"It was a challenge, but it worked!"
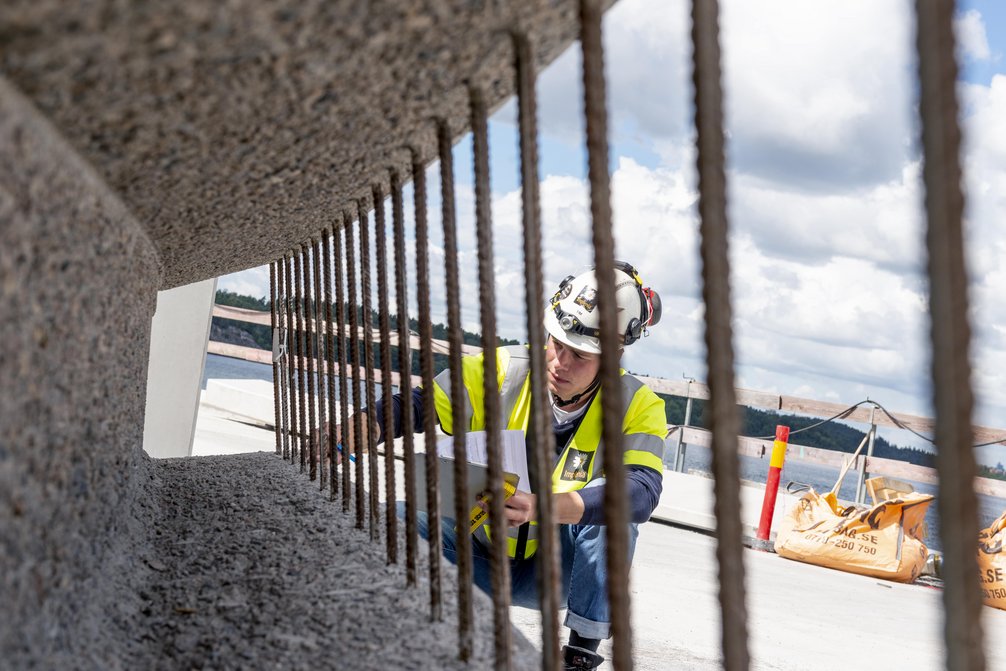
Tim Pergande comes from Germany and is at the end of his studies: all exams have been completed, now all that is missing is the diploma thesis. Between September 2021 and September 2022, the budding civil engineer will complete a one-year internship at Implenia in Sweden.
The Lilla Lidingöbron Project
Start of construction: January 2019
Length of the bridge: approx. 750 metres
Bridge width: 16 metres
Bridge piers: 12
Bridge spans: approx. 70 metres
Prefabricated elements: 450
Why an internship at Implenia?
"I wanted to do an internship abroad and there are only a few companies that offer this opportunity. Implenia is one of them and a well-known company in Germany," Tim explains. "On top of that, I preferred to do my internship on a bridge construction project. When I saw the vacancy at Lilla Lidingöbron, I naturally applied for it - and got it! "
«I wanted to do an internship abroad on a bridge construction project. There are only a few companies that offer this opportunity.»
Tim Pergande, Trainee
The 750-metre long Lidingö Bridge is Sweden's longest tram bridge. It connects the suburb of Lidingö, located on an island, with Stockholm. Tim is doing an internship in construction management, which means he supports the foremen and engineers during construction by taking responsibility for the precast elements used during construction. "I like being on the construction site, being part of the team and seeing how the project develops!" he says enthusiastically.
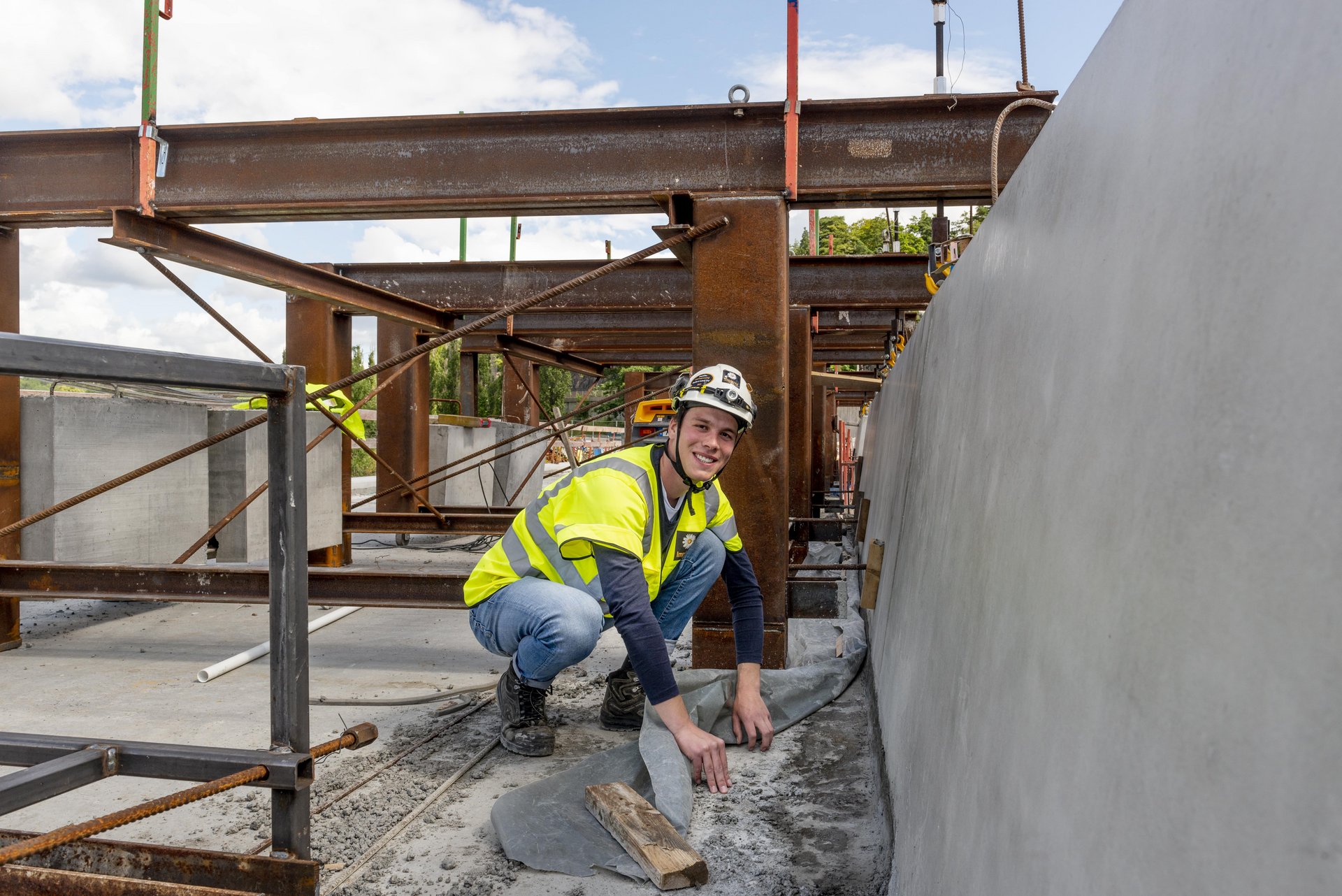
What speaks in favour of precast elements?
Prefabricated concrete elements are used for the cornice cap and the middle barrier between the tramway and the foot and cycle path. In total, about 450 elements weighing up to 5 tonnes will be installed. The solution with prefabricated elements is an efficient working method that requires fewer working hours than the conventional in-situ construction method...
In addition to the consistently high quality, the system also guarantees the desired appearance. "The prefabricated concrete elements are supplied by a precast factory from Poland. The light shade desired by the client can be achieved with the concrete formulations there."
What can the newly developed mounting frames do?
Once delivered, the prefabricated elements have to be assembled - no easy task, as Tim points out: "We had to develop an assembly system, which was quite a challenge due to the shape and weight of the elements. " The team fiddled around for a whole two months to find a suitable solution to hold the elements using a steel mounting frame that allows adjustments in height, position and inclination.
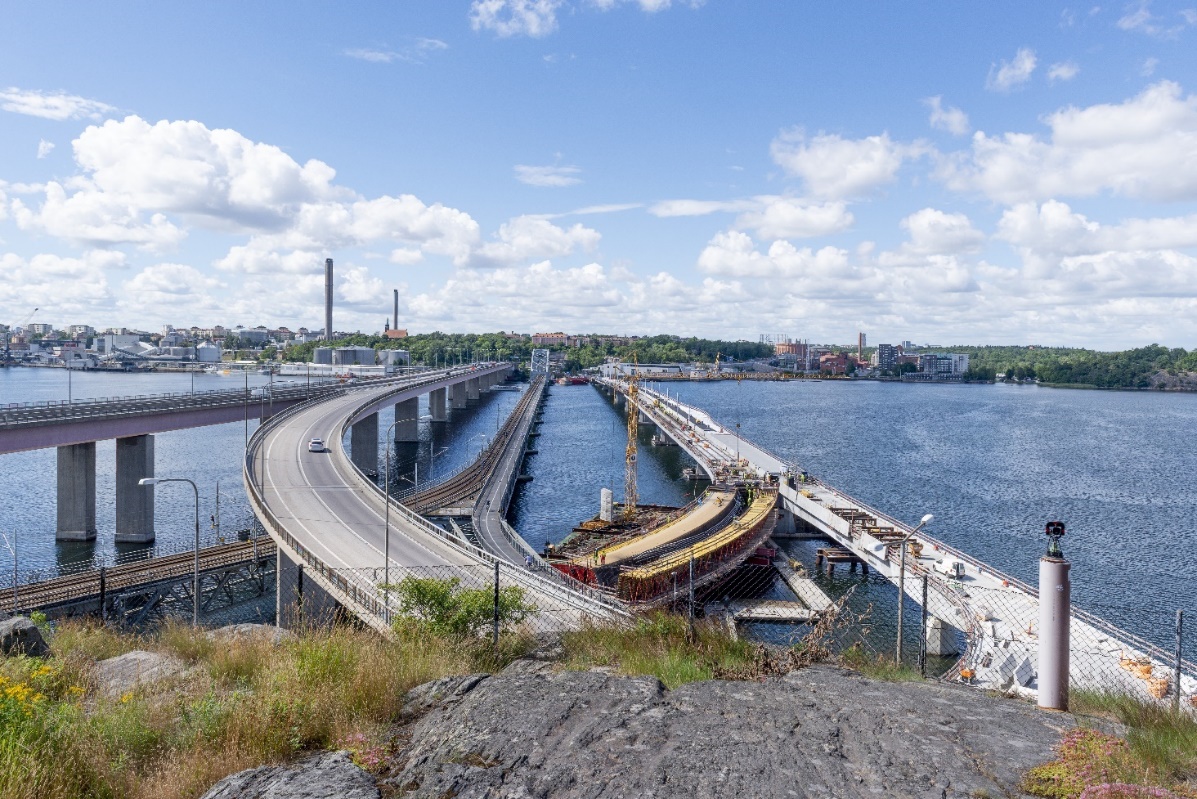
The invention was put into use at the end of last summer. In total, the team is working with eight assembly frames, which are all being used on the south side at the moment. Six elements are connected to the bridge superstructure at the same time via an in-situ concrete allowance. After concreting, it takes two days until the concrete has hardened and the assembly frames can be pushed forward. At the moment, the team is building the elements on the south side, the tram side, where only a few elements are still missing.
Challenging innovation
"We were involved in the development of the whole solution for the prefabricated elements and in the installation. It was a challenge to find the right solution, but it worked out well - that's a great feeling! ", Tim explains.
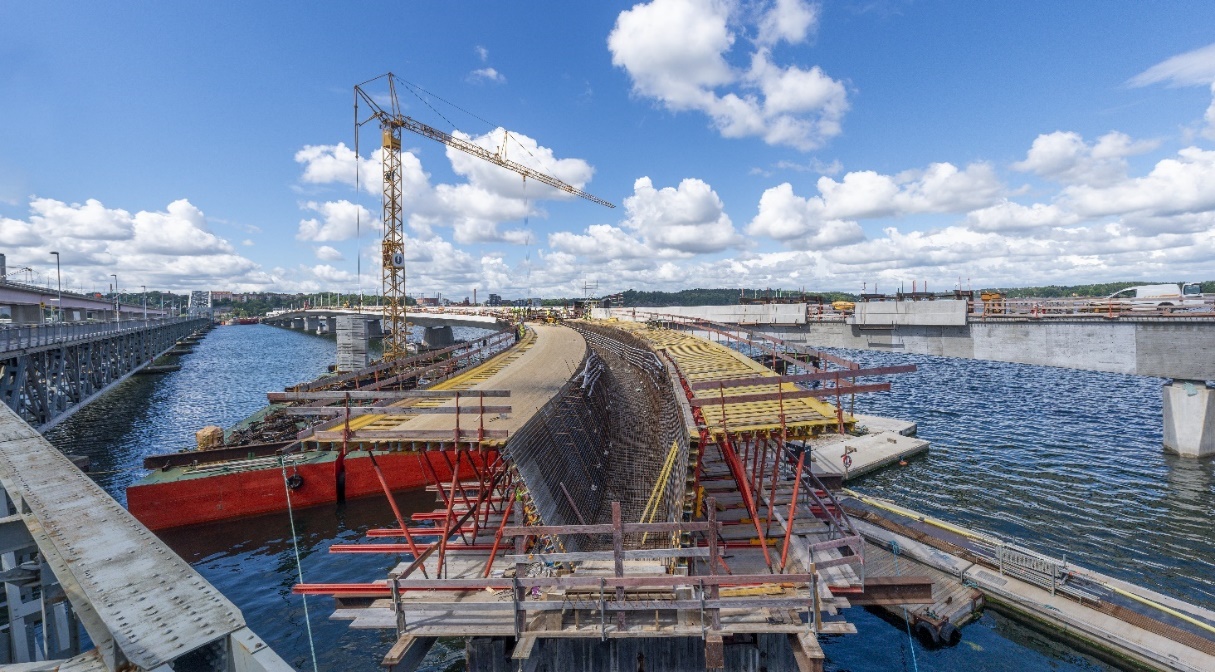
The cornice cap is now about 80% complete. The separate tram bridge will consist of another 70 prefabricated elements that will be installed as soon as this part of the bridge is finished. Tim is excited: "I'm looking forward to when the part is opened for pedestrians and cyclists. It's a milestone! "
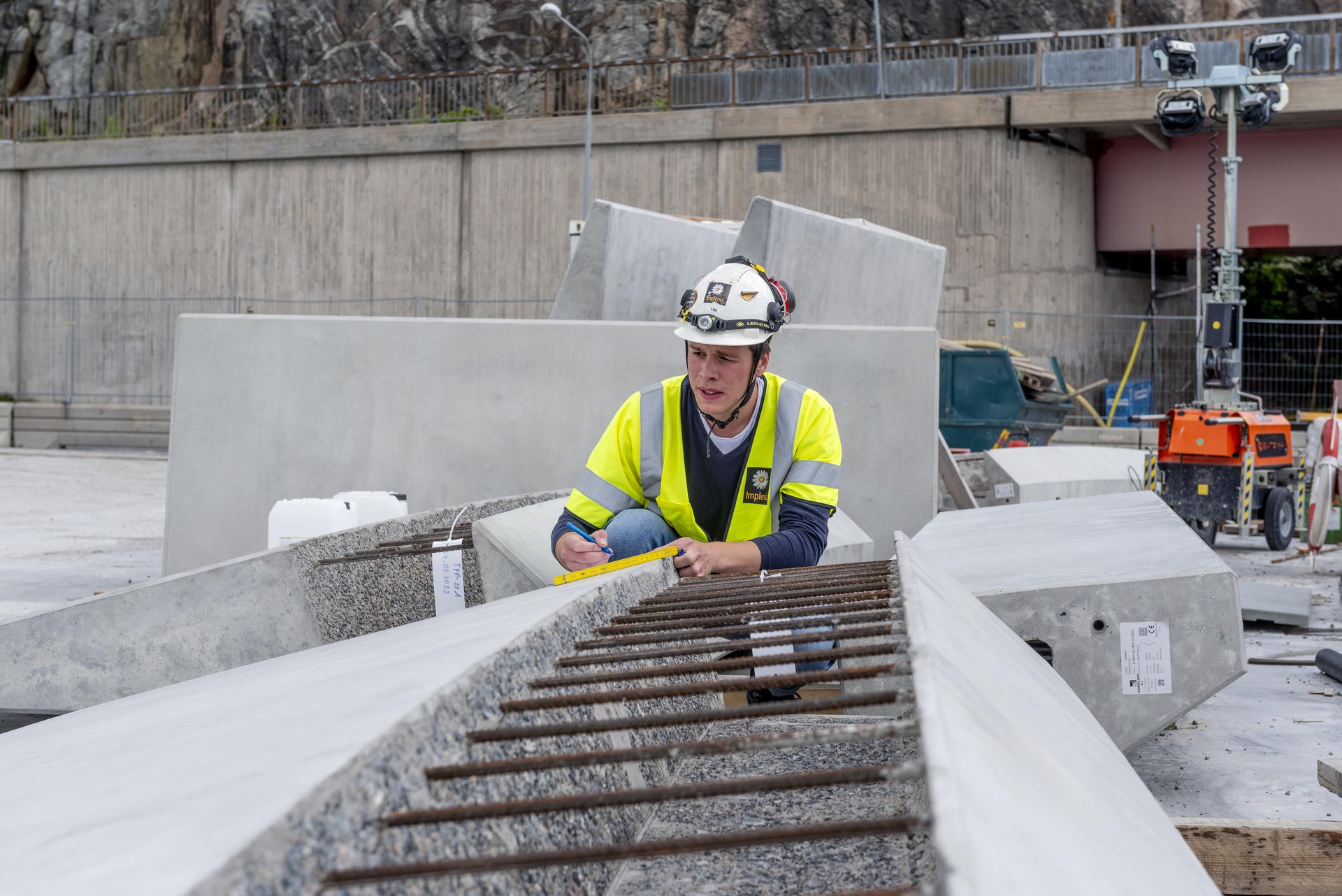