A power team for the Marienhof project
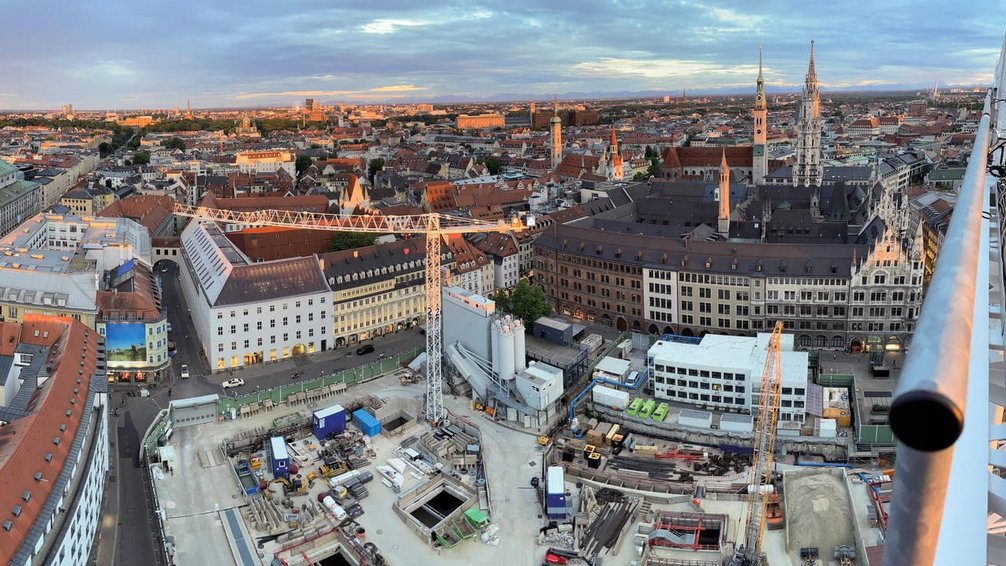
This article has been produced jointly by the Communications departments of Implenia and HOCHTIEF.
It is a hot July day. The sun beats down on the Marienhof construction site, stretching to 5,500 square metres. The 30-yearold Japanese pagoda trees that provided such beautiful shade here until 2011 have found a new home in the city’s arboretum in Allach. Once construction is completed, a host of new trees will be planted in the green space in the heart of Munich, behind the town hall.
New construction 42 metres underground
But beneath the former green space at Marienhof, nothing is what it was. Embedded in six alternating sequences of tertiary clays and sands, 200,000 cubic metres of reinforced steel will carry a construction that stretches up to 42 metres underground and will improve the infrastructure for Munich’s local public transport in a sustainable way. The new commuter rail station is part of the 10-kilometre second trunk section that crosses the centre of Munich largely underground – from Laim in the West to Leuchtenbergring in the East – passing under houses and business, churches and museums, and even existing stations and tunnel systems for the current underground and commuter railways.
Marienhof: A construction site of superlatives
42 | meters deep—the equivalent of a 15-story house, built downward |
100 x 55 | meters—the size of the area being dug into the depths |
210 | meters long—how long the underground station will be in order to accommodate the 180-meter-long suburban train |
267,500 | cubic meters of earth will be excavated for the construction, including the finest tertiary sand |
200,000 | cubic meters of concrete will flow into the structure |
15,700 | square meters of slurry wall is being used ‚ to stabilize the excavation pit |
50 | primary columns, anchored at depths of up to 70 meters, support the structure |
136 | wells and groundwater measuring points have been dug for drainage |
A total of 2,000 | measuring units have been installed on and around the construction site to warn of the subsidence of the adjacent development |
Zur Projektwebsite der Deutschen Bahn: www.2.stammstrecke-muenchen.de/marienhof.html
No one has ever dug deeper in Munich
The crowded space underground has forced the construction companies to dig deeper than anyone in Munich has ever done before – an undertaking made all the more difficult by the crowded space above ground. “One of the biggest challenges in this project full of challenges is logistics,” stresses Jens Classen, who heads the Marienhof syndicate as overall project manager. “We are bringing enormous machinery into extremely tight spaces in the centre of a very busy city, ideally without being seen and, above all, heard.” “Anyone who wants to build here needs to be proactive in their efforts to nurture good relations with their neighbours,” adds Michael Müller, Construction Manager and deputy overall project manager.
“One of the biggest challenges posed by this challenge-packed project is the logistics.”
Jens Classen, Overall Project Manager Marienhof joint venture
One example he mentions is the city’s mayor, whose office is in the town hall next door. “We talk to each other all the time. Today, for example, the Bettenrid store is having new shop windows delivered in the central courtyard directly opposite, blocking our access to the north of the site. We need to find a solution.”
Complexity at every level
Finding solutions is the central theme of this project, which unites the two major construction and real estate corporations in a joint venture. This joint venture in turn works closely together with the client, Deutsche Bahn, and numerous subcontractors.
“It is rare for a construction site to bring together so many different disciplines and for every single one of them to face such enormous challenges,” says Michael Müller, describing the complexity of the project. In the first phase of the construction project, Special Foundations had to erect 15,700 square metres of diaphragm walls and 50 primary supports extending up to 67 metres into the ground.
Constant measurements and stabilisation measures
To ensure that neither buildings nor existing rails are damaged, the consortium installed a measurement system with around 2,000 measurement units and well over 5,000 individual sensors that constantly deliver data on subsoil and building movements. Drilling for extensive elevation injections will begin in late 2022; these prevent the surrounding buildings from subsiding as a result of settling following the tunnelling. Another issue is dealing with ground water. More than 130 wells ensure that the water pressure on the surrounding diaphragm wall and tunnels does not become excessive. The water treatment plant to the south of the site prevents potential contamination from the site’s waste water from entering Munich’s water supply system.
Currently, the engineers are working to produce the first ceiling under the top ceiling (E-1), eight metres below ground. This involves joint venture 72-metre special crane, capable of lifting loads of up to 48 tonnes. This transports reinforcement rods through one of the openings on the level below, supported by just one member of the joint venture team in the burning July sun. The rest of the crew is enjoying more comfortable temperatures below ground.
Long-planned collaboration
The project would be a technical and logistical challenge. The joint venture partners therefore put a great deal of work into the very long bidding process, which went on for almost three years. This period brought them very close as a team, says Jens Classen. “The good thing about our joint venture is that a lot of people from both companies moved into the project directly from the bidding phase. That allowed us to use their expertise, and meant that we didn’t have to integrate a lot of new people into the team.”
Today, the Marienhof team benefits from the combined expertise of two major construction companies. Does tension ever arise? Jens Classen: “Not really. Despite all our experience, we are all learning all the time – including from one another. For example, we use HOCHTIEF’s SAP system for our invoice checking. In return, Implenia contributes the quality management system and the iTWO software solution for controlling.”
Making the partnership work demands a solid basis of trust and a conscious commitment to avoiding turf wars. After five years of collaboration, such conflicts are no longer an issue between the joint venture partners, says Michael Müller emphatically. “The good thing is that we can put all our expertise into the technology and the project – that is what makes construction fun.”
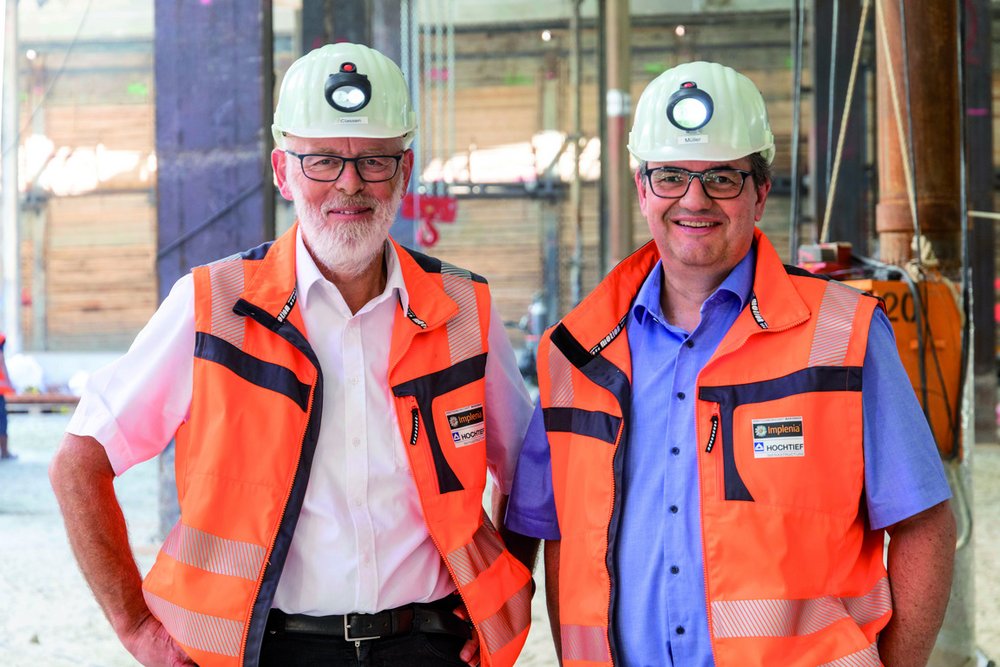
Joint Venture Teams
The Marienhof team can draw on the concentrated know-how of two major construction groups. In the following, we give some examples such as overall project manager Jens Classen from Implenia and his deputy, construction manager Michael Müller from HOCHTIEF. Together, they steer the fortunes of the Marienhof consortium.
Home game in Munich
The motivation to help build the Marienhof is palpable throughout the team. “Many colleagues have moved to one of the companies to be part of this project,” says Classen. Especially veteran Munich tunnel builders were keen to be part of this project on their own doorstep. That is why many employees from both HOCHTIEF and Implenia are involved who have already had a lot of experience with large projects – and who now form the basis of this project.
At the same time, there are also many young people in the ranks of the Marienhofler. They learn in the slipstream of the experienced team, so to speak, how to successfully set up a large project – and they also get the chance to switch to another area again and again to gain new experience there. “In addition to their drive, the junior staff also bring along their know-how regarding digital working methods and thus complement us old hands,” Classen emphasises. “In this respect, it's a very pleasant mixture!”
Geglückter Know-how-Transfer
Like everywhere else in the construction industry, there is a lack of mid-level staff at Marienhof: for 20 years, only a few new people were hired. This makes it all the more important now to pass on the know-how of experienced colleagues to the next generation and thus keep them in the project. “Many of the older employees will retire during the project. That's why we deliberately paired experienced people with young people within the teams – the combination is almost unbeatable.”
Face-to-face discussion is also a major feature of the very friendly atmosphere in the construction office. Most people here do not even know for sure who joined the group from Implenia and who from HOCHTIEF. They are one team.
The ABCs of joint venture success
CHEMISTRY
New team members must not only have the necessary qualifications; they must also fit into the team on a personal level to ensure the right atmosphere.
CONTINUITY
With respect to the Marienhof joint venture, the majority of those involved have been working together since the bidding phase and now make up a well-established team.
ENTHUSIASM
The Marienhof team feels privileged to be able to make an important contribution to this once-in-a-century project in the heart of Munich.
EXCHANGE
The Marienhof team discusses issues in an open and sometimes heated manner in order to find the best solutions for the project and to ultimately pull together.
PLANNING
The Marienhof team puts an above-average amount of energy into planning in order to enable adjustments to be made at short notice—despite the tight schedule.
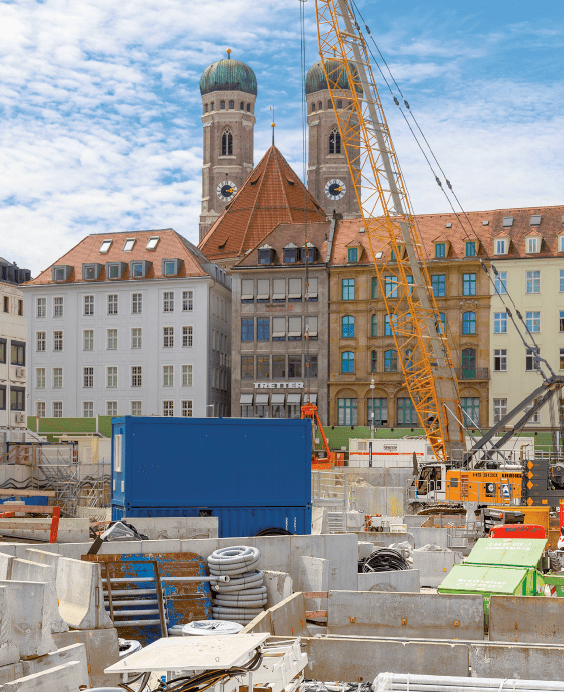
Open communication
Relations with the client, Deutsche Bahn, are also maintained proactively – supported by a shared understanding that both parties want to advance the project through collaboration. “The approach has allowed us to optimise the project right from the bidding phase,” believes Jens Classen. “The lean concept, which is set out in the contract, also brought us together very quickly, especially at the start of the project, in workshops with the client, the planners and construction supervisory bodies.”
According to Jens Classen, the collaborative, lean-based relationship with the joint venture and project partners forms the foundation on which hybrid largescale projects can be conducted efficiently and profitably. Preventing conflict allows everyone involved to concentrate on resolving complex technical challenges and on processing and negotiating follow-up orders quickly. When you put them all together, these factors deliver a stable, constant contribution to success.
Investing in staffing levels
The consortium also consciously invests in resources. “We have a more appropriate staffing level than on other major construction sites,” explains Michael Müller. “The fact is, with execution planning and work preparation running in parallel, followed by implementation at very short notice on site, more staff are needed in order to prevent time being lost or quality suffering. Here at Marienhof, for example, we have invested in planning coordination to ensure that the plans made by the client are actually implemented.
When problems emerge, we sound the alarm early – and put our energy into finding solutions, rather than resolving disputes.” Open exchange creates an understanding of the issues, problems and challenges faced by the other party in each case – and using this communication saves the team a great deal of written correspondence and subsequent negotiation. “We ask where the problem is, and then we work together to find a solution. And we do this as a team, not against one another – both within the joint venture and with the client and subcontractors,” says Müller.
It is no wonder that the project is a kind of flagship: for successful collaboration in a joint venture, as well as for solution- orientated execution of a complex infrastructure project. This all prevents unnecessary costs and helps avoid any unnecessary extensions to the construction period. It is why Jens Classen and Michael Müller are so annoyed that recent discussions in the press about extended construction periods and increased costs have shown Marienhof in a bad light. “It’s nothing to do with our work!”