Grand Paris Express: drill, sink, repeat
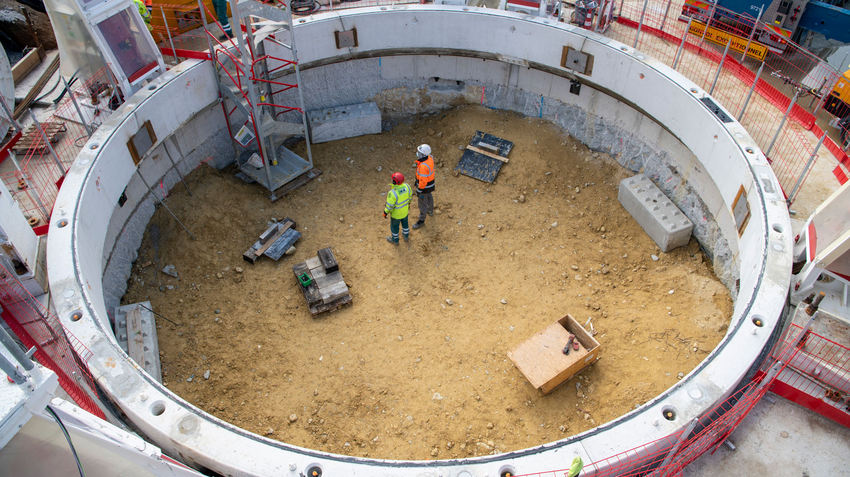
The Grand Paris Express is one of the most ambitious construction projects of the 21st century, not only because of the size of the infrastructure and the budget, but also in terms of the civil engineering techniques required. Implenia is proud to be playing an important role in the project, which also gives the company an opportunity to demonstrate its mastery of the very latest technology. For example, we are using VSM technology (VSM = vertical shaft sinking machine) developed by German manufacturer Herrenknecht to sink four shafts, the first two of which were completed in January 2021 and May 2021 respectively.
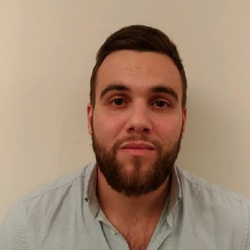
“The VSM method allows simultaneous excavation and installation of the concrete segments, which are driven into the ground as excavation progresses. This reduces the length of the job, the amount of concrete used, the volume excavated, etc.”
Hugo Launais, Plant Engineer
VSM technology facilitates the construction of vertical shafts below groundwater level using a roadheader and concrete segments. Traditionally, this type of project would rely on diaphragm wall construction; but the structures located around the future metro line 17 leave little room for manoeuvre. The use of VSM technology allows us to significantly reduce the size of the construction site. It also cuts construction time, because excavation and lining take place at the same time – a huge advantage when running a construction site in a congested urban area. There is also much less noise generated than there would be if we were using diaphragm wall cutters and earth-moving equipment. The technology also complies with all the altitude restrictions that apply in the vicinity of the airport.
How it works
The vertical shaft sinking machine has three main parts: the shaft boring unit; the spoil removal system and the lowering unit. Unlike horizontal tunnelling machines, instead of a cutting wheel the VSM system has a rotating cutting drum, mounted on a swivelling telescopic boom, which excavates the shaft and removes the spoil. This excavated material is removed hydraulically through a submersible pump and transported to a separation plant on the surface. The water is separated from the rock and soil and returned to the shaft. At the same time, the shaft lining is assembled on the surface from precast concrete segments, which are continuously lowered into the shaft.
THE TECHNOLOGY
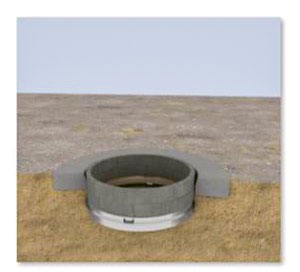
1 | The first ring of the shaft lining, the “cutting edge”, is put together before the machine is installed and placed on the surface site of the shaft. Subsequent rings are built on this so that the shaft drilling machine can be installed within them. Three arms on the machine are fixed to pre-installed steel elements to brace the machine in the shaft. The shaft is connected to the lowering unit with steel cables to keep it in place. In this way, the entire shaft structure can be held and lowered in a controlled manner. |
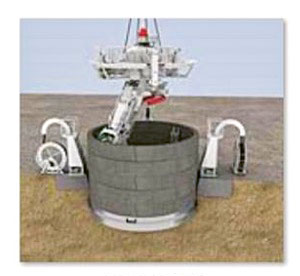
2 | As the VSM gradually drills into the ground, the prefabricated concrete rings that form the shaft wall are installed at the upper end of the shaft. As the shaft is sunk, they slide into the hole and the next ring can be placed on top. |
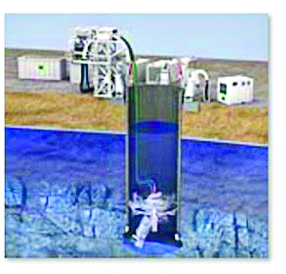
3 | This process continues until the shaft reaches the desired depth. The vertical shaft sinking machine is designed to work under water in order to balance the pressure and prevent earth movements |
In-house production
The concrete segments are made in Implenia’s own production facility in Limoges-Fourches, so we can control the planning, the quality of the segments and their structural resilience. The segments meet the Grand Paris Express specifications (load cases, exposure class, material performance) and are manufactured using a new-generation procedure.
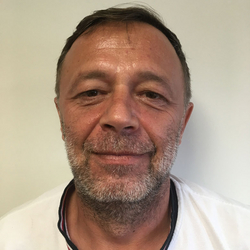
“Producing segments for the VSM required engineering work to ensure all the components were integrated and to adjust our protocols to suit the specific properties of the products. This helped us master the process and become one of only two producers in France known for a technical solution that we really believe in.”
Arnoux Cornille, Director of Prefa
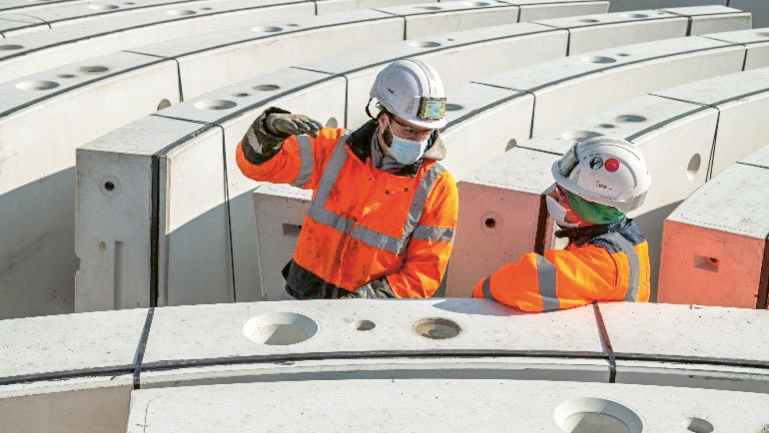
Once excavation is complete, the shaft floor is poured and barrier mortar is injected between the vertical walls and the surrounding ground. As soon as everything has cured and hardened, the water in the shaft is pumped out. The concrete segments ensure that the shaft remains waterproof.
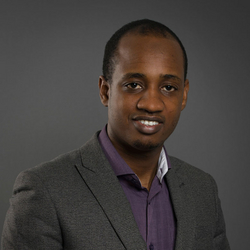
“With this method, all the work inside the structure is carried out without the need for human intervention. This reduces the stress on our people created by vibration, dust and fumes. The excavation work is remotely controlled from the surface and carried out below groundwater level. Because there is no need to reduce this level artificially, the risk of unexpected subsidence is greatly reduced. And the method is also more environmentally friendly because we have less excavation slurry to deal with.”
Mohamed Talla, QSE Manager
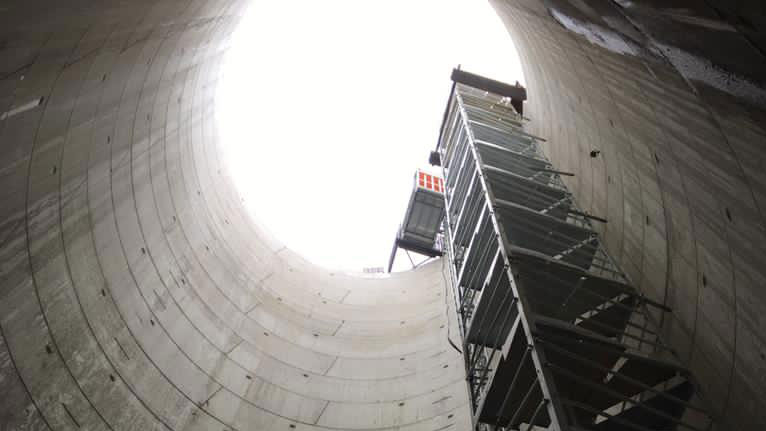
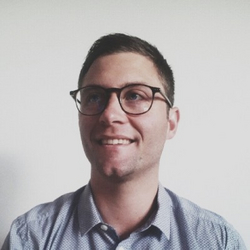
“Feedback from the first complete drilling shows that the technique is well suited to the Paris underground. The drilling went smoothly overall and came in on budget. This test drilling makes us confident about the next shaft we’ll be drilling on the site, and we’re thinking about using the same technology on other projects.”
Thomas Brochot, Plant Engineer