Grand Paris Express: Bohren +++ für die Pariser Metro
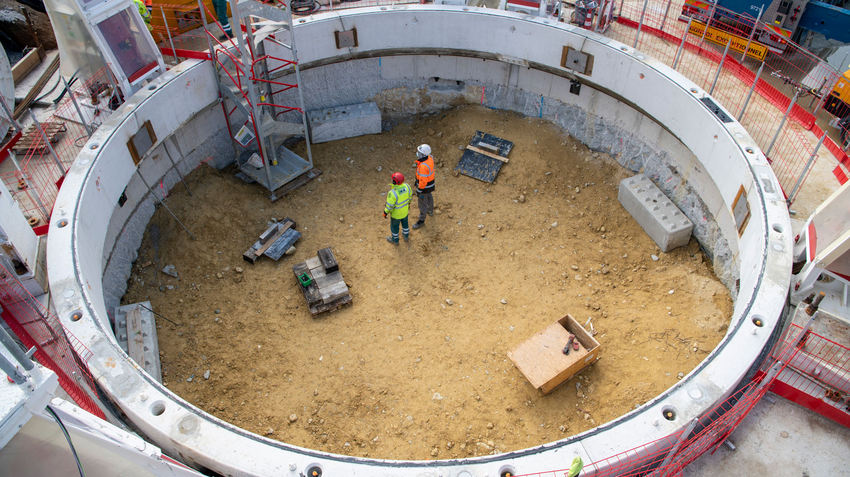
Grand Paris Express gilt als eines der ehrgeizigsten Projekte des 21. Jahrhunderts, nicht nur in Bezug auf die Grösse der Infrastruktur und des Budgets, sondern auch was die Bautechnik betrifft. Implenia ist stolz darauf, eine wichtige Rolle zu spielen, und punktet mit dem Einsatz modernster Technologie. So haben wir mit der vom deutschen Hersteller Herrenknecht entwickelten VSM-Technologie (Abkürzung für Vertical Shaft Sinking Machine) im Januar 2021 den ersten und im Mai 2021 den zweiten von insgesamt vier Schächten fertiggestellt.
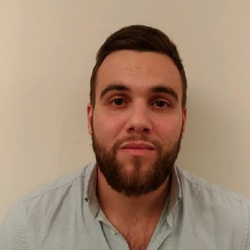
«Die VSM-Methode ermöglicht den gleichzeitigen Aushub und Einbau der Betonsegmente, die beim Aushub in den Boden getrieben werden. Das reduziert die Dauer der Arbeiten ebenso wie die Menge des verwendeten Betons, das Aushubvolumen, etc.»
Hugo Launais, Betriebsingenieur
Die VSM-Technologie ermöglicht den Bau von vertikalen Schächten unter dem Grundwasserspiegel durch Schneiden mit einer Teilschnittmaschine und von Betonsegmenten. Traditionell kommt bei dieser Art von Projekt die Schlitzwandbauweise zum Einsatz. Bei der Konfiguration der Strukturen der künftigen Metrolinie 17 liegt die Herausforderung jedoch in den beengten Platzverhältnissen. Der Einsatz der VSM-Technologie ermöglicht es, die Baustelle erheblich zu verkleinern. Gleichzeitig verkürzt sich die Bauzeit, weil Aushub und Auskleidung zeitgleich ausgeführt werden – gewichtige Vorteile bei Baustellen in beengten städtischen Gebieten. Das gilt auch für die wesentlich geringere Lärmbelästigung als beim Einsatz von Schlitzwandfräsen und Erdbewegungsgeräten. Zusätzlich erfüllt die Technologie auch noch alle Kriterien für die Höhenbeschränkungen im Umfeld des Flughafens.
So funktioniert die Technologie
Die Schachtabsenkanlage besteht aus drei Hauptkomponenten: einer Aushubeinheit; dem Abraumabfördersystem und der Absenkeinheit. Im Gegensatz zu einer horizontalen Tunnelbaumaschine ist die VSM-Anlage nicht mit einem Schneidrad ausgestattet, sondern mit einer Fräsetrommel, die an einem beweglichen Teleskoparm montiert ist und für den Aushub und Abtransport des Bodens sorgt. Das gelöste Material wird angesaugt, mit Wasser vermischt und über eine Schlauchleitung zur Separationsanlage an der Oberfläche gepumpt. Dort wird das Wasser vom Bodenmaterial getrennt und wieder zurück in den Schacht befördert. Zeitgleich erfolgt an der Oberfläche der Schachtausbau mit vorgefertigten Betonsegmenten, die kontinuierlich abgesenkt werden.
DIE TECHNOLOGIE:
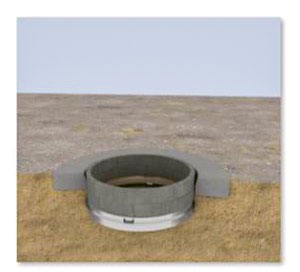
1 | Ein erster Ring des Schachtausbau, der sogenannte Schneidring, wird vor der Installation der Maschine zusammengesetzt und an der Oberfläche des Schachts platziert. Darauf werden dann weitere Ringe aufgebaut, um die Schachtbohrmaschine darin zu installieren. Diese greift mit drei Armen nach vorinstallierten Stahlteilen und verspannt sich dadurch im Schacht. Der Schacht wird durch Stahlkabel mit der Absenkeinheit verbunden und so gehalten. Damit kann diese dann kontrolliert abgesenkt oder angehoben werden. |
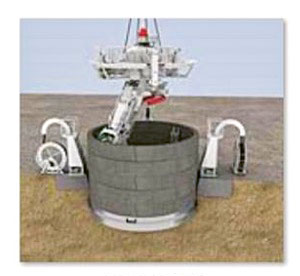
2 | Während die Schachtabsenkmaschine schrittweise den Boden abfräst, werden parallel vorgefertigte Betonsegmente, welche die Schachtwand bilden, ringförmig am oberen Ende des Schachtes installiert. Beim Absenken des Schachtes gleiten sie in das gebohrte Loch und der nächste Ring kann aufgesetzt werden. |
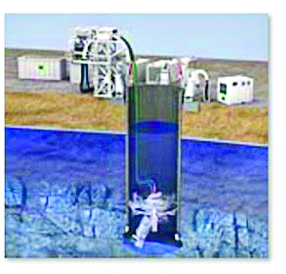
3 | Dieser Prozess wird fortgesetzt, bis der Schacht die gewünschte Tiefe erreicht. Die Schachtabsenkanlage ist so konstruiert, dass sie unter Wasser arbeitet, um den Druck auszugleichen und Bodenbewegungen zu verhindern. |
Material aus Eigenproduktion
Die Betonsegmente werden in der eigenen Produktionsstätte in Limoges-Fourches hergestellt, was uns die Kontrolle über die Planung, die Qualität der Segmente und die Haltbarkeit der Konstruktion ermöglicht. Die Segmente erfüllen die Anforderungen der Grand-Paris-Express-Spezifikationen (Lastfälle, Expositionsklasse, Materialleistung) und werden mit Verfahren der neuesten Generation hergestellt.
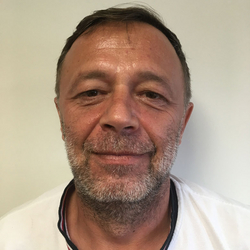
«Die Herstellung von Segmenten für den VSM erforderte Engineering-Arbeiten, um alle Komponenten zu integrieren und unsere Protokolle an die spezifischen Eigenschaften der Produkte anzupassen. Diese Entwicklungen haben es uns ermöglicht, den Prozess zu beherrschen und als einer der beiden Hersteller in Frankreich für eine technische Lösung anerkannt zu werden, an die wir glauben.»
Arnoux Cornille, Direktor von Préfa
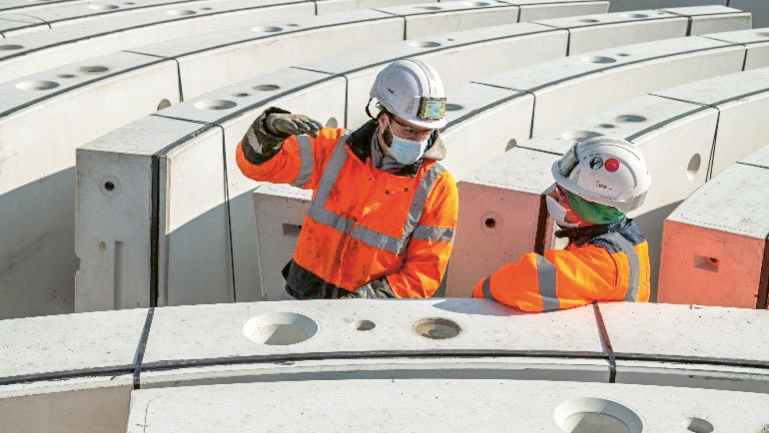
Wenn der Schacht ausgehoben ist, wird die Schachtsohle gegossen und Sperrmörtel zwischen die vertikale Wand und den Boden injiziert. Sobald diese Materialien ausgehärtet sind, wird das im Schacht enthaltene Wasser abgepumpt und die Betonsegmente sorgen dafür, dass der Schacht wasserdicht ist.
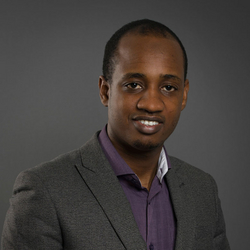
«Bei dieser Methode werden alle Arbeiten im Inneren des Bauwerks ohne Zutun von Menschen durchgeführt. So reduziert sich die Belastung unserer Leute durch Vibrationen, Staub und Dämpfe. Die Aushubarbeiten werden von der Oberfläche aus ferngesteuert und unterhalb des Grundwasserspiegels durchgeführt. Eine künstliche Absenkung des Grundwasserspiegels wird unnötig, was das Risiko von unerwarteten Setzungen stark reduziert. Und da wir weniger Aushubflüssigkeit zu bewältigen haben, ist die Methode auch umweltfreundlicher.»
Mohamed Talla, QSE Engineer
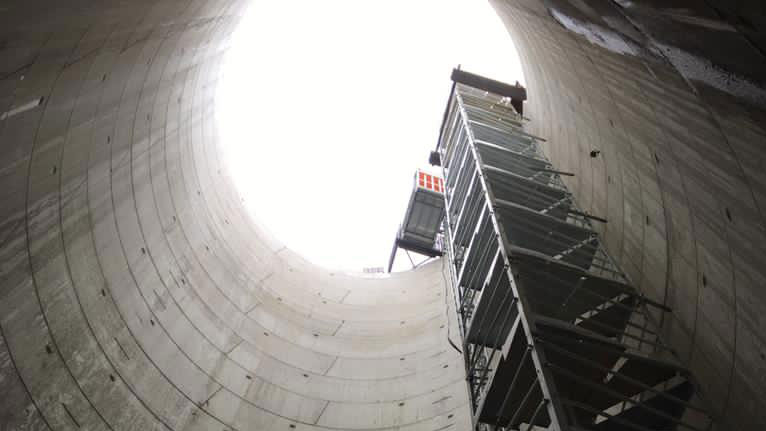
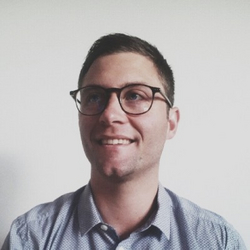
«Das Feedback der ersten abgeschlossenen Bohrung zeigt, dass diese Technik für den Pariser Untergrund gut geeignet ist. Die Bohrung verlief insgesamt gut und innerhalb des Kostenrahmens. Diese Testbohrung stimmt uns positiv im Hinblick auf die Fertigstellung der nächsten Bohrungen auf dem Gelände und wir überlegen uns den Einsatz der Technologie auch bei anderen Projekten.»
Thomas Brochot, Betriebsingenieur