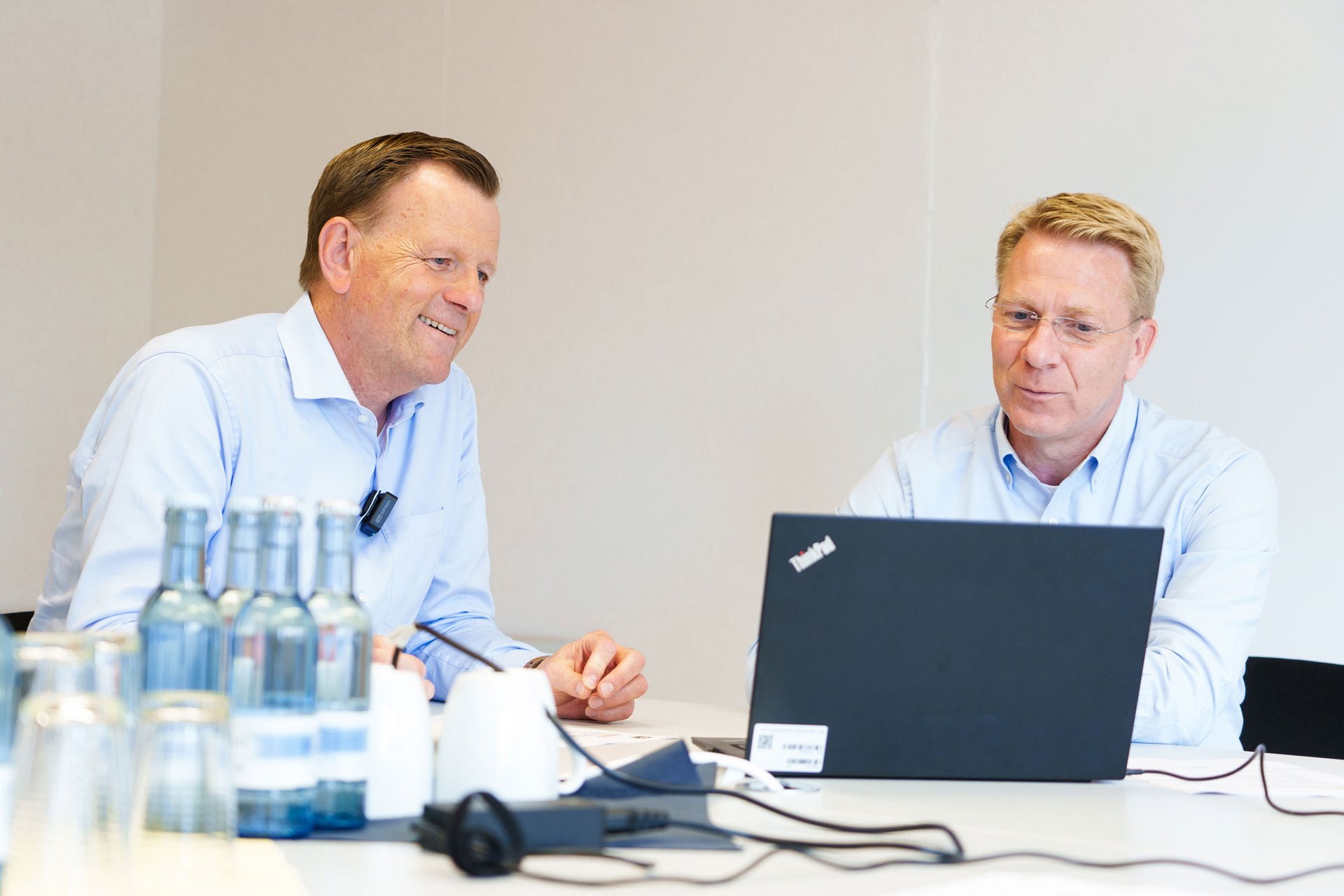
Did you enjoy the podcast? Do you have any suggestions or topics you'd like us to cover? Then write to us at: redaktion@implenia.com
We look forward to an exciting exchange and will stay on top of the topics that matter to you. Until next time!