Where ships take the lift
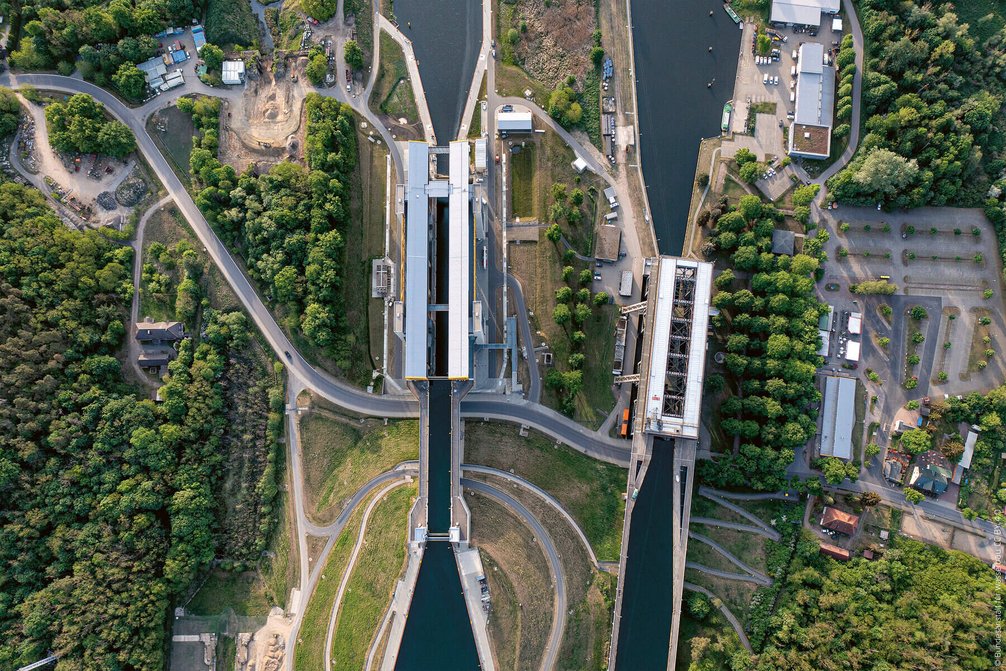
When travelling between Berlin and the seaport at Stettin in Poland, large modern goods ships came across a bottleneck. The old Niederfinow Boat Lift from 1934 was too small for today’s fleet and had become very expensive to maintain. The new lift solves the problem. Looking to the future, it was designed to allow 110-metre-long, bi-level loaded container ships to pass through the Oder-Havel Canal. The system works like a giant elevator: ships are raised or lowered in an enormous trough to overcome the 36-metre height difference between the two rivers. The raising or lowering process lasts approximately three minutes, with the entire process from entry to exit taking around half an hour.
The new Niederfinow Boat Lift has been built on behalf of the Federal Waterway and Maritime Administration (WSV), with technical leadership by Implenia in a joint venture with its partners DSD Brückenbau, Johann Bunte and SIEMAG TECBERG.
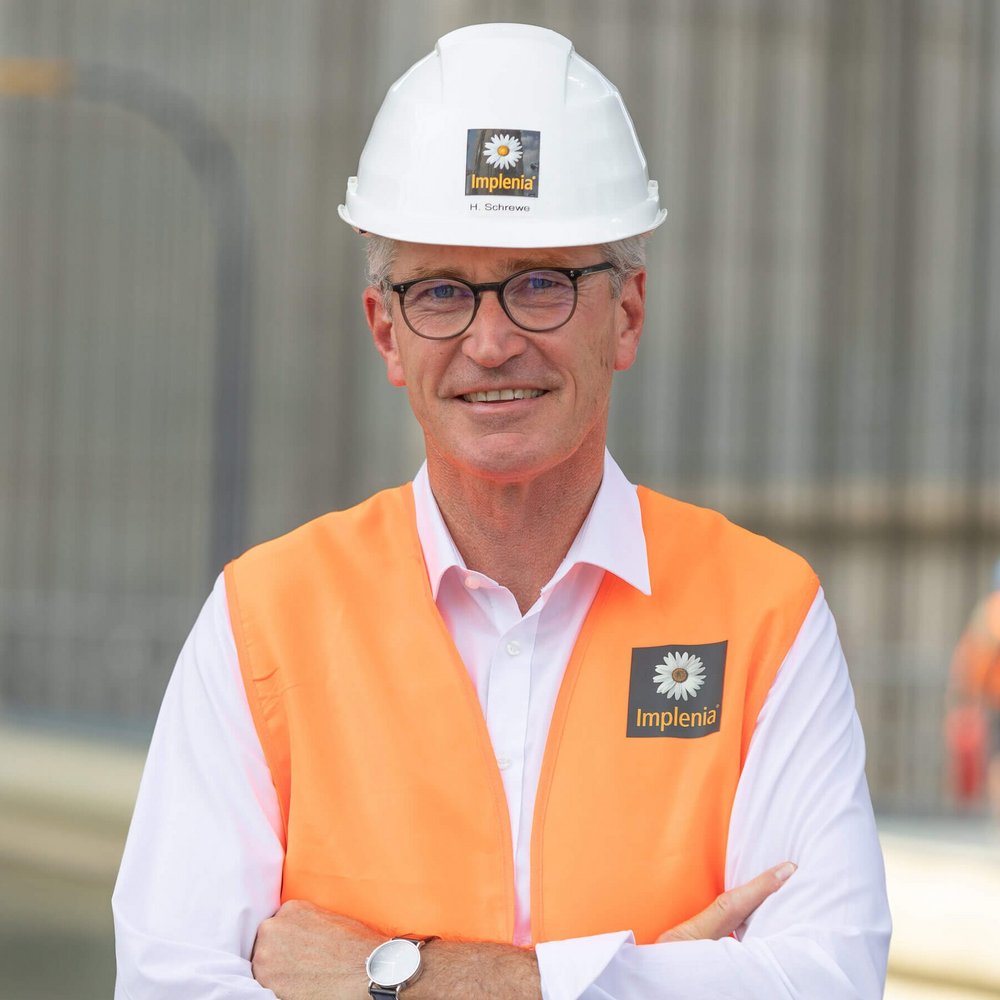
“It was an extremely challenging project on a gigantic scale.”
Henning Schrewe, Head Civil Germany
“This was an extremely challenging project on an enormous scale,” says Henning Schrewe, Head Civil Deutschland. And it was a project in which Implenia was able to contribute once again prove its expertise in the implementation of complex projects. “We are all very proud that we are now in a position to hand over this impressive structure to the client for operation.”
In house disciplines ensure success
The construction period between 2008 and 2022 was not only long, but also intensive – from the very beginning. “Many aspects of the planning put out for tender had to be reexamined. As a result, we produced a completely new full structural analysis and deformation calculation while construction was already ongoing,” explains Project Manager Carsten Genetzke. “It was so lucky that we were able to provide this service for Implenia’s part of the project from our own technical office and thus to ensure close collaboration with the construction site.” Incorporating Implenia’s own expertise was also a central success factor when it came to building the load bearing structure from reinforced concrete, which was subject to very strict tolerance limits. “We could count not only on a motivated and highly qualified team on the ground, but also on the services of our Special Foundations, Formwork Construction and Concrete Laboratory departments – it was a truly integrated project.” Skills and expertise from Implenia’s Engineering, Special Foundations and Civil Engineering departments were all incorporated throughout the project.
Engineering and management expertise needed
Just as ships are transported up and down in the lift, there were also highs and lows during the construction period. “We as a construction company wanted to complete our construction role in line with the contract we had signed, to the specifications in the design, and within the planned schedule; and we had to think about the economics of the construction site. Meanwhile, our client wanted the highest quality in line with the latest standards and had to keep its planned budget in mind. And between us lay a contract that needed to be drafted and brought to life,” explains Henning Schrewe.
Essential to the project’s success was the firm intention of all parties involved to bring the project to a close together – despite all the challenges – and to make the necessary decisions with the involvement of all experts involved. That took intensive discussions and a willingness to compromise on the part of both client and contractor. “Once we had completed the project to a high degree of quality, which was acknowledged by the client, we were able to agree remuneration in line with the market for the additional services and construction period needed. Ultimately, both the client and the contractor were equally satisfied with the construction service and the business results of the project.”
In future projects involving the German waterways, a charter will govern the most important aspects of collaboration on construction sites. This charter is the result of dialogue between the Federal Ministry for Digital and Transport, the WSV, the Verband der Bauindustrie, and construction companies and partners in various projects.
Carsten Genetzke also knows that, “for all the standardisation in engineering, this project also needed a high level of creativity and the ability to communicate.” Be it technical aspects or contractual considerations, Implenia was involved in finding solutions to a wide range of problems, all of which needed to be discussed and implemented in a very large team. This process was helped along by a number of factors: knowledge transfer was guaranteed at all times thanks to continuity of management, there was close collaboration with the joint venture partners, and teamwork happened easily across the various levels of the hierarchy.
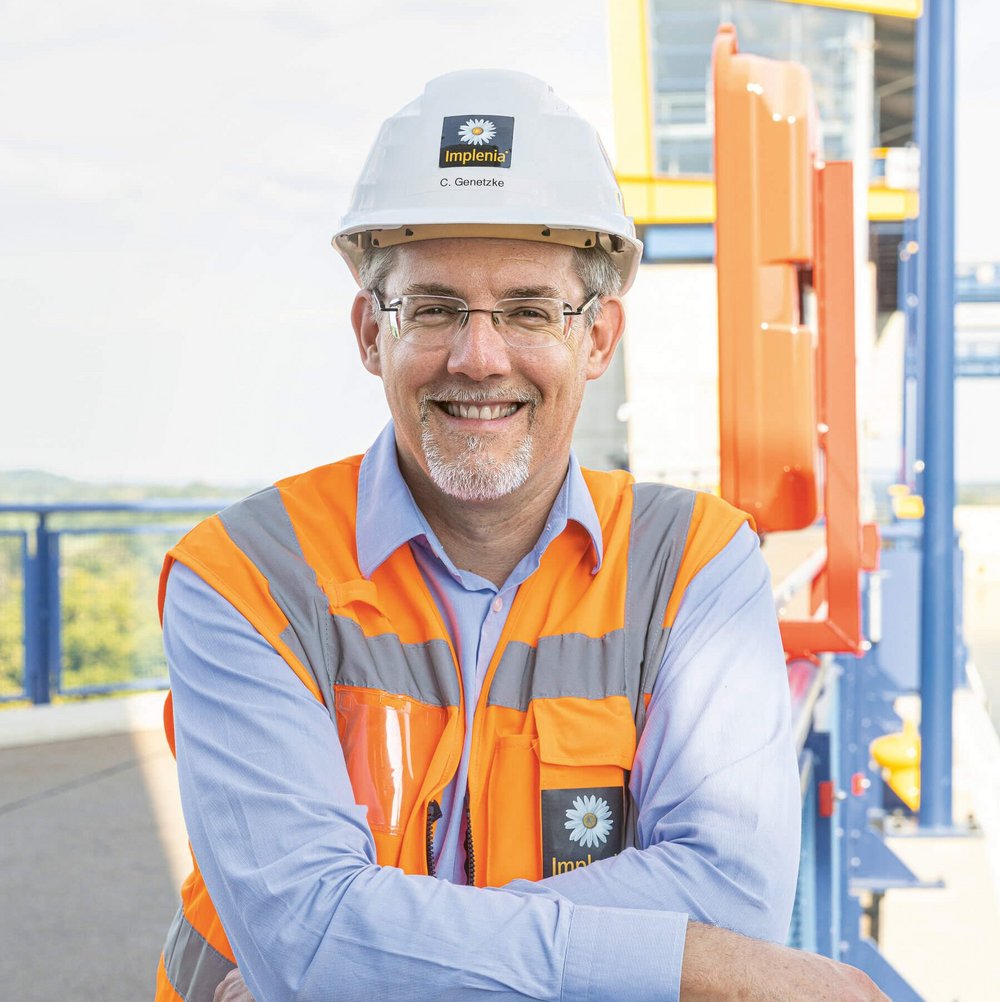
“For all the standardisation in engineering, this project also needed a high level of creativity and the ability to communicate.”
Carsten Genetzke, Project Manager
A masterpiece of mechanical and construction engineering
All in all, the new Niederfinow Boat Lift took around 65,000 cubic metres of concrete and reinforced concrete, 8,900 tons of reinforcing steel and 40,000 cubic metres of sheet pile steel. The dimensions of the massive structure are as impressive as that suggests: 55 metres tall, 46 metres wide and 133 metres long. “One of the aspects we had to consider when implementing the project was the fact that the four separate pylons become warped during different loads. The pylons were therefore constructed prewarped, so that they stand vertical once the loads are applied,” explains Henning Schrewe. But the boat lift is also a masterpiece from a technological point of view, equipped with modern technology and controlled completely electronically.
HOW IT WORKS
The principle of the new boat lift is as simple as it is ingenious. The trough in which the boats travel within the lift is connected to counterweights by steel cables and cable pulleys. The entire system is perfectly balanced. When the counterweights travel upwards with the cables on one side, the trough travels downwards. The cable weight compensation chain, which is connected to the trough and the weights, changes the ratio of the chain length at the trough to the chain length at the weights. This compensates for the changing cable lengths and thus for the changing weights of the trough and counterweight. A small amount of electricity is needed for the lift drive, in order to get the system with its balanced weights moving.
The new Niederfinow Boat Lift is an impressive 55 metres tall. The cable weight compensation chain (right) is a core part of the weight compensation.
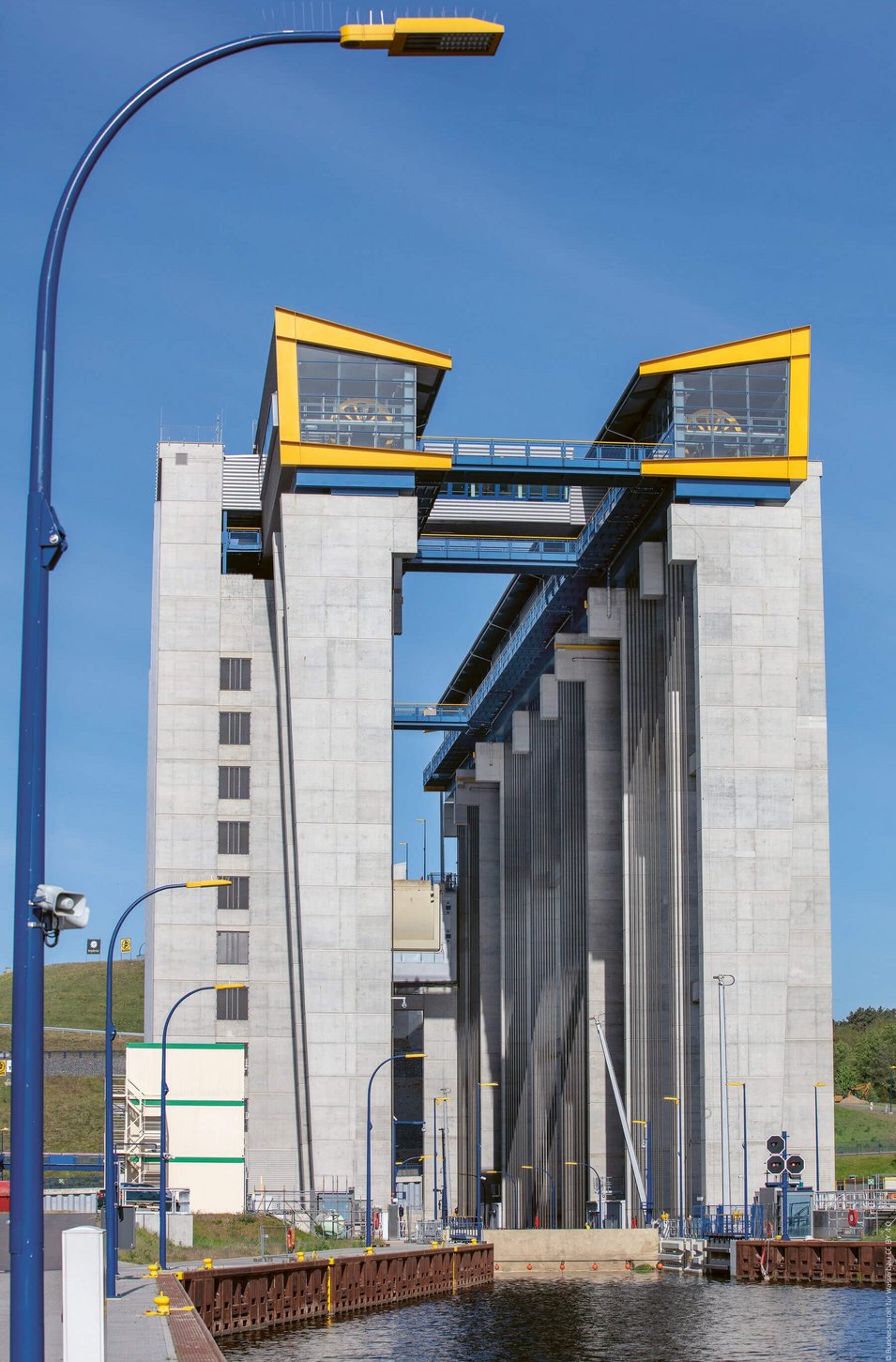
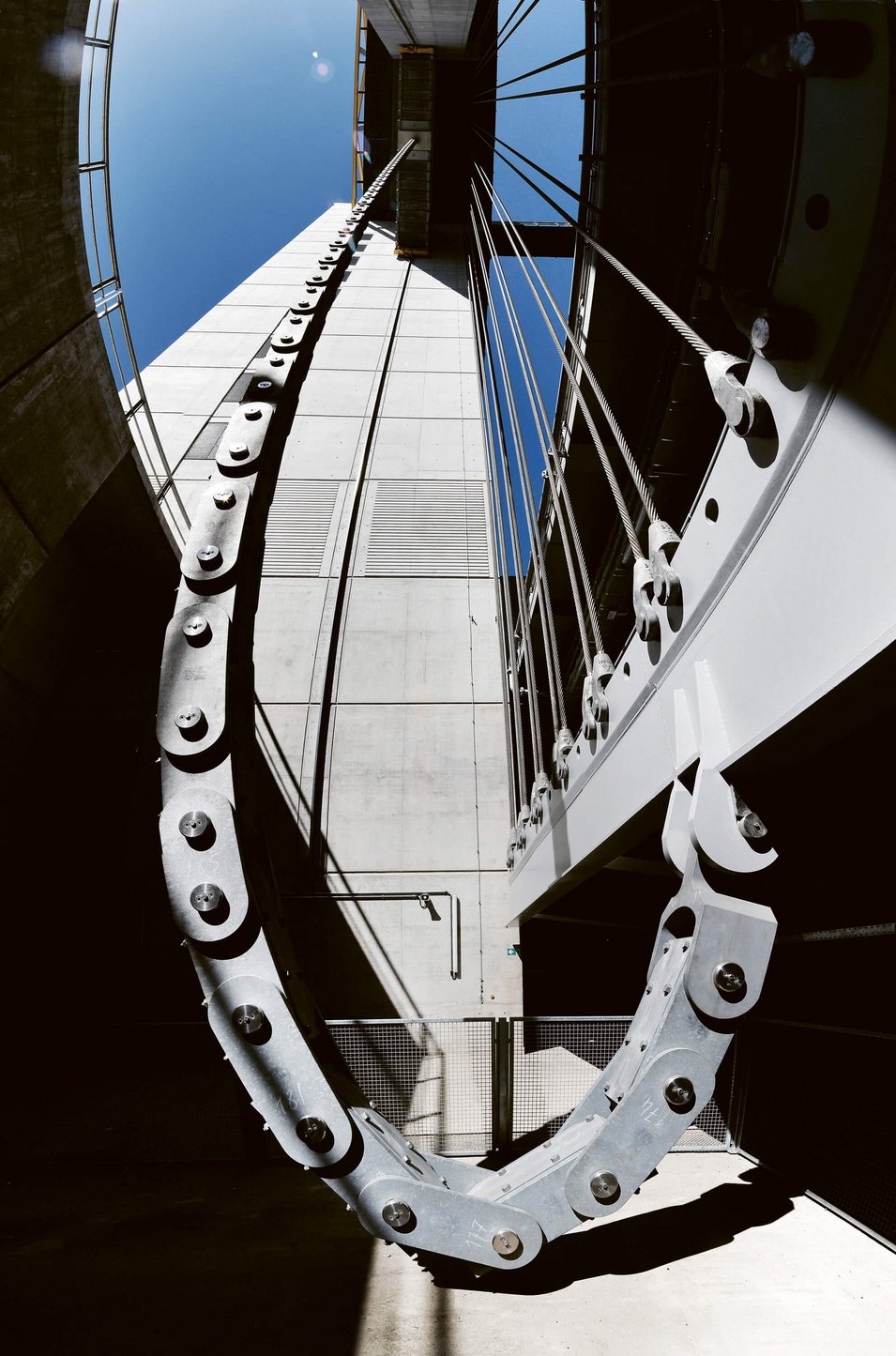
Green light for climate friendly transport
This section of the Havel-Oder Canal, which is not just a tourist magnet but also a key axis for the transportation of goods and abnormal loads between Western and Eastern Europe, can now carry up to four million tonnes of goods annually. Around 12,000 ships pass through the locks each year, a third of which are goods ships. The new boat lift thus plays a key role in protecting the environment. After all, every load transported by river boat is one more load that is not being taken by road. For comparison, a river boat has around the same load capacity as 200 trucks.
Big structure, big feelings
The complexity and imposing nature of the structure, and the time it took to complete this massive project, all trigger emotions among those involved. “We spent so much time poring over documents and plans, but when we see the lift operational and moving, it is an overwhelming feeling,” says Carsten Genetzke. He and everyone else involved share a sense of pride and of having done the right thing as a team over so many years, and having all contributed to the project’s success together.
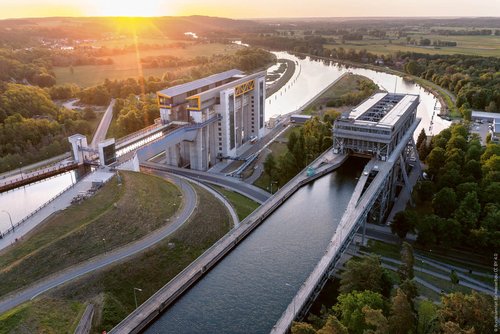
A visit is worthwhile
Are you fascinated by the old and new Niederfinow ship lift? Find out here about the current tours and guided tours on site.
Pictures: Lars Wiedemann, Bundesanstalt für Wasserbau BAW